1. Introduction
Automobile pollution is one of the most important issues that people are most concerned about and need to solve urgently. As an important method for detecting automobile exhaust pollutants, the simple transient operating condition method (VMAS method, IG method) can count the total mass of emissions and monitor the actual emission of vehicles. The equipment cost is not high, the measurement is relatively accurate, and it is correlated with the new car certification test results. It can detect NO related factors and other advantages, making it a hot topic for people to study. The VMAS (Vehicle Mass Analysis System) detection method has a good application basis in the United States and Europe. At present, the flow analyzers of the VMAS test system used in China are basically imported, especially the products of the American sensors company. This product is not only expensive, but also inconvenient to maintain and repair, and it is not conducive to secondary development of a complete test system with chassis dynamometers, gas analyzers, etc. To this end, we conducted research on flow analyzers, aiming to reduce equipment costs and promote the localization of products.
2. Working principle of flow analyzer
The structure of the VMAS test system is shown in Figure 1.
Figure 1 Composition of VMAS test system
The car is driven on the chassis dynamometer according to the specific working conditions required by the national standard. The chassis dynamometer simulates the acceleration inertia of the vehicle under different working conditions and the transient working load of road driving. A part of the original exhaust gas of the car directly enters the high-precision five-gas analyzer through the sampling probe to analyze the concentration values of CO, CO2, HC, NOX, and O2 in the exhaust gas. At the same time, all the remaining exhaust gas passes through the collection device, is diluted by the surrounding air, and is sent to the flow analyzer under the action of the fan to measure the volume flow of the diluted gas, and the volume flow measurement value is sent to the main control computer. At the same time, the gas concentration analysis results of the five-gas analyzer and the driving speed and mileage of the chassis dynamometer are also sent to the main control computer. The computer calculates the overall emission (g/km) of harmful gases CO, CO2, HC, and NOX in the automobile exhaust according to the gas concentration, volume, dilution ratio, speed, and time. The dilution ratio Dil is calculated according to the oxygen concentration in the air, the oxygen concentration of the mixed gas, and the oxygen concentration in the original exhaust gas of the car according to Formula 1.
(1)
3. Structural design of flow analyzer
The general vortex flow meter cannot be installed on the gas flow analyzer due to its large body and complex structure. In order to meet the use requirements, a new design idea is adopted to directly install the triangular prism vortex generator and the piezoelectric vortex detection probe on the sampling tube of the gas flow analyzer, and the structure is designed into an integrated structure, so the structure is more compact.
The overall structure of the flow analyzer is shown in Figure 2. The total length of the sampling tube is 800mm. According to the flow range of the gas during operation, the inner diameter D of the flow analyzer pipe is determined to be 100mm. The installation position of each sensor is marked in the figure.
1-Oxygen concentration sensor 2-Pressure sampling hole 3-Triangular prism vortex generator
4-Piezoelectric vortex detection probe 5-Temperature sensor
Figure 2 Overall structure of flow analyzer
The triangular prism vortex generator is selected. The vortex signal generated by this generator is strong. Because the vortex is fixed at its boundary layer separation point, the Strouhal number is relatively constant, about S1=0.16, and the linear relationship between the vortex frequency and the flow rate is good. The triangular prism is installed vertically in the gas pipeline. When the gas bypasses the spoiler column, the boundary layer separation occurs, and vortices are generated alternately behind the left and right sides of the spoiler column. According to the Karman vortex street theory, the relationship between the vortex street frequency and the flow velocity is, where: d-the base width of the triangular prism, taken as 28mm; u-the fluid flow velocity. According to the D and d values, the parameters L1, L2 and θ of the triangular prism are determined, as shown in Figure 3. [page]
Figure 3 The structure of the triangular prism (unit: mm)
According to the Reynolds number calculation formula
, where: ν-the kinematic viscosity of air, at standard pressure and 20℃, the Reynolds number corresponding to the flow range of 140m3/h~930m3/h is 3.3~21.9 ×104, which meets the upper and lower limit requirements of vortex street measurement and has an ideal instrument coefficient. The theoretically calculated instrument coefficient K is:
(3)
S1 and S2 are the cross-sectional area of the pipeline and the windward area of the triangular prism respectively. The final instrument coefficient should be based on the results of the calibration experiment.
4. Circuit design of flow analyzer
The circuit design of flow analyzer includes the selection of four sensors, flow sensor, oxygen concentration sensor, temperature sensor and pressure sensor, and the design of measurement circuit. The circuit structure block diagram is shown in Figure 4.
Figure 4 Circuit block diagram of flow analyzer
3.1 Flow sensor
The piezoelectric vortex detection method is adopted. When the gas flows through the pipeline, the vortex street generated by the triangular column periodically exerts force on the piezoelectric ceramic of the probe, causing it to generate periodically changing charges. Through the charge amplification circuit, it is filtered and shaped step by step to convert it into a corresponding square wave voltage pulse with a frequency of 44Hz to 297Hz and an amplitude of about 8.8V. The signal is isolated by photoelectric isolation, which can suppress interference from the test site on the one hand, and reduce the amplitude to below 5V on the other hand, and send it to the single-chip microcomputer for periodic measurement. Since the frequency of the vortex street is proportional to the gas flow rate, the gas volume flow rate is measured by measuring the frequency (period) of the voltage pulse.
The circuit structure of the vortex flow sensor is shown in Figure 5.
Figure 5 Schematic diagram of vortex flowmeter circuit
3.2 Oxygen sensor
A-02/T oxygen concentration sensor is used. This product is designed according to PTB 18.10 and is mainly used for automobile exhaust measurement. In a dry environment, when the oxygen concentration changes in the range of 0~100%, the output analog voltage signal is 7~13.5 mV, the response time does not exceed 5 seconds, the linear error is <0.5%, the working pressure range is 75~125kPa, and there is NTC temperature compensation. The signal is amplified by the measuring circuit, and the zero point adjustment and gain adjustment are performed to make the circuit output voltage 0~2.40V, and the corresponding oxygen concentration is 0~22.5%.
3.3 Temperature sensor
Pt100 platinum resistance is used as the temperature sensing element, and it is made into an integrated armored structure with a metal protective tube and insulating material to reduce the harmful gases and impurities in the mixed gas affecting the performance of the platinum resistance. In order to improve the temperature measurement accuracy, multi-point calibration is carried out, and the segmented linearization method is used in the software. At the same time, in order to improve the anti-interference ability of the sensor, a three-wire circuit structure is adopted. The actual test shows that the temperature measurement accuracy of the sensor is better than 1.0℃ in the range of (5~150)℃.
3.4 Pressure sensor
The MPXA6115A series on-chip integrated silicon pressure sensor is used for pressure measurement. The sensor integrates bipolar operational amplifier circuit and thin film resistor network circuit. The internal structure is shown in Figure 6. [page]
Figure 6 Internal structure of MPXA6115A
After testing, the output voltage signal of the sensor has a very good linear relationship with the input gas pressure. When the absolute pressure of the input gas changes in the range of 15kPa~115kPa, its maximum relative error is no more than 1%.
3.5 Data processing system
The C8051F021 microcontroller is used as the data processing core to complete the acquisition and processing of temperature, pressure, flow, and oxygen concentration signals. The C8051F021 microcontroller integrates a multi-channel 12-bit successive approximation ADC converter with a conversion rate of 100kps. It uses an internal voltage reference generator to generate a 2.4V high-precision reference voltage with a temperature coefficient of 15×10-6/℃. The output of the temperature, pressure, and oxygen concentration sensors is adjusted to a voltage signal of 0~2.40V after zero adjustment and gain adjustment, and enters the single-chip microcomputer for AD conversion. The accuracy of AD conversion is 0.025%. The
output of the flow sensor is a square wave voltage pulse of 44Hz to 297Hz. For signals in this frequency range, the method of measuring the cycle is more convenient and accurate. The counter TIME0 is selected for counting and period measurement. One twelfth of the main frequency of 22.1184MHz is used as the counting pulse. The 16-bit counter has a counting error of ±1, and the uncertainty of the period measurement is about 0.0000.
The single-chip microcomputer calibrates the three-way AD converted data and the period measurement value, converts them into the corresponding temperature, pressure, oxygen concentration and flow value, and transmits them to the main control computer through the serial port. The communication program between the computer and the single-chip microcomputer and the human-machine interface program are written in VB language on the control computer to display and save the measurement parameters, and an interface is left to exchange data with the control program of the five-gas analyzer and the chassis dynamometer to complete the calculation of the final emission of the vehicle.
5. Experiments and Conclusions
In order to verify the measurement accuracy of the flow analyzer, the flow, temperature, pressure, and oxygen concentration sensors of the flow analyzer were calibrated and the comprehensive accuracy was evaluated. The temperature measurement accuracy is ±1°C, the pressure measurement accuracy is better than 1%, and the oxygen concentration measurement accuracy is better than 0.5%, which fully meets the national standard requirements for test instruments.
Due to the large number of experimental projects, this article only gives the calibration experimental method and data of the main sensor vortex flow sensor.
The gas flow analyzer was installed on a pipe with a diameter of 100 mm for calibration experiments. The LXH series critical flow sonic nozzle gas flow standard device was used as the flow standard. The flow rate of the gas in the airway was adjusted by selecting different combinations of 12 sonic nozzles. Five calibration points were selected within the measurement range of 140m3/h to 930m3/h. The experimental data are shown in Table 1.
Table 1 Flow calibration experimental data
From Table 1, we can see that the average instrument system of the flow analyzer is 1159.91, and the basic error is 0.93%. Through the calibration experiment of the flow sensor in the flow analyzer, we can see that the deviation of flow measurement does not exceed 1%, which is much higher than the 5% of similar products produced by the American sensor company, and the cost is greatly reduced, which is suitable for large-scale promotion and use in China.
Previous article:Design and implementation of data acquisition module for industrial fan monitoring instrument based on MAxl320
Next article:A temperature tester based on FM20L08
Recommended ReadingLatest update time:2024-11-16 21:47
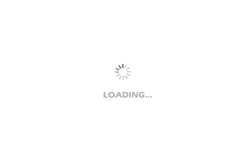
- Popular Resources
- Popular amplifiers
- Keysight Technologies Helps Samsung Electronics Successfully Validate FiRa® 2.0 Safe Distance Measurement Test Case
- From probes to power supplies, Tektronix is leading the way in comprehensive innovation in power electronics testing
- Seizing the Opportunities in the Chinese Application Market: NI's Challenges and Answers
- Tektronix Launches Breakthrough Power Measurement Tools to Accelerate Innovation as Global Electrification Accelerates
- Not all oscilloscopes are created equal: Why ADCs and low noise floor matter
- Enable TekHSI high-speed interface function to accelerate the remote transmission of waveform data
- How to measure the quality of soft start thyristor
- How to use a multimeter to judge whether a soft starter is good or bad
- What are the advantages and disadvantages of non-contact temperature sensors?
- Innolux's intelligent steer-by-wire solution makes cars smarter and safer
- 8051 MCU - Parity Check
- How to efficiently balance the sensitivity of tactile sensing interfaces
- What should I do if the servo motor shakes? What causes the servo motor to shake quickly?
- 【Brushless Motor】Analysis of three-phase BLDC motor and sharing of two popular development boards
- Midea Industrial Technology's subsidiaries Clou Electronics and Hekang New Energy jointly appeared at the Munich Battery Energy Storage Exhibition and Solar Energy Exhibition
- Guoxin Sichen | Application of ferroelectric memory PB85RS2MC in power battery management, with a capacity of 2M
- Analysis of common faults of frequency converter
- In a head-on competition with Qualcomm, what kind of cockpit products has Intel come up with?
- Dalian Rongke's all-vanadium liquid flow battery energy storage equipment industrialization project has entered the sprint stage before production
- Allegro MicroSystems Introduces Advanced Magnetic and Inductive Position Sensing Solutions at Electronica 2024
- Car key in the left hand, liveness detection radar in the right hand, UWB is imperative for cars!
- After a decade of rapid development, domestic CIS has entered the market
- Aegis Dagger Battery + Thor EM-i Super Hybrid, Geely New Energy has thrown out two "king bombs"
- A brief discussion on functional safety - fault, error, and failure
- In the smart car 2.0 cycle, these core industry chains are facing major opportunities!
- The United States and Japan are developing new batteries. CATL faces challenges? How should China's new energy battery industry respond?
- Murata launches high-precision 6-axis inertial sensor for automobiles
- Ford patents pre-charge alarm to help save costs and respond to emergencies
- New real-time microcontroller system from Texas Instruments enables smarter processing in automotive and industrial applications
- This flyback switching power supply based on TinySwitch-III
- RF wireless transmission distance
- TMS320C6678 Evaluation Module
- Data collection and display of dsp
- Power Supply Problem Summary
- The one with the highest score wins: ST Sensors Conquer the World: Driver Transplantation Competition + Bone Vibration Sensor Evaluation
- [RVB2601 Creative Application Development] Experience Sharing 1: Unboxing, Environment Building, and Outputting HelloWorld
- Award-winning live broadcast: Application of TI mmWave radar sensors in smart home and smart security
- The 10 Best Pico Accessories of 2021
- Yole: GaN RF market size will exceed $2 billion in 2025