0 Introduction
Sensor circuits are usually used to measure weak signals and have high sensitivity, but they are also easy to receive some irregular noise or interference signals from the outside or inside. If the size of these noise and interference can be compared with the useful signal, then the useful signal at the output end of the sensor circuit may be submerged, or because the useful signal component and the noise interference component are difficult to distinguish, it will inevitably hinder the measurement of the useful signal. Therefore, in the design of sensor circuits, anti-interference design is often the key to the success of sensor circuit design.
1 Internal noise of sensor circuits
1.1 High-frequency thermal noise
High-frequency thermal noise is caused by the irregular movement of electrons inside the conductor. The higher the temperature, the more intense the electron movement. The irregular movement of electrons inside the conductor will form many tiny current fluctuations inside it. Because it is disordered movement, its average total current is zero, but when it is connected to the amplifier circuit as a component (or as part of the circuit), its internal current will be amplified and become a noise source, especially for circuits working in the high-frequency band. High-frequency thermal noise has a particularly strong impact.
Usually within the power frequency, the thermal noise of the circuit is proportional to the passband. The wider the passband, the greater the impact of the thermal noise of the circuit. Within the passband △f, the effective value of the thermal noise voltage of the circuit is:. Taking a 1 kΩ resistor as an example, if the passband of the circuit is 1 MHz, the effective value of the open-circuit voltage noise presented at both ends of the resistor is 4μV (assuming the temperature is room temperature T=290 K). It seems that the electromotive force of the noise is not large, but if it is connected to an amplifier circuit with a gain of 106 times, its output noise can reach 4 V, and the interference to the circuit is very large.
1.2 Low-frequency noise
Low-frequency noise is mainly caused by the discontinuity of the conductive particles inside. In particular, carbon film resistors have many tiny particles inside their carbonaceous materials, and the particles are discontinuous. When current flows through, the conductivity of the resistor will change, causing the current to change, and producing a flash arc similar to poor contact. In addition, transistors may also produce similar burst noise and flicker noise. The generation mechanism is similar to the discontinuity of the particles in the resistor and is also related to the doping degree of the transistor.
1.3 Shot noise generated by semiconductor devices
Due to the change in the voltage of the barrier region at both ends of the semiconductor PN junction, the amount of charge accumulated in this region changes, thus showing the capacitance effect. When the external forward voltage increases, the electrons in the N region and the holes in the P region move to the depletion region, which is equivalent to charging the capacitor. When the forward voltage decreases, it makes the electrons and holes move away from the depletion region, which is equivalent to discharging the capacitor. When the reverse voltage is applied, the change in the depletion region is opposite. When the current flows through the barrier region, this change will cause the current flowing through the barrier region to produce a small fluctuation, thereby generating current noise. The size of the noise generated is proportional to the temperature and the bandwidth △f.
1.4 Interference of electromagnetic components on circuit boards
Many circuit boards have electromagnetic components such as relays and coils. When the current passes through, the inductance of the coil and the distributed capacitance of the shell radiate energy to the surroundings, and the energy will interfere with the surrounding circuits. Components such as relays work repeatedly, and when the power is turned on and off, a momentary reverse high voltage will be generated, forming a momentary surge current. This momentary high voltage will have a great impact on the circuit, thereby seriously interfering with the normal operation of the circuit.
1.5 Noise of resistors
The interference of resistors comes from the inductance and capacitance effects in the resistors and the thermal noise of the resistors themselves. For example, a solid core resistor with a resistance value of R can be equivalent to the series and parallel connection of resistor R, parasitic capacitance C, and parasitic inductance L. Generally speaking, the parasitic capacitance is 0.1-0.5 pF and the parasitic inductance is 5-8 nH. When the frequency is higher than 1 MHz, these parasitic inductance and capacitance cannot be ignored.
All kinds of resistors will generate thermal noise. When a resistor with a resistance value of R (or the body resistance of BJT, the channel resistance of FET) is not connected to the circuit, the thermal noise voltage generated within the bandwidth B is:
Where: k is the Boltzmann constant; T is the absolute temperature (unit: K). The thermal noise voltage itself is a non-periodic time function, so its frequency range is very wide. Therefore, wide-band amplifier circuits are more affected by noise than narrow-band circuits.
In addition, the resistor will also generate contact noise, and its contact noise voltage is:
where I is the mean square value of the current flowing through the resistor; f is the center frequency; k is a constant related to the geometry of the material. Since Vc plays an important role in the low frequency band, it is the main noise source of the low-frequency sensor circuit.
[page]
0 Introduction
Sensor circuits are usually used to measure weak signals and have high sensitivity, but they are also easy to receive some irregular noise or interference signals from the outside or inside. If the size of these noise and interference can be compared with the useful signal, then the useful signal at the output end of the sensor circuit may be submerged, or because the useful signal component and the noise interference component are difficult to distinguish, it will inevitably hinder the measurement of the useful signal. Therefore, in the design of sensor circuits, anti-interference design is often the key to the success of sensor circuit design.
1 Internal noise of sensor circuits
1.1 High-frequency thermal noise
High-frequency thermal noise is caused by the irregular movement of electrons inside the conductor. The higher the temperature, the more intense the electron movement. The irregular movement of electrons inside the conductor will form many tiny current fluctuations inside it. Because it is disordered movement, its average total current is zero, but when it is connected to the amplifier circuit as a component (or as part of the circuit), its internal current will be amplified and become a noise source, especially for circuits working in the high-frequency band. High-frequency thermal noise has a particularly strong impact.
Usually within the power frequency, the thermal noise of the circuit is proportional to the passband. The wider the passband, the greater the impact of the thermal noise of the circuit. Within the passband △f, the effective value of the thermal noise voltage of the circuit is:. Taking a 1 kΩ resistor as an example, if the passband of the circuit is 1 MHz, the effective value of the open-circuit voltage noise presented at both ends of the resistor is 4μV (assuming the temperature is room temperature T=290 K). It seems that the electromotive force of the noise is not large, but if it is connected to an amplifier circuit with a gain of 106 times, its output noise can reach 4 V, and the interference to the circuit is very large.
1.2 Low-frequency noise
Low-frequency noise is mainly caused by the discontinuity of the conductive particles inside. In particular, carbon film resistors have many tiny particles inside their carbonaceous materials, and the particles are discontinuous. When current flows through, the conductivity of the resistor will change, causing the current to change, and producing a flash arc similar to poor contact. In addition, transistors may also produce similar burst noise and flicker noise. The generation mechanism is similar to the discontinuity of the particles in the resistor and is also related to the doping degree of the transistor.
1.3 Shot noise generated by semiconductor devices
Due to the change in the voltage of the barrier region at both ends of the semiconductor PN junction, the amount of charge accumulated in this region changes, thus showing the capacitance effect. When the external forward voltage increases, the electrons in the N region and the holes in the P region move to the depletion region, which is equivalent to charging the capacitor. When the forward voltage decreases, it makes the electrons and holes move away from the depletion region, which is equivalent to discharging the capacitor. When the reverse voltage is applied, the change in the depletion region is opposite. When the current flows through the barrier region, this change will cause the current flowing through the barrier region to produce a small fluctuation, thereby generating current noise. The size of the noise generated is proportional to the temperature and the bandwidth △f.
1.4 Interference of electromagnetic components on circuit boards
Many circuit boards have electromagnetic components such as relays and coils. When the current passes through, the inductance of the coil and the distributed capacitance of the shell radiate energy to the surroundings, and the energy will interfere with the surrounding circuits. Components such as relays work repeatedly, and when the power is turned on and off, a momentary reverse high voltage will be generated, forming a momentary surge current. This momentary high voltage will have a great impact on the circuit, thereby seriously interfering with the normal operation of the circuit.
1.5 Noise of resistors
The interference of resistors comes from the inductance and capacitance effects in the resistors and the thermal noise of the resistors themselves. For example, a solid core resistor with a resistance value of R can be equivalent to the series and parallel connection of resistor R, parasitic capacitance C, and parasitic inductance L. Generally speaking, the parasitic capacitance is 0.1-0.5 pF and the parasitic inductance is 5-8 nH. When the frequency is higher than 1 MHz, these parasitic inductance and capacitance cannot be ignored.
All kinds of resistors will generate thermal noise. When a resistor with a resistance value of R (or the body resistance of BJT, the channel resistance of FET) is not connected to the circuit, the thermal noise voltage generated within the bandwidth B is:
Where: k is the Boltzmann constant; T is the absolute temperature (unit: K). The thermal noise voltage itself is a non-periodic time function, so its frequency range is very wide. Therefore, wide-band amplifier circuits are more affected by noise than narrow-band circuits.
In addition, the resistor will also generate contact noise, and its contact noise voltage is:
where I is the mean square value of the current flowing through the resistor; f is the center frequency; k is a constant related to the geometry of the material. Since Vc plays an important role in the low frequency band, it is the main noise source of the low-frequency sensor circuit.
[page]
3.2 Select appropriate amplifier circuits according to different working frequency bands and parameters
Selecting appropriate amplifier circuits not only has a direct impact on the circuit at this level, but also has an important impact on the working parameters and working state of the entire circuit. For example, when connected in a common emitter configuration, the circuit has a higher amplifier gain, and its noise has less impact on the subsequent stage. When connected in a common collector configuration, it has a higher input impedance and a better frequency response. Therefore, different circuits should have different requirements for parameters. Selecting a good circuit can not only simplify the circuit structure, but also reduce the interference of noise on the entire circuit. Under the condition that the circuit performance parameters allow, digital circuits with good anti-interference ability should be used as much as possible.
3.3 Add filtering links to sensor circuits
In the amplifier circuit, the wider the frequency band, the greater the noise, and the frequency of the useful signal is often within a certain range. Therefore, a filtering link can be added to the circuit to filter out or attenuate the interference signal as much as possible to achieve the purpose of improving the signal-to-noise ratio and suppressing interference. Filtering technology is particularly effective in suppressing interference coupled to the circuit through wires. Connecting filters of the corresponding frequency band to the signal transmission channel, various filters are one of the effective measures to suppress differential mode interference. Commonly used filters in automatic detection systems are:
(1) RC filters. When the signal source is a sensor with slow signal changes, such as a thermocouple or strain gauge, a small-volume, low-cost passive RC filter will have a good suppression effect on cross-mode interference.
(2) AC power filter. The power supply network absorbs various high- and low-frequency noises. LC filters are often used to suppress the noise mixed into the power supply. For example, a high-frequency filter composed of a 100μH inductor and a 0.1 μF capacitor can absorb high-frequency noise interference in the medium and short wave bands.
(3) DC power filter. The DC power supply is often shared by several circuits. In order to avoid mutual interference between several circuits through the internal resistance of the power supply, an RC or LC decoupling filter should be added to the DC power supply of each circuit to filter out low-frequency noise.
3.4 Suppressing noise through negative feedback circuits
Negative feedback circuits can stabilize the circuit by sampling and controlling the feedback signal, improve the signal-to-noise ratio of the amplifier, and improve the dynamic performance of the amplifier circuit in many aspects. The negative feedback signal can stabilize the static operating point of the circuit, thereby stabilizing multiple parameters such as the temperature, current, and voltage of the circuit. In a multi-stage circuit, the first stage circuit is a small original signal, so a common emitter circuit configuration with a large gain is often used. Unless there is a special need, the common emitter configuration circuit is often not negatively fed back. Therefore, the noise generated by the first stage circuit can only be suppressed by the negative feedback circuit of the next stage. For a multi-stage circuit, the generation and propagation of the circuit noise of this stage can be suppressed by stabilizing the static operating point of this stage through the negative feedback signal. Therefore, in a multi-stage circuit, the negative feedback circuit is an important means to suppress noise.
3.5 Suppressing and reducing the noise of the input bias circuit
The input bias circuit noise is generally generated by the input bias shunt resistor. When the DC current flowing through the bias resistor is too large, it will cause excess energy and generate current noise. If a suitable bias circuit is selected, the noise can be short-circuited to the ground through the bypass capacitor, which can suppress the noise output and reduce the impact on the next stage circuit. In addition, a high-quality signal source is also an important guarantee for the circuit to resist interference.
4 Measures to reduce interference in sensor circuits
4.1 Reasonable layout
Reasonable circuit layout can reduce mutual interference between circuits in different working frequency bands, and also make filtering interference signals relatively simple.
4.1.1 Anti-interference measures for ground wire layout
In order to overcome the interference caused by unreasonable ground wire layout, when designing printed circuits, it is necessary to avoid circuits of different loops flowing through a certain common ground wire at the same time. Especially in high-frequency circuits and high-current circuits, it is more important to pay attention to the connection method of the ground wire. Separating "AC ground" and "DC ground" is an effective way to reduce noise crosstalk through the ground wire.
4.1.2 Anti-interference measures for power supply wiring
When wiring, first separate the AC power supply part from the DC power supply part, and do not share the ground wire, that is, separate the "AC ground" and "DC ground" to reduce noise crosstalk through the ground wire. In addition, in the DC power supply circuit, load changes will cause power supply noise. Configuring decoupling capacitors can suppress the noise generated by load changes. The specific configuration method is to connect a 10-100μF electrolytic capacitor to the power input terminal. If the position of the printed circuit board allows, the anti-interference effect of using an electrolytic capacitor of more than 100μF will be better. When routing the power line, according to the current size of the printed circuit board, try to increase the width of the power line to reduce the loop resistance. At the same time, make the routing of the power line and the ground line consistent with the direction of data signal transmission, which will help enhance the anti-interference ability.
4.1.3 Anti-interference measures for component layout
(1) Suppress electromagnetic interference. Components that may affect or interfere with each other should be separated as much as possible or shielded. Try to shorten the connection between high-frequency components to reduce their distributed parameters and mutual electromagnetic interference (if a metal shielding cover is required for the high-frequency part, the area occupied by the shielding cover should be reserved on the board). Components that are susceptible to interference should not be too close. The components of the strong current part (220 V) and the weak current part (DC power supply), input stage and output stage should be separated as much as possible. When the DC power supply lead is long, add filtering components to prevent 50 Hz interference. Components such as speakers, electromagnets, and permanent magnet instruments will generate constant magnetic fields, while high-frequency transformers and relays will generate alternating magnetic fields. These magnetic fields will not only interfere with surrounding components, but also affect surrounding printed wires. This type of interference should be treated differently according to the situation. Generally, several points should be noted: reduce the cutting of magnetic lines on printed wires. When determining the positions of two inductance components, try to make their magnetic field directions perpendicular to each other to reduce coupling between each other; magnetically shield the interference source, and the shielding cover should be well grounded; when using high-frequency cables to directly transmit signals, the shielding layer of the cable should be grounded at one end.
(2) Suppress thermal interference. Interference caused by temperature rise should also be paid attention to in printed board design. When designing printed boards, measures should be taken to thermally isolate components. For example, temperature-sensitive components such as transistors, integrated circuits and other heat-sensitive components, large-capacity electrolytic capacitors, etc. should not be placed near heat sources or on the upper part of the equipment. The temperature rise caused by long-term operation of the circuit will affect the working state and performance of these components.
4.2 Shielding technology
Shielding technology can effectively prevent interference from electric or magnetic fields. Shielding can be divided into electrostatic shielding, electromagnetic shielding and low-frequency magnetic shielding.
4.2.1 Electrostatic shielding
Use copper or aluminum and other metals with good conductivity as materials to make a closed metal container, connect it to the ground wire, and place the circuit to be protected in it so that the external interference electric field does not affect its internal circuit. Conversely, the electric field generated by the internal circuit will not affect the external circuit. For example, in the sensor measurement circuit, insert a conductor with a gap between the primary and secondary of the power transformer and ground it to prevent electrostatic coupling between the two windings. [page]
4.2.2 Electromagnetic shielding
For high-frequency interference magnetic fields, the eddy current principle is used to make the high-frequency interference electromagnetic field generate eddy currents in the shielding metal, consume the energy of the interference magnetic field, and the eddy current magnetic field offsets the high-frequency interference magnetic field, thereby protecting the protected circuit from the influence of the high-frequency electromagnetic field. If the electromagnetic shielding layer is grounded, it also has the function of electrostatic shielding. The output cable of the sensor generally adopts a copper mesh shield, which has both electrostatic shielding and electromagnetic shielding. The shielding material must be a low-resistance material with good conductivity, such as copper, aluminum or silver-plated copper.
4.2.3 Low-frequency magnetic shielding
If the interference is a low-frequency magnetic field, the eddy current phenomenon is not very obvious at this time, and the anti-interference effect of the above method alone is not very good. Therefore, it is necessary to use a high magnetic permeability material as a shielding layer to limit the low-frequency interference magnetic flux lines within the magnetic shielding layer with very small magnetic resistance, so that the protected circuit is protected from the influence of low-frequency magnetic field coupling interference. The iron shell of the sensor detection instrument plays the role of low-frequency magnetic shielding. If it is further grounded, it also plays the role of electrostatic shielding and electromagnetic shielding.
Based on the above three commonly used shielding technologies, composite shielded cables can be used in places where interference is more serious, that is, the outer layer is a low-frequency magnetic shielding layer, and the inner layer is an electromagnetic shielding layer, so as to achieve the effect of double shielding. For example, the parasitic capacitance of capacitive sensors is a key problem that must be solved in actual measurement, otherwise its transmission efficiency and sensitivity will be reduced. The sensor must be electrostatically shielded, and its electrode lead wire adopts double-layer shielding technology, which is generally called drive cable technology. This method can effectively overcome the parasitic capacitance of the sensor during use.
4.3 Grounding technology
Grounding technology is one of the effective technologies for suppressing interference and an important guarantee for shielding technology. Correct grounding can effectively suppress external interference, and at the same time improve the reliability of the test system and reduce the interference factors generated by the system itself. There are two purposes of grounding: safety and interference suppression. Therefore, grounding is divided into protective grounding, shielding grounding and signal grounding. Protective grounding is for the purpose of safety. The housing and chassis of the sensor measuring device must be grounded. The grounding resistance is required to be below 10 Ω; shielding grounding is a low-resistance path formed by the interference voltage to the ground to prevent interference with the measuring device. The grounding resistance should be less than 0.02Ω; the signal ground is the common line of the zero signal potential of the input and output of the electronic device, which itself may be insulated from the earth. The signal ground is divided into analog signal ground and digital signal ground. The analog signal is generally weak, so the ground requirement is higher; the digital signal is generally strong, so the ground requirement can be lower.
Different sensor detection conditions also have different requirements for grounding methods. It is necessary to choose a suitable grounding method. Common grounding methods include one-point grounding and multi-point grounding.
4.3.1 One-point grounding
In low-frequency circuits, it is generally recommended to use one-point grounding, which has radial grounding wires and busbar grounding lines. Radial grounding means that each functional circuit in the circuit is directly connected to the zero potential reference point with a wire; busbar grounding means that a high-quality conductor with a certain cross-sectional area is used as a grounding busbar, which is directly connected to the zero potential point, and the ground of each functional block in the circuit can be connected to the busbar nearby. If multi-point grounding is used at this time, multiple grounding loops will be formed in the circuit. When low-frequency signals or pulse magnetic fields pass through these loops, electromagnetic induction noise will be caused. Due to the different characteristics of each grounding loop, potential differences will be generated at different loop closing points, forming interference. To avoid this situation, it is best to use a single-point grounding method.
The sensor and the measuring device constitute a complete detection system, but the two may be far apart. Since the earth current in the industrial field is very complex, the potential between the grounding points of the two parts of the shell is generally different; if the zero potential of the sensor and the measuring device is grounded at two locations, that is, two-point grounding, a large current will flow through the signal transmission line with a very low internal resistance to generate a voltage drop, causing series mode interference. Therefore, a single-point grounding method should also be used in this case.
4.3.2 Multi-point grounding
It is generally recommended that high-frequency circuits use multi-point grounding. At high frequencies, even a small section of ground wire will have a large impedance voltage drop. In addition to the effect of distributed capacitance, it is impossible to achieve single-point grounding. Therefore, a planar grounding method, i.e., a multi-point grounding method, can be used. A good conductive plane (such as a layer in a multi-layer circuit board) is connected to the zero potential reference point, and the ground of each high-frequency circuit is connected to the conductive plane body nearby. Since the high-frequency impedance of the conductive plane body is very small, the potential consistency of each point is basically guaranteed. At the same time, bypass capacitors are added to reduce the voltage drop. Therefore, a multi-point grounding method should be used in this case.
4.4 Isolation technology
In the interface circuit, if there are more than two grounding points, common impedance coupling interference and ground loop current interference may be introduced. The method to suppress this type of interference is to use isolation technology. Usually there are two types: electromagnetic isolation and photoelectric isolation.
4.4.1 Electromagnetic coupling isolation
Use an isolation transformer to cut off the circulating current. Since the ground loop is cut off, the two circuits have independent ground potential references, so there will be no interference, and the signal is transmitted in a coupled form.
4.4.2 Photoelectric coupling isolation
The photoelectric coupler is an electric-optical-electric coupling device, which is composed of a light-emitting diode and a phototransistor package. Its input and output are electrically insulated. Therefore, in addition to being used for photoelectric control, this device is now increasingly used to improve the system's ability to resist common-mode interference. In this way, even if there is interference in the input circuit, as long as it is within the threshold, it will not affect the output.
4.5 Other anti-interference technologies
(1) Voltage stabilization technology. At present, there are two types of voltage stabilization power supplies commonly used in the development of intelligent sensors and instruments: one is a series adjustment power supply provided by an integrated voltage stabilization chip, and the other is a DC-DC voltage stabilization power supply, which is very effective in preventing grid voltage fluctuations from interfering with the normal operation of the instrument.
(2) Common-mode interference suppression technology. Using a differential amplifier, increasing the input impedance of the differential amplifier or reducing the internal resistance of the signal source can greatly reduce the impact of common-mode interference.
(3) Software compensation technology. External factors such as temperature and humidity changes can also cause changes in certain parameters, resulting in deviations. Software can be used to make corrections based on changes in external factors and error curves to remove interference.
5 Conclusion
Anti-interference is a very complex and practical problem. An interference phenomenon may be caused by several factors. Therefore, in the design of sensor circuits and measurement and control systems, not only should anti-interference measures be taken in advance, but also the encountered phenomena should be analyzed in time during the debugging process, and the circuit principles, specific wiring, shielding, anti-interference ability of power supply, digital or analog ground processing and protection forms of sensors and their systems should be continuously improved to improve the reliability and stability of the circuit.
Previous article:Application of Combination Compression in Storage Test System
Next article:Research on Unstructured Massive Network Data Processing Technology
Recommended ReadingLatest update time:2024-11-16 15:20
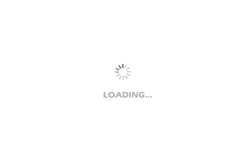
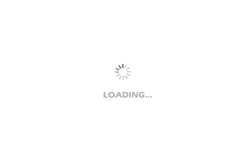
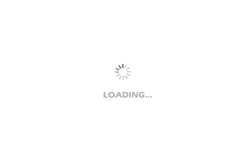
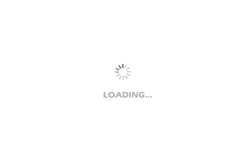
- Popular Resources
- Popular amplifiers
-
Analysis and Implementation of MAC Protocol for Wireless Sensor Networks (by Yang Zhijun, Xie Xianjie, and Ding Hongwei)
-
Introduction to Internet of Things Engineering 2nd Edition (Gongyi Wu)
-
西门子S7-12001500 PLC SCL语言编程从入门到精通 (北岛李工)
-
Modern Motor Control Technology (Wang Chengyuan, Xia Jiakuan, Sun Yibiao)
- Keysight Technologies Helps Samsung Electronics Successfully Validate FiRa® 2.0 Safe Distance Measurement Test Case
- From probes to power supplies, Tektronix is leading the way in comprehensive innovation in power electronics testing
- Seizing the Opportunities in the Chinese Application Market: NI's Challenges and Answers
- Tektronix Launches Breakthrough Power Measurement Tools to Accelerate Innovation as Global Electrification Accelerates
- Not all oscilloscopes are created equal: Why ADCs and low noise floor matter
- Enable TekHSI high-speed interface function to accelerate the remote transmission of waveform data
- How to measure the quality of soft start thyristor
- How to use a multimeter to judge whether a soft starter is good or bad
- What are the advantages and disadvantages of non-contact temperature sensors?
- Innolux's intelligent steer-by-wire solution makes cars smarter and safer
- 8051 MCU - Parity Check
- How to efficiently balance the sensitivity of tactile sensing interfaces
- What should I do if the servo motor shakes? What causes the servo motor to shake quickly?
- 【Brushless Motor】Analysis of three-phase BLDC motor and sharing of two popular development boards
- Midea Industrial Technology's subsidiaries Clou Electronics and Hekang New Energy jointly appeared at the Munich Battery Energy Storage Exhibition and Solar Energy Exhibition
- Guoxin Sichen | Application of ferroelectric memory PB85RS2MC in power battery management, with a capacity of 2M
- Analysis of common faults of frequency converter
- In a head-on competition with Qualcomm, what kind of cockpit products has Intel come up with?
- Dalian Rongke's all-vanadium liquid flow battery energy storage equipment industrialization project has entered the sprint stage before production
- Allegro MicroSystems Introduces Advanced Magnetic and Inductive Position Sensing Solutions at Electronica 2024
- Car key in the left hand, liveness detection radar in the right hand, UWB is imperative for cars!
- After a decade of rapid development, domestic CIS has entered the market
- Aegis Dagger Battery + Thor EM-i Super Hybrid, Geely New Energy has thrown out two "king bombs"
- A brief discussion on functional safety - fault, error, and failure
- In the smart car 2.0 cycle, these core industry chains are facing major opportunities!
- The United States and Japan are developing new batteries. CATL faces challenges? How should China's new energy battery industry respond?
- Murata launches high-precision 6-axis inertial sensor for automobiles
- Ford patents pre-charge alarm to help save costs and respond to emergencies
- New real-time microcontroller system from Texas Instruments enables smarter processing in automotive and industrial applications
- EEWORLD University ---- Amplifier Protection Series
- Introduction to calling DSP functions of TMS320F28335
- If the input signal travels 100 meters, is it better to connect it to the positive pole or the negative pole of the optocoupler?
- RCD calculation method (welcome to find faults. Many experts participated)
- Summary of programming development skills
- I don't know if this problem is negative optimization of AD.
- The BB_Black control panel of the Antminer
- MSP430 MCU Timer A Structure and Application Examples
- The development history of single-chip microcomputer and 51 series single-chip microcomputer
- A brief discussion on the 9 functions and 27 applications of capacitors in power supplies