This paper uses a computer as the main controller and adopts Windows-style interface software. It has fast calculation and testing speed, strong information processing ability, high system integration, friendly working interface, easy operation, realizes the automation of multi-parameter test process, and improves test efficiency and accuracy.
Main functions and features of the system
The system is mainly aimed at integrated testing of parameters that have a great impact on machine tool performance, and has the following functions and features:
(1) The system can measure the load of the reducer, and perform no-load test, load test, inertia load test, clutch on-off test, hysteresis test, etc. It can test the three axes of X, Y1 and Y2 at the same time;
(2) The system has online measurement for the automatic height adjustment system; the height adjustment precision function can test up to 8 heads at the same time, and the feed distance has automatic setting and user setting functions. The error value is calculated and displayed in real time as the head feeds;
(3) It has the functions of automatic test time setting, adding virtual load and load adjustment;
(4) The control system has a high temperature aging test function and automatically monitors and records the system status;
(5) Dynamic display of measurement data, if the data exceeds the standard, alarm will be given immediately or the experiment will be stopped;
(6) The test results are automatically analyzed and printed, and related file operations can be performed to facilitate in-depth analysis and statistics of the test results.
System hardware structure and composition
The system adopts a modular structure, with a computer as the main controller. The computer has rich software and hardware resources and powerful system functions, high computing and control speed, and good control performance in field control. The other parts of the system are connected to the computer through an interface card, controlled by it and providing test data for it. By executing the interface software on the computer, the hardware structure block diagram of the system is shown in Figure 1. It mainly consists of the following parts:
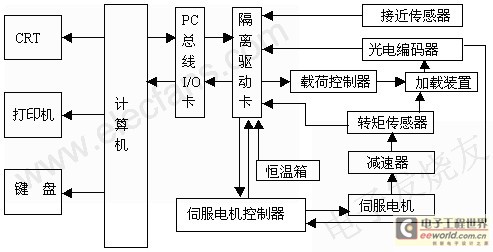
Figure 1 System structure diagram
Main Controller
The main controller of the system consists of an industrial computer, a standard keyboard, a mouse, a CRT color display and a printer. As the main controller of the system, the computer controls the actions of other parts through the interface card, collects test data, and performs complex calculations and analyses on these data to complete various test functions integrated by the system. At the same time, during the test process, the test results are displayed in real time and dynamically. If it is found that the standard is exceeded, an alarm will be issued and the fault time will be automatically recorded so that the operator can take relevant measures. The operator can perform human-machine operations through the display, keyboard and mouse, select the corresponding test items, enter the necessary test parameters, monitor the entire test process, perform corresponding file operations, and print the test results through the printer.
Interface modules
The interface module mainly includes the isolation driver card and the input/output interface card. The input/output interface card is responsible for the computer control of the test device and data acquisition, and is divided into a digital signal interface and an analog signal interface. The analog input (AI) uses Advantech PCI-726, the analog output (AO) uses Advantech PCI-1710, and the isolation driver card digital input (DI) and digital output (DO) use Advantech PCI-734. The specific number of channels is determined as follows:
Digital Input (DI):
Torque sensor 3-way
Code disk 18 way
Fault alarm 3 channels
Analog Input (AI):
Proximity sensor 8-way
Digital output (DO):
Clutch 3-way
Pulse inhibit 3-way
SV-ON 3-way
Pulse train 3 channels
Symbol 3 way
C-MODE 3-way
Analog Output (AO):
Servo command: 3 channels[page]
Loading control: 3-way
Total DI: 24 channels, AI: 8 channels, DO: 18 channels, AO: 6 channels.
The input and output interface cards used in this system are all PCI buses. Due to the large amount of testing and control, three interface cards are used. Through hardware adjustment, the base addresses are set to 300H and 330H respectively. The analog signal input and output channels are independent of each other, with a resolution of 12 bits, and the signal range is as follows:
Input range: -10V~+10V
Output range: -10V~+10V
The digital input and output signals of the interface card are compatible with TTL level and are easy to connect with other parts. The characteristics are as follows:
Input low level VIL≤0.8V
Input high level VIH ≥ 2.0V
Output low level VOL≤0.5V
Output high level VOH ≥ 2.4V
In order to ensure the safety of system operation, the system also uses an isolation driver card to ensure the isolation of computer signals and external signals through means such as photoelectric isolation, and amplify the output signal of the interface card into the required intensity control signal of the servo drive and clutch.
Motion Control Module
It mainly includes servo system and loading system. The servo system consists of servo motor driver, servo motor and photoelectric encoder. Its main function is to control the reducer under test to operate according to a motion law during the test. In this system, 3 sets of Panasonic (MINAS) servo systems are used to control the X, Y1 and Y2 axes respectively. The system has three control modes: speed control, position control and torque control, which can meet various motion control requirements during the test. Before use, parameter settings are required. The relevant parameter settings are as follows:
No.25=10000, No.26=7200
NO.27=1, NO.29=3
The servo drive is controlled by the computer interface card. When the servo command output of the interface card is +3V, the servo motor speed is 1500 rpm. The computer also controls the sign bit, output prohibition, SV-ON bit and C-MODE bit of the servo drive through the interface card. When the sign is 1, it corresponds to the CCW direction (forward rotation), when the pulse output is 1, prohibition is effective, SV-ON low level is effective, C-MODE low level is speed control mode, and high level is position control mode. During the test, according to different test items, the computer changes these control signals according to the program to make the servo motor work in different modes and states.
The loading system is mainly responsible for providing a virtual load to the shaft end. The loading controller receives the analog signal output by the computer and adjusts the current flowing through the loading device according to this signal, thereby controlling the torque at the shaft end.
Sensor Module
The proximity sensor uses the WYD series DC displacement sensor with a range of 20mm and an output voltage of 0~5V. The sensor is integrated with the electronic circuit, easy to install and use, does not require an external amplifier, and can be directly connected to the computer input and output interface card for analog-to-digital conversion and data processing, and then provide the micro-variables of relative displacement to the computer. The system uses a total of 8 proximity sensors to test and adjust the accuracy.
The torque sensor uses JN338 torque sensor, which can realize non-contact transmission of energy and signals, and the transmission is independent of whether it rotates, the speed, and the direction of rotation. The output signal is a pulse signal.
As a speed and displacement sensor, the output of the incremental photoelectric encoder is provided to the servo system for motion control on the one hand, and to the computer for collection on the other hand. The computer converts and counts the encoder output signal through software. The product of the total count value and the pulse equivalent is the displacement, and the displacement in a short period of time is the instantaneous speed.
Interface software development
The main application program of the system interface software is developed under the Windows operating system using the visual program development tool Visual Basic 6.0. The software operation interface adopts the Windows style, and its block diagram is shown in Figure 2.
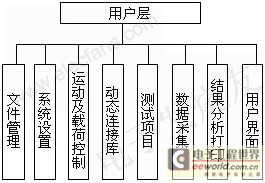
Figure 2 System software block diagram
Visual Basic 6.0 is a powerful high-level visual programming language for computers, but it cannot directly access the computer input and output interfaces. To solve this problem, the system uses C++ language to compile a dynamic link library (DLL). All the access functions to the hardware ports are implemented in the link library. When a port needs to be accessed, the corresponding link library function is called to perform dynamic connection. This not only realizes the predetermined functions, but also optimizes the software structure and saves a lot of system resources.
in conclusion
The machine tool testing system designed with this system runs smoothly, has a friendly interface, is easy to operate, has high control accuracy, and the positioning accuracy of the X-axis, Y1-axis, and Y2-axis all reaches 0.024mm, and the repeat positioning accuracy of the X-axis, Y1-axis, and Y2-axis all reaches 0.015mm.
Previous article:Automatic cutting, collecting and arranging system of microstructured optical fiber capillaries based on PLC
Next article:Application of new microcontroller in electricity theft prevention and metering
- Popular Resources
- Popular amplifiers
- Keysight Technologies Helps Samsung Electronics Successfully Validate FiRa® 2.0 Safe Distance Measurement Test Case
- From probes to power supplies, Tektronix is leading the way in comprehensive innovation in power electronics testing
- Seizing the Opportunities in the Chinese Application Market: NI's Challenges and Answers
- Tektronix Launches Breakthrough Power Measurement Tools to Accelerate Innovation as Global Electrification Accelerates
- Not all oscilloscopes are created equal: Why ADCs and low noise floor matter
- Enable TekHSI high-speed interface function to accelerate the remote transmission of waveform data
- How to measure the quality of soft start thyristor
- How to use a multimeter to judge whether a soft starter is good or bad
- What are the advantages and disadvantages of non-contact temperature sensors?
- Innolux's intelligent steer-by-wire solution makes cars smarter and safer
- 8051 MCU - Parity Check
- How to efficiently balance the sensitivity of tactile sensing interfaces
- What should I do if the servo motor shakes? What causes the servo motor to shake quickly?
- 【Brushless Motor】Analysis of three-phase BLDC motor and sharing of two popular development boards
- Midea Industrial Technology's subsidiaries Clou Electronics and Hekang New Energy jointly appeared at the Munich Battery Energy Storage Exhibition and Solar Energy Exhibition
- Guoxin Sichen | Application of ferroelectric memory PB85RS2MC in power battery management, with a capacity of 2M
- Analysis of common faults of frequency converter
- In a head-on competition with Qualcomm, what kind of cockpit products has Intel come up with?
- Dalian Rongke's all-vanadium liquid flow battery energy storage equipment industrialization project has entered the sprint stage before production
- Allegro MicroSystems Introduces Advanced Magnetic and Inductive Position Sensing Solutions at Electronica 2024
- Car key in the left hand, liveness detection radar in the right hand, UWB is imperative for cars!
- After a decade of rapid development, domestic CIS has entered the market
- Aegis Dagger Battery + Thor EM-i Super Hybrid, Geely New Energy has thrown out two "king bombs"
- A brief discussion on functional safety - fault, error, and failure
- In the smart car 2.0 cycle, these core industry chains are facing major opportunities!
- The United States and Japan are developing new batteries. CATL faces challenges? How should China's new energy battery industry respond?
- Murata launches high-precision 6-axis inertial sensor for automobiles
- Ford patents pre-charge alarm to help save costs and respond to emergencies
- New real-time microcontroller system from Texas Instruments enables smarter processing in automotive and industrial applications
- Purgatory Legend-FIFO Battle
- Want to solve the overheating and board separation uncertainty problems of LED driver chips?
- X-NUCLEO-IKS01A3 sensor test based on STM32F401RE development board 7 LSM6DSO click test
- ESD electrostatic protection issues
- Design of intelligent control system for traffic lights
- Download and run the program via DAP
- Share the installation tips of proteus8.7 to simulate stm32
- I just started learning, so I would like to ask you, what kind of circuit is this and what is its function?
- Hearing is believing, seeing is believing! Acoustic black technology is here!
- Shenzhen recruitment: Embedded software engineer (power supply direction), listed company background