Under Matlab/Simulink, combined with Simulink basic modules and S-Function, a design scheme for brushless DC motor control system is proposed. The system adopts double closed-loop control: the speed loop adopts PI control, and the current loop is composed of current hysteresis comparator. The simulation results show that the brushless DC motor control system designed by this scheme has the advantages of fast and practical.
1. Introduction
Brushless DC Motor (BLDCM) is a new type of motor that has matured rapidly with the development of power electronics technology and new permanent magnet materials. It has the advantages of large starting torque, good speed regulation performance, high efficiency, strong overload capacity, stable performance, simple control structure, etc., while retaining the excellent mechanical properties of ordinary DC motors. It is widely used in servo control, CNC machine tools, robots and other fields.
With the continuous expansion of BLDCM application fields, higher requirements are put forward for control system design. Therefore, establishing a visual simulation model of the BLDCM control system can effectively reduce the design time of the control system, and at the same time make full use of the advantages of Simulink simulation, add different disturbances and changing parameters, so as to examine the dynamic and static characteristics of the system under different control conditions. Based on the analysis of the BLDCM mathematical model, with the help of MATLAB's Simulink tool, a simulation model of the BLDCM control system is established, and the control system simulation test is carried out using this model. The results show that the effectiveness of the mathematical model and the rationality of the control system are verified by this simulation model.
2. Overall design of numerous DC motors
BLDCM consists of three-phase stator winding, permanent magnet rotor, inverter, rotor magnetic pole position detector, etc. Its rotor adopts tile-shaped magnetic steel and special magnetic circuit design to obtain trapezoidal air gap magnetic field. The stator winding adopts concentrated full-pitch winding, which is provided with square wave current by inverter. The relationship between BLDCM trapezoidal wave back electromotive force and square wave current is shown in Figure 1.
The back electromotive force waveform of BLDCM is a trapezoidal wave, and the mutual inductance between the stator and the rotor is non-sinusoidal. Here, the analysis effect of the induction motor dq transformation theory is not ideal, and the original phase variable method of the motor is directly used. According to the rotor position, the induced electromotive force is expressed by piecewise linear. This paper analyzes the mathematical model and electromagnetic torque characteristics of BLDCM in the two-phase conduction star three-phase six-state mode. For the convenience of analysis, the following assumptions are made:
(1) The three-phase winding is completely symmetrical, the air gap magnetic field distribution is a trapezoidal wave, and the flat top width is 120° electrical angle;
(2) Ignore the effects of cogging, commutation process and armature reaction;
(3) The magnetic circuit is not saturated, and eddy current and hysteresis losses are not considered;
(4) The armature winding is evenly and continuously distributed on the inner surface of the stator.
According to the characteristics of BLDCM, its voltage balance equation, electromagnetic torque equation and rotor motion equation can be established.
2.1 Voltage balance equation
The balance equation of the three-phase stator voltage of BLDCM can be expressed by the following equation:
Among them, ua, ub, uc are the stator phase winding voltages; ia, ib, ic are the stator phase winding currents; ea, eb, ec are the stator phase winding back electromotive force; L is the self-inductance of each phase winding; r is the internal resistance of each phase winding; M is the mutual inductance of each two phase winding. Since the rotor magnetic resistance does not change with the position of the rotor, the self-inductance and mutual inductance of the stator winding are constants. When Y-shaped connection is adopted, ia+ib+ic=0, so:
3. Brushless DC motor model design
In the Simulink environment of Matlab R2012, using the rich module library of SimPowerSystem Toolbox 5.6, on the basis of analyzing the mathematical model of BLDCM, a simulation model of BLDCM control system is established. The system design block diagram is shown in Figure 2.
As shown in Figure 2, the BLDCM control system adopts dual closed-loop control: the speed loop adopts PI control, and the current loop adopts current hysteresis comparator. The control system shown in Figure 2 is divided into independent sub-modules, which mainly include: BLDCM body module, reference current module, current hysteresis control module, voltage inverter module, speed control module, torque calculation module. By organically integrating each module, the simulation model of the BLDCM control system can be established, as shown in Figure 3.
3.1 BLDCM main module
In the entire control system, the BLDCM main module is the most important part. This module obtains the BLDCM three-phase current according to the BLDCM voltage balance equation (2). The control block diagram is shown in Figure 4. From the voltage balance equation (2), it can be obtained that to obtain the three-phase currents ia, ib, and ic, it is necessary to first obtain the three-phase back electromotive force ea, eb, and ec. In the BLDCM modeling process, obtaining the ideal trapezoidal back electromotive force waveform is a key issue. At present, the commonly used methods for obtaining back electromotive force are: (1) finite element method; (2) Fourier transform method; (3) piecewise linear method. As shown in Figure 5, a running cycle is divided into 6 stages, and each 60° is a phase change stage. Each running stage of each phase can be represented by a straight line. According to the rotor position and speed signal at a certain moment, the running state of each phase at that moment is determined, and the back electromotive force waveform can be obtained by the straight line equation. The piecewise linear method is simple and easy to use, and has high accuracy, which can better meet the design requirements of simulation modeling. Therefore, the piecewise linear method is used to establish the trapezoidal back electromotive force waveform.
According to FIG5 , the linear relationship between the rotor position and the back electromotive force can be deduced, as shown in Table 1. Thus, the problem of obtaining the trapezoidal wave back electromotive force in the BLDCM main module is solved by using the piecewise linear method.
3.2 Current hysteresis control module
The function of the current hysteresis control module is to realize hysteresis current control. It inputs three-phase reference current and three-phase actual current, and outputs inverter control signal. The module structure block diagram is shown in Figure 6. The deviation between the actual current and the reference current is compared with the loop width of the hysteresis comparator, and the corresponding phase is turned on or off. By selecting the appropriate loop width of the hysteresis comparator, the actual current waveform can continuously track the waveform of the reference current to realize current closed-loop control.
k is the coefficient, Pos is the position signal, and w is the speed signal. 3.3 Speed Control Module
The speed control module has a single input: the difference between the reference speed and the actual speed; and a single output: the amplitude Is of the three-phase reference current. KP is the proportional parameter, KI is the integral parameter, and the Saturation limiting module limits the amplitudes of the three reference currents output within the required range, as shown in Figure 7.
3.4 Reference Current Module
The function of the reference current module is to give a three-phase reference current according to the current amplitude signal Is and the position signal. The output three-phase reference current is directly input into the current hysteresis control module for current hysteresis control with the actual current. The reference current module is implemented by S-Function programming.
3.5 Voltage Inverter Module
The voltage inverter module realizes the function of the inverter. The input is the position signal and the current hysteresis control module gives the inverter control signal. The output is the three-phase terminal voltage.
This module can determine the operating stage of the motor based on the position signal and give the corresponding three-phase terminal voltage signal. This module is implemented using S-Function programming.
4. Simulation Results
This paper establishes a simulation model of the BLDCM control system based on Matlab/Simulink, and simulates the BLDCM double closed-loop control system on the model. In the simulation, the BLDCM parameters are set as follows: stator phase winding resistance R=1Ω, stator phase winding self-inductance L=0.02H, mutual inductance M=-0.0061H, moment of inertia J=0.005kg.m2, rated speed n=2400r/min, pole pair number p=1, and rated voltage 220V. In order to verify the static and dynamic performance of the designed BLDCM control system simulation model, the system is started at no-load, and after entering the steady state, a load TL=5Nm is suddenly added at t=0.5s, and the load is removed at t=0.65s. The simulation curves of system speed, torque, three-phase current and three-phase back EMF are shown in Figures 8-11.
It can be seen from the simulation waveform that at the reference speed of n=2400r/min, the system responds quickly and smoothly, and the phase current and back electromotive force waveforms are ideal. Figures 9 and 10 show that: during the starting stage, the system maintains a constant torque and does not cause a large torque and phase current impact, indicating that the limiting effect of the reference current is effective; when running at a steady speed without load, the friction torque of the system is ignored, and the mean value of the electromagnetic torque at this time is zero; when the load is suddenly added at t=0.5s, the speed drops suddenly, but it can quickly return to a balanced state, and there is no static error during steady-state operation. The simulation results show that the design scheme of the brushless DC motor control system proposed in this paper is effective and the control system is reasonable.
Previous article:How to distinguish between brushless motors and servo motors
Next article:What are the characteristics of a servo encoder? How to connect it?
Recommended ReadingLatest update time:2024-11-16 11:40
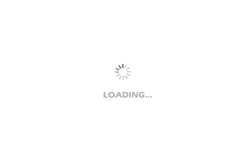
- Huawei's Strategic Department Director Gai Gang: The cumulative installed base of open source Euler operating system exceeds 10 million sets
- Analysis of the application of several common contact parts in high-voltage connectors of new energy vehicles
- Wiring harness durability test and contact voltage drop test method
- Sn-doped CuO nanostructure-based ethanol gas sensor for real-time drunk driving detection in vehicles
- Design considerations for automotive battery wiring harness
- Do you know all the various motors commonly used in automotive electronics?
- What are the functions of the Internet of Vehicles? What are the uses and benefits of the Internet of Vehicles?
- Power Inverter - A critical safety system for electric vehicles
- Analysis of the information security mechanism of AUTOSAR, the automotive embedded software framework
Professor at Beihang University, dedicated to promoting microcontrollers and embedded systems for over 20 years.
- Innolux's intelligent steer-by-wire solution makes cars smarter and safer
- 8051 MCU - Parity Check
- How to efficiently balance the sensitivity of tactile sensing interfaces
- What should I do if the servo motor shakes? What causes the servo motor to shake quickly?
- 【Brushless Motor】Analysis of three-phase BLDC motor and sharing of two popular development boards
- Midea Industrial Technology's subsidiaries Clou Electronics and Hekang New Energy jointly appeared at the Munich Battery Energy Storage Exhibition and Solar Energy Exhibition
- Guoxin Sichen | Application of ferroelectric memory PB85RS2MC in power battery management, with a capacity of 2M
- Analysis of common faults of frequency converter
- In a head-on competition with Qualcomm, what kind of cockpit products has Intel come up with?
- Dalian Rongke's all-vanadium liquid flow battery energy storage equipment industrialization project has entered the sprint stage before production
- Allegro MicroSystems Introduces Advanced Magnetic and Inductive Position Sensing Solutions at Electronica 2024
- Car key in the left hand, liveness detection radar in the right hand, UWB is imperative for cars!
- After a decade of rapid development, domestic CIS has entered the market
- Aegis Dagger Battery + Thor EM-i Super Hybrid, Geely New Energy has thrown out two "king bombs"
- A brief discussion on functional safety - fault, error, and failure
- In the smart car 2.0 cycle, these core industry chains are facing major opportunities!
- The United States and Japan are developing new batteries. CATL faces challenges? How should China's new energy battery industry respond?
- Murata launches high-precision 6-axis inertial sensor for automobiles
- Ford patents pre-charge alarm to help save costs and respond to emergencies
- New real-time microcontroller system from Texas Instruments enables smarter processing in automotive and industrial applications
- How to set AD copper plating to only fully plating the via GND, while the GND of the straight plug-in is still a cross connection
- [Silicon Labs BG22-EK4108A Bluetooth Development Evaluation] + LED Flashing
- 【ART-Pi Review】V. Getting Weather Data Online
- 【IoT Graduation Project. Part 1】STM32+Gizwits AIoT+Laboratory Safety Monitoring System
- SparkRoad realizes personal camera
- How to detect transformer?
- [Image recognition classification & motion detection & analog signal processing system based on Raspberry Pi 400, Part 4] Try to make an MP3 player...
- Wiring harness insulation resistance test, which method would you choose?
- The continuous operation mode CCM and the interruption mode DCM of the inductor
- Free application: ST motion sensor kit worth 638 yuan, advanced machine learning