Home >
Power Circuits >Electronic Ballast > Analysis on failure mechanism of energy-saving lamp power tube
Analysis on failure mechanism of energy-saving lamp power tube
Source: InternetPublisher:通通 Updated: 2016/03/28
1 Introduction As an environmentally friendly power source, energy-saving lamps have been widely used around the world, and the domestic production of energy-saving lamps is particularly outstanding. As an important component of energy-saving lamps (including electronic ballasts), the quality of high-power switching transistors plays a key role in the quality and life of energy-saving lamps. At present, except for several imported brands such as Fairchild and ST, the quality of domestic energy-saving lamp power tubes on the market is not stable enough. This article analyzes the failure mechanism of high-power switching transistors in energy-saving lamp applications, and discusses the factors affecting failure. 2 Failure mode The main reason why energy-saving lamps are damaged and have short lifespan is the failure of high-power switching transistors. Through anatomical analysis of failed power tubes, it was found that the vast majority of failed power tubes were caused by emitter junction burnout and short circuit. When observing the dissected failed tube with a microscope, you can see obvious burnt black spots near the welding position in the launch area (see Figure 1). This is a typical burning phenomenon.
When the transistor is working, it will consume a certain amount of power due to the thermal effect of the current, which is dissipated power. The dissipated power mainly consists of the collector dissipated power: PT≈VceIc, that is, PT≈PCM. We know that the operating current of the triode is greatly affected by temperature. The relationship between the forward current of the PN junction and the temperature is: I∝e-(Eg-qV)/kT When the transistor is working, the dissipated power is converted into heat, which increases the collector junction temperature and further increases the collector junction current. Increasing it will cause a vicious cycle and cause the pipe to burn out. This situation is called thermal breakdown. The maximum operating temperature that prevents thermal breakdown of the tube is defined as the maximum junction temperature. The maximum junction temperature of the silicon material PN junction is: Tjm=6400/(10.45+lnρ) In another case, when the tube does not reach the maximum junction temperature, or does not exceed the maximum power dissipation, due to material defects and process unevenness properties, as well as the current tightening effect in the emitter area caused by structural reasons, make the operating current distribution of the triode uneven. When the current distribution is concentrated at a certain point, the power consumption at that point increases, causing the local temperature to increase. The increase in temperature, in turn, further increases the current there, thus forming a "hot spot". If its temperature exceeds that of the metal electrode and The eutectic point of semiconductors causes the triode to burn out. On the other hand, local temperature rise and high current density will cause local avalanche (breakdown). At this time, the local high current can cause the tube to burn through, causing the breakdown voltage to drop sharply, the current to rise, and finally causing the tube to burn out. This situation is called secondary breakdown. The characteristic curve of the secondary breakdown of the triode is shown in Figure 2.
Secondary breakdown is an important cause of power tube failure. In order to ensure the normal operation of the pipe, the concept of safe working area SOA is proposed. The SOA schematic diagram is shown in Figure 3. It consists of the collector maximum current Icm line, breakdown voltage BVceo line, collector maximum power dissipation Pcm line and secondary breakdown power consumption Psb line. Since the operating current and maximum voltage are designed not to exceed the rated value of the tube during use, under normal circumstances, the collector's power dissipation and secondary breakdown characteristics are the main factors causing tube failure and burnout.
3 Factors affecting failure From the above failure mechanism analysis, it can be seen that in order to reduce failure, it is important to reduce the power of the tube when working and improve the secondary breakdown characteristics. The two are actually related. It can be seen from the occurrence mechanism of secondary breakdown that the increase in temperature causes the HFE of the tube to increase, the switching performance becomes worse, and the secondary breakdown characteristics become worse (secondary breakdown is more likely to occur); the increase in temperature also causes the tube's The actual dissipated power parameters become worse and the safe working area of the tube becomes smaller. In turn, since the power dissipation of the tube is mainly related to the thermal resistance of the tube, low power dissipation actually means that the current and voltage it can withstand is low and the heat dissipation performance is poor, which also affects the secondary breakdown characteristics. Therefore, preventing the temperature of the tube from rising too high during operation and increasing the power dissipation of the tube are the most effective ways to improve the quality of the tube. 1) When the thermal resistance tube is working, when the PN junction temperature exceeds the maximum allowable junction temperature, the power consumed by the tube is the maximum power dissipated by the collector of the tube. Since the maximum junction temperature of a certain material is fixed, improving the heat dissipation performance of the tube means increasing the power dissipation of the tube. At the same time, good heat dissipation performance will lower the temperature rise of the tube, which also reduces the possibility of secondary breakdown. , which is an important factor in improving the secondary breakdown characteristics. As an important parameter of high-power tubes, thermal resistance represents the heat dissipation capacity of the tube. The relationship between thermal resistance and power dissipation is: Pcm=(Tjm-Ta)/RT where Tjm is the maximum junction temperature, Ta is the ambient temperature, and RT is the thermal resistance. It can be seen that when the maximum junction temperature is constant and the ambient temperature is constant, the amount of power dissipated depends on the size of the thermal resistance. In energy-saving lamp products, tubes with the lowest possible thermal resistance should be selected. In addition to the chip itself, the materials, processes and quality of post-process assembly have a great impact on thermal resistance. Testing and screening the tubes for thermal resistance is a basic requirement to ensure the quality of energy-saving lamp power tubes. 2) Switching parameters When a typical energy-saving lamp circuit is working, the two tubes work in saturation and cut-off states in turn, so the switching parameters of the tubes have a significant impact on their working conditions. There are four switching parameters of the tube: delay time td, rise time tr, storage time ts and fall time tf. As shown in the three-stage tube switching waveform shown in Figure 4, when the tube goes from cut-off to saturation, the transition time is affected by the delay time and rise time. When the tube goes from saturation to cut-off, the transition time is affected by the storage time and fall time. The power consumed by the tube in different working states is:
cut-off: P=Vce·Icex; saturation: P=Vces·Ic. Due to three reasons:
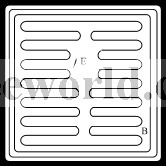
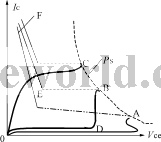
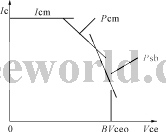
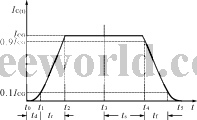
Latest Power Circuits Circuits
- Basic characteristics of power field effect tubes, how to improve the dynamic performance of power MOSFET
- 5 Converter Topologies for Integrated Solar and Storage Systems
- Step-down power supply for driving relays
- Visible laser digital control modulation driver
- A simple positive and negative power supply circuit
- Adjustable regulated power supply with current limiting protection
- Power supply circuit that can reduce LM317 ripple
- Reconstruction of the tube pre-stage by using low voltage difference power supply
- LM317T voltage regulation adjustable circuit diagram explanation
- How to Select Modular EMI Filters for AC-DC Converters
Popular Circuits
- DC 12V to AC 100V inverter power supply circuit design
- Power circuit a composed of intelligent thyristor modules
- EPSON PHOTO 830U printer power circuit
- 2-phase CPU power supply circuit using HIP6302 and HIP6602 chips
- KGDS type single-phase low temperature iron plated power supply circuit
- 500A-6V single-phase thyristor voltage regulating electroplating power supply circuit
- Simple dual-channel variable DC power supply circuit
- Timing switch AC power circuit
- Low voltage adjustable reference power circuit
- Household emergency power circuit 02