AC motor is a machine used to realize the mutual conversion between mechanical energy and AC electrical energy. Due to the tremendous development of AC power system, AC motor has become the most commonly used motor.
Since AC motors do not have commutators, they are simple in structure, easy to manufacture, relatively strong, and easy to make into high-speed, high-voltage, high-current, and large-capacity motors. The power of AC motors covers a wide range, from a few watts to hundreds of thousands of kilowatts, or even millions of kilowatts.
AC motor speed regulation
With the development of power electronics technology, microelectronics technology, digital control technology and control theory, the dynamic and static characteristics of AC drive systems are completely comparable to those of DC drive systems. AC drive systems have been widely used, and it has gradually become a reality for AC drive to replace DC drive.
Since AC motors are essentially nonlinear, multivariable, strongly coupled, time-varying parameters, and highly disturbed complex objects, their effective control has always been a hot topic of research at home and abroad, and a variety of control strategies and methods have been proposed. Among them, classical linear control cannot overcome the large-scale changes in load and model parameters and the influence of nonlinear factors, and the control performance is not high; vector control and direct torque control also have some problems: In recent years, with the theoretical development of modern control and intelligent control, advanced control algorithms have been applied to AC motor control and have achieved certain results.
(1) Constant voltage-frequency ratio control
This method is an open-loop control method without speed feedback, which is based on the basic control method of variable voltage and variable frequency. If the voltage is constant and only the frequency is reduced below the rated frequency, the air gap flux will be too large, causing magnetic circuit saturation, and in serious cases, burning the motor. In order to keep the air gap flux unchanged, the ratio of induced potential to frequency is controlled as a constant.
The advantages of this method are: simple structure, reliable operation, and low control operation speed requirements.
Disadvantages of this method: The speed regulation accuracy and dynamic performance of open-loop control are poor; it only controls the air gap flux, but cannot adjust the torque, and the performance is not high; since it does not contain current control, a given integral link must be provided during starting to suppress current shock; the torque is insufficient at low frequency, and torque compensation is required to change the low-frequency torque characteristics.
(2) Closed-loop slip frequency control
This method is a direct torque control method. When the motor is running stably, within a small range of slip rate, as long as the motor flux remains unchanged, the motor torque is approximately proportional to the slip angular frequency. Therefore, controlling the slip angular frequency can control the motor torque.
The advantages of this method are: it basically controls the motor torque and improves the dynamic performance and steady-state accuracy of speed regulation.
Disadvantages of this method: It cannot truly control the torque of the dynamic process and the dynamic performance is not ideal.
AC motor speed regulation method
1. Listen to the sound and carefully find the fault point. When the AC asynchronous motor is running, if a thin "buzzing" sound is found, without changes in high and low, it is a normal sound. If the sound is rough and there is a sharp "buzzing" or "hissing" sound, it is a precursor to a fault. The following reasons should be considered:
(l) The vibration of the motor during operation and the sudden temperature changes will cause the core fixing bolts to deform, causing the silicon steel sheets to loosen and generate large electromagnetic noise.
(2) Rotor noise: The sound of the rotating rotor is produced by the cooling fan, which is a "humming" sound. If there is a "dong dong" sound like beating a drum, it is caused by the acceleration torque of the motor causing the rotor core and the shaft to loosen when the motor suddenly starts, stops, reverses, or changes speed. If the noise is minor, it can continue to be used. If the noise is serious, it should be disassembled for inspection and repair.
(3) Bearing noise When the motor is running, you must pay attention to the changes in the bearing sound. Touch one end of the screwdriver to the bearing cover and put the other end to your ear. You can hear the changes in the sound inside the motor. Different parts and different faults will have different sounds. For example, the "creaking" sound is caused by the irregular movement of the rollers in the bearing, which is related to the clearance and grease state of the bearing. The "hissing" sound is the metal friction sound, which is generally caused by the lack of oil in the bearing and the grinding. The bearing should be disassembled and greased.
2. Use your sense of smell to analyze the fault. The motor has no peculiar smell during normal operation. If you smell something strange, it is a fault signal. For example, a burnt smell is caused by the burning of insulation, and as the temperature of the motor rises, it will even smoke in severe cases. If it smells like burnt oil, it is mostly caused by the lack of oil in the bearing. When it is close to the dry grinding state, the peculiar smell of oil and gas evaporation occurs.
3. Use your hand to check for faults. Touch the TV casing with your hand to roughly determine the temperature. If the motor casing feels very hot when you touch it, the temperature is very high. You should check the cause, such as excessive load, excessive voltage, etc., and then troubleshoot the cause.
What are the three methods of AC motor speed regulation?
1. The purpose of speed regulation by changing the number of magnetic poles is to control the synchronous speed of the magnetic field to control the rotor speed. The slip rate remains unchanged, the slip loss is small, it is a step-by-step speed regulation, and its application occasions are limited.
2. Change the slip rate to adjust the speed, and change the rotor differential excitation current while keeping the synchronous speed unchanged. Disadvantages: The slip power of the motor cannot be utilized, its power factor is low, and all the slip power is consumed in the form of heat energy.
3. When changing the frequency speed regulation, the slip rate and slip power consumption remain unchanged.
From the perspective of energy consumption conversion of the above three speed regulation methods, the speed regulation efficiency of changing frequency is the highest. Because the power and efficiency of variable frequency speed regulation are high, the speed regulation accuracy is also quite high. It also has very hard mechanical characteristics and a wide speed regulation range, which makes it easy to achieve closed-loop automatic control. It is also the most energy-saving speed regulation method for AC motor speed regulation. It represents the current level of AC transmission speed control and is also the main reason for the increasing use of frequency converters.
(1) Pole-changing speed regulation: This speed-changing method is only applicable to specially produced pole-changing multi-speed asynchronous motors. Through different winding connection methods, three speeds of 2, 3, and 4 poles are obtained. Only a relatively large range of speed regulation can be achieved.
(2) Rotor series resistance: only suitable for wound rotor asynchronous motors, changing the resistance value of the resistor in series with the rotor circuit to change the slip rate to achieve speed regulation. It can achieve a variety of speed regulation. However, the resistor consumes power, has low efficiency, and weakens the mechanical properties, so it is only suitable for occasions where the speed regulation requirements are not high.
(3) Cascade speed regulation: only suitable for wound-rotor asynchronous motors, it feeds back the slip power to the power grid through certain electronic devices. It is widely used in transmission systems such as wind pumps.
(4) Super synchronous cascade speed regulation: Connect to the AC-AC inverter and control the working state of the inverter, so that the motor can be adjusted up and down at the synchronous speed. The speed regulation range is large and can generate braking torque.
(5) Voltage regulation and speed control: Use thyristors to form an AC speed control circuit, change the trigger angle, and change the terminal voltage of the asynchronous motor to adjust the speed. The efficiency is low and it is only suitable for motors with special rotors;
AC motor speed regulation method
1. Pole-changing speed regulation method
The speed can be adjusted by changing the connection method of the stator winding to change the number of stator poles of the cage motor.
2. Frequency conversion speed regulation method
A speed regulation method that uses a frequency converter to change the frequency of the motor's stator power supply, thereby changing its synchronous speed.
3. Cascade speed regulation method
Cascade speed regulation refers to inserting an adjustable additional potential in series into the rotor circuit of a wound-rotor motor to change the motor's slip and achieve the purpose of speed regulation. Most of the slip power is absorbed by the additional potential inserted in series, and then the absorbed slip power is returned to the power grid or converted into energy for utilization by generating additional devices. According to the way of absorbing and utilizing the slip power, cascade speed regulation can be divided into motor cascade speed regulation, mechanical cascade speed regulation and thyristor cascade speed regulation, and thyristor cascade speed regulation is mostly used.
Previous article:The difference between AC induction motor and permanent magnet synchronous motor
Next article:What are the advantages and disadvantages of brushless motors, their functions and lifespan?
Recommended ReadingLatest update time:2024-11-16 09:46
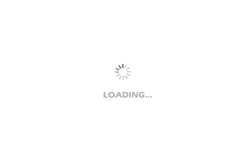
- Popular Resources
- Popular amplifiers
- Huawei's Strategic Department Director Gai Gang: The cumulative installed base of open source Euler operating system exceeds 10 million sets
- Analysis of the application of several common contact parts in high-voltage connectors of new energy vehicles
- Wiring harness durability test and contact voltage drop test method
- Sn-doped CuO nanostructure-based ethanol gas sensor for real-time drunk driving detection in vehicles
- Design considerations for automotive battery wiring harness
- Do you know all the various motors commonly used in automotive electronics?
- What are the functions of the Internet of Vehicles? What are the uses and benefits of the Internet of Vehicles?
- Power Inverter - A critical safety system for electric vehicles
- Analysis of the information security mechanism of AUTOSAR, the automotive embedded software framework
Professor at Beihang University, dedicated to promoting microcontrollers and embedded systems for over 20 years.
- Innolux's intelligent steer-by-wire solution makes cars smarter and safer
- 8051 MCU - Parity Check
- How to efficiently balance the sensitivity of tactile sensing interfaces
- What should I do if the servo motor shakes? What causes the servo motor to shake quickly?
- 【Brushless Motor】Analysis of three-phase BLDC motor and sharing of two popular development boards
- Midea Industrial Technology's subsidiaries Clou Electronics and Hekang New Energy jointly appeared at the Munich Battery Energy Storage Exhibition and Solar Energy Exhibition
- Guoxin Sichen | Application of ferroelectric memory PB85RS2MC in power battery management, with a capacity of 2M
- Analysis of common faults of frequency converter
- In a head-on competition with Qualcomm, what kind of cockpit products has Intel come up with?
- Dalian Rongke's all-vanadium liquid flow battery energy storage equipment industrialization project has entered the sprint stage before production
- Allegro MicroSystems Introduces Advanced Magnetic and Inductive Position Sensing Solutions at Electronica 2024
- Car key in the left hand, liveness detection radar in the right hand, UWB is imperative for cars!
- After a decade of rapid development, domestic CIS has entered the market
- Aegis Dagger Battery + Thor EM-i Super Hybrid, Geely New Energy has thrown out two "king bombs"
- A brief discussion on functional safety - fault, error, and failure
- In the smart car 2.0 cycle, these core industry chains are facing major opportunities!
- The United States and Japan are developing new batteries. CATL faces challenges? How should China's new energy battery industry respond?
- Murata launches high-precision 6-axis inertial sensor for automobiles
- Ford patents pre-charge alarm to help save costs and respond to emergencies
- New real-time microcontroller system from Texas Instruments enables smarter processing in automotive and industrial applications
- Pingtouge RVB2601 board-GUI and operating system tasks
- MSP430G2553ADC conversion program
- How to choose the right fuse for your design
- Build an IP surveillance camera system using low-cost FPGA
- Microwave Heating Principle
- 【Development Kit for nRF52840】+ Hardware Review
- [Repost] Comparison between aluminum electrolytic capacitors and tantalum capacitors
- Programming example: CPU card response data command
- How to use multiple devices to study radiation signals - Part 1
- Tianjin - Recruiting embedded software and hardware engineers - fresh graduates preferred