1 System hardware design
The system hardware circuit is shown in Figure 1. It mainly consists of five parts: a solar cell group, a Hall current sensor, an I/U conversion circuit, a display device composed of a liquid crystal 1602, a control system composed of an AT89S52 single-chip microcomputer, and an energy storage system composed of a lead-acid battery. Its working process: When the solar cell receives light, it generates current to charge the battery. The microcontroller uses the voltage stabilizing device to provide driving voltage from the battery to collect real-time signals of the amount of electricity generated by the solar cell. Since the microcontroller can only receive voltage signals, the I/U and U/U conversion modules adjust the signal to a suitable voltage before receiving the signal. After internal calculation processing, the result is sent to the 1602 LCD display device to display the battery power generation.
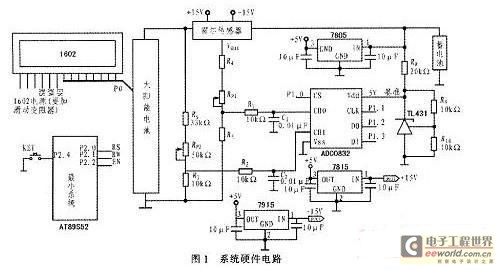
1.1 A/D conversion module
After the analog signal is input into the microcontroller, it needs to be converted into a digital signal. Since the output voltage and current of the solar cell need to be measured at the same time, ADC0832 is an 8-bit serial dual-channel A/D converter. The A/D conversion accuracy depends on the reference voltage with high stability. The reference voltage is set to 5 V and is generated by TL431. The analog signal is sent to the AD input terminal after RC filtering, and then the analog-to-digital conversion is performed and the serial output is output.
1.2 I/U conversion module
Because the I/O interface of the microcontroller can only receive 0-5 V voltage signals, the real-time acquisition of the output current of the solar cell requires the current signal to be converted into a voltage signal. Since this system is an auxiliary device for the photovoltaic power generation system, reducing energy consumption as much as possible is the primary issue. Therefore, the Hall current sensor becomes the first choice. It works according to the Hall effect principle and can convert the current signal into a voltage signal without consuming almost any energy. This system uses the TBCl0SY type Hall current sensor with a rated output voltage of (±4±0.5%)V, ±15 V dual power supply, and a measurement current range of 0-15 A, which basically meets the application of small off-grid photovoltaic systems. [page]
1.3 Power supply design
For the normal operation of the single-chip microcomputer, it is necessary to supply power to the transistors or field effect tubes in the chip so that they can work in the corresponding state. AT89S52 requires a 5 V power supply (the actual working voltage is 3.6~6.0 V). It can be powered by rectification and voltage regulation to obtain a voltage of about 4.5 V. Because this system is an independent power generation and is used for a long time, considering the life of the power supply, it is not practical for the device to be driven by the mains or dry batteries. Therefore, the best solution should be powered by the battery of the solar cell inside the system, which is stabilized to 5 V by the voltage regulator integrated block 7805 and input to the Vcc pin of the single-chip microcomputer to drive the single-chip microcomputer and the liquid crystal display device. The TBCl0SY Hall current sensor requires a ±15 V dual power supply, which is also powered by the battery in the system. It is stabilized at ±15 V by the voltage regulator integrated blocks 7805 and 7915, thereby driving it to work.
1.4 Output display module
The power calculation formula is Q=UIT, where the time T can be determined by the software programming according to the needs, such as sampling every 3 minutes, and sending it to the 1602 LCD to display the power generation after internal calculation. In order to save energy, the LCD display is set to automatically turn off after 10 seconds.
2 System software design
The system software design is mainly completed by the single-chip microcomputer, which mainly realizes data acquisition and control display. The entire software system design adopts modularization thinking. The measurement and display program flow is shown in Figure 2.
3 System test analysis
Take a 200 W small off-grid photovoltaic system as an example, with a rated voltage of 24 V, a maximum current of 6.18 A, and a battery of 200 Ah. The normal discharge time is designed to be 2 to 3 days. The current of 0 to 6.18 A is converted into a voltage of 0 to 5 V in proportion. The attenuator is composed of two resistors. The output voltage amplification ratio is determined by the ratio of resistors R1 and R2. The U/U conversion ratio is set to 5/24, then R7=10 kΩ, R6+Rp2=48 kΩ. According to the power calculation formula Q=UIT, the experimental time is from 12 noon to 2 pm. Starting from the display of power, the actual power and the data displayed by the monitoring system are recorded every 3 minutes. The error of each time is less than 3%. Table 1 shows the initial 10 measurement errors. As the power gradually increases, the error range gradually decreases.
4 Conclusions
The real-time monitoring system of solar cell power generation composed of AT89S52 microcontroller, Hall current sensor and 1602 LCD has a simple structure, low cost, maintenance-free, low power consumption, and can effectively monitor the power generation of solar cells in real time, and detect abnormal conditions in the operation of solar cells as soon as possible. The system is designed as an auxiliary component of a photovoltaic system and is suitable for small off-grid photovoltaic systems. At the same time, the system devices have a long life, are durable and reliable, and are widely used in off-grid photovoltaic systems.
Previous article:Design of digital temperature measurement system based on platinum resistance
Next article:Multi-resolution display design and compatibility testing on Android platform
- Keysight Technologies Helps Samsung Electronics Successfully Validate FiRa® 2.0 Safe Distance Measurement Test Case
- From probes to power supplies, Tektronix is leading the way in comprehensive innovation in power electronics testing
- Seizing the Opportunities in the Chinese Application Market: NI's Challenges and Answers
- Tektronix Launches Breakthrough Power Measurement Tools to Accelerate Innovation as Global Electrification Accelerates
- Not all oscilloscopes are created equal: Why ADCs and low noise floor matter
- Enable TekHSI high-speed interface function to accelerate the remote transmission of waveform data
- How to measure the quality of soft start thyristor
- How to use a multimeter to judge whether a soft starter is good or bad
- What are the advantages and disadvantages of non-contact temperature sensors?
- Innolux's intelligent steer-by-wire solution makes cars smarter and safer
- 8051 MCU - Parity Check
- How to efficiently balance the sensitivity of tactile sensing interfaces
- What should I do if the servo motor shakes? What causes the servo motor to shake quickly?
- 【Brushless Motor】Analysis of three-phase BLDC motor and sharing of two popular development boards
- Midea Industrial Technology's subsidiaries Clou Electronics and Hekang New Energy jointly appeared at the Munich Battery Energy Storage Exhibition and Solar Energy Exhibition
- Guoxin Sichen | Application of ferroelectric memory PB85RS2MC in power battery management, with a capacity of 2M
- Analysis of common faults of frequency converter
- In a head-on competition with Qualcomm, what kind of cockpit products has Intel come up with?
- Dalian Rongke's all-vanadium liquid flow battery energy storage equipment industrialization project has entered the sprint stage before production
- Allegro MicroSystems Introduces Advanced Magnetic and Inductive Position Sensing Solutions at Electronica 2024
- Car key in the left hand, liveness detection radar in the right hand, UWB is imperative for cars!
- After a decade of rapid development, domestic CIS has entered the market
- Aegis Dagger Battery + Thor EM-i Super Hybrid, Geely New Energy has thrown out two "king bombs"
- A brief discussion on functional safety - fault, error, and failure
- In the smart car 2.0 cycle, these core industry chains are facing major opportunities!
- The United States and Japan are developing new batteries. CATL faces challenges? How should China's new energy battery industry respond?
- Murata launches high-precision 6-axis inertial sensor for automobiles
- Ford patents pre-charge alarm to help save costs and respond to emergencies
- New real-time microcontroller system from Texas Instruments enables smarter processing in automotive and industrial applications
- AMS1117 step-down circuit
- Installation and calibration methods of wireless pressure transmitter!
- How to choose the inductor of the RF antenna of Bluetooth products
- NUCLEO_G431RB Review - SPI Operation of SSD1306, OLED
- EEWORLD University Hall----Radiation Hardness Assurance (RHA) Process of TI Space Products
- 【NXP Rapid IoT Review】Environmental Quality Test
- [ATmega4809 Curiosity Nano Review] Installing MCC
- GD32E231C-START Unboxing
- X-NUCLEO-IKS01A3 sensor test based on STM32F401RE development board 5L
- Simulation failed with no results