The three-phase asynchronous motor is a common type of motor, widely used in industrial production and daily life. In practical applications, the starting method of the three-phase asynchronous motor has an important impact on its performance and life. This article will introduce the starting method of the three-phase asynchronous motor in detail, especially the scope and limitations of direct starting.
-
The basic principle of three-phase asynchronous motor
The three-phase asynchronous motor is an electric motor that works on the principle of electromagnetic induction. It consists of two parts: the stator and the rotor. The stator is the fixed part of the motor, usually composed of three-phase windings. The rotor is the rotating part of the motor, usually composed of a squirrel cage or wound structure. When three-phase alternating current passes through the stator winding, a rotating magnetic field is generated in the stator. This rotating magnetic field cuts the rotor conductor, thereby generating an induced current in the rotor. The induced current interacts with the rotating magnetic field to generate an electromagnetic force, which causes the rotor to rotate.
-
Starting method of three-phase asynchronous motor
There are mainly the following starting methods for three-phase asynchronous motors:
(1) Direct starting: Direct starting means connecting the motor directly to the power supply so that it is subjected to the rated voltage during starting. Direct starting has the advantages of simple starting and low cost, but the starting current is large, which has a certain impact on the power grid and the motor itself.
(2) Star-delta starting: Star-delta starting is a commonly used starting method suitable for motors with higher power. During starting, the three-phase windings of the motor are connected in a star shape to reduce the starting current. After starting, the motor is switched to a delta connection to provide the rated voltage and rated power.
(3) Autotransformer starting: Autotransformer starting uses an autotransformer to reduce the starting voltage of the motor, thereby reducing the starting current. After starting, the autotransformer is removed to allow the motor to run at rated voltage.
(4) Soft starter start: A soft starter is an electronic control device that can gradually increase the voltage during the motor start-up process to achieve smooth start-up. Soft starters have the advantages of smooth start-up and little impact on the power grid, but they are relatively expensive.
-
Application scope of direct starting of three-phase asynchronous motor
Direct starting is suitable for small three-phase asynchronous motors, generally with a power of less than 7.5 kilowatts. This is because when starting directly, the starting current of the motor is large, which has a certain impact on the power grid and the motor itself. For large motors, direct starting may cause problems such as grid voltage drop and motor overheating.
-
Limitations of direct starting of three-phase asynchronous motors
(1) Large starting current: When starting directly, the starting current of the motor is about 5-7 times the rated current. This will cause the grid voltage to drop and affect the normal operation of other equipment.
(2) Small starting torque: When starting directly, the starting torque of the motor is small, about 1.5-2 times the rated torque. This may cause the motor to fail to start or start with difficulty.
(3) Impact on the motor itself: During direct starting, the motor is subjected to a large starting current and torque, which may cause problems such as motor overheating and insulation damage, thus affecting the life of the motor.
-
Selection of starting methods for three-phase asynchronous motors
When choosing the starting method for a three-phase asynchronous motor, it is necessary to comprehensively consider factors such as the motor's power, starting torque, and grid conditions. For small motors, direct starting is possible; for large motors, star-delta starting, autotransformer starting, or soft starter starting is recommended.
-
in conclusion
The starting method of a three-phase asynchronous motor has an important impact on its performance and life. Direct starting is suitable for motors with lower power, but there are problems such as large starting current and small starting torque. When choosing a starting method, it is necessary to make comprehensive considerations based on the actual situation of the motor. By reasonably choosing a starting method, the operating efficiency and life of a three-phase asynchronous motor can be improved.
Previous article:What are the electrical braking methods for three-phase asynchronous motors?
Next article:What current flows through the field winding of a synchronous generator?
Recommended ReadingLatest update time:2024-11-18 11:50
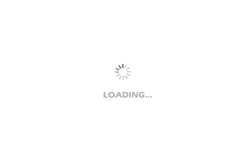
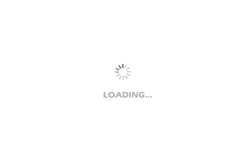
- Popular Resources
- Popular amplifiers
- A comprehensive analysis of electric vehicle charging infrastructure
- Automotive Imaging Radar Waveform Selection
- Regulations and standards for automotive millimeter wave radar (IV)
- An article explains the inner workings of automobile electric motors
- 5G helps turn self-driving cars into mobile data centers
- The psychology behind automotive LED lights
- How much benefit will adding a 48V system on top of a 12V system bring?
- How does SiC optimize the energy efficiency and performance of hybrid and electric vehicles compared to IGBT?
- The difference between new energy vehicle chargers and home charging piles
Professor at Beihang University, dedicated to promoting microcontrollers and embedded systems for over 20 years.
- Intel promotes AI with multi-dimensional efforts in technology, application, and ecology
- ChinaJoy Qualcomm Snapdragon Theme Pavilion takes you to experience the new changes in digital entertainment in the 5G era
- Infineon's latest generation IGBT technology platform enables precise control of speed and position
- Two test methods for LED lighting life
- Don't Let Lightning Induced Surges Scare You
- Application of brushless motor controller ML4425/4426
- Easy identification of LED power supply quality
- World's first integrated photovoltaic solar system completed in Israel
- Sliding window mean filter for avr microcontroller AD conversion
- What does call mean in the detailed explanation of ABB robot programming instructions?
- NXP FXLS8971CF and FXLS8961AF accelerometers improve your precision inclinometer application performance
- NXP FXLS8971CF and FXLS8961AF accelerometers improve your precision inclinometer application performance
- Industry Summit 2024 to stimulate innovation and promote the development of smart energy technologies
- Industry Summit 2024 to stimulate innovation and promote the development of smart energy technologies
- 2.1 uboot transplantation in linux
- uboot relocation code analysis
- ECS operating system: hardware platform porting and driver programming
- "Writing Embedded Operating Systems Step by Step" Reading Notes 1—Skyeye Introduction, Installation and HelloWorld
- The relationship between BootLoader and kernel image
- How to use UBOOT's own loadb command to load the application program into SDRAM for execution
- Detailed explanation of CAN bus
- Can you paint three-layer boards?
- AT32F421 Review
- AD20 schematic diagram and PCB Cross select layout have problems
- TF288_SPCE_Built-in driver chip HT1621 segment code LCD screen driver data
- Crystal oscillators determine the life and death of digital circuits
- Showing off the goods (2) - Intel, the king of pitfalls
- Software simulation of asynchronous communication of BF561 SPORT port
- About the strategy design of watchdog under multi-tasking
- Read the good book "Electronic Engineer Self-study Handbook" - a preliminary exploration of the content