New energy vehicle technology is developing rapidly, and best-selling vehicles have gained a leading edge over traditional fuel vehicles in terms of power performance, intelligence, and cost of use. However, "not enough range for long-distance travel" and "inconvenient charging" are the two major pain points for current new energy vehicle consumers. In order to extend the range, major manufacturers have adopted technical solutions to increase battery capacity and provide fast charging solutions to effectively solve charging and range anxiety. As a result, the 800V high-voltage system technology for new energy vehicles came into being.
What is 800V high voltage system?
The name of the 800V high-voltage system comes from the perspective of the vehicle's electrical system. The voltage range of the current mainstream new energy vehicle high-voltage electrical system is generally 230V-450V, with the middle value of 400V, which is generally referred to as a 400V system; and with the application of fast charging, the voltage range of the vehicle's high-voltage electrical system reaches 550-930V, with the middle value of 800V, which can be generally referred to as an 800V system.
The typical feature of the 800V high-voltage system is the voltage platform. The core of fast charging technology is to increase the charging power of the whole vehicle. To increase the charging power of the whole vehicle, the technical means are either to increase the charging current or to increase the charging voltage. Increasing the charging current means thicker and heavier wiring harnesses, more heat generation, and more bottlenecks of auxiliary equipment, while increasing the charging voltage has greater design freedom, which directly promotes the conversion of the 400V voltage platform to the 800V voltage platform.
What does an 800V high-voltage system look like and what are its performances? We can get a glimpse of its true appearance from several 800V electric vehicles that have been mass-produced.
In April 2019, Porsche Taycan Turbo S was launched globally, and the world's first 800V pure electric model was born. In terms of performance, the maximum charging power can reach 320kW, which is 2 to 3 times that of a general 120kW fast charging pile; the high-voltage power battery, front drive motor, rear drive motor, on-board charger and PTC components all use an 800V voltage platform.
On December 2, 2020, Hyundai Motor Group launched the new electric vehicle dedicated platform "E-GMP" globally, which can also achieve 800V function. In terms of performance, the maximum charging power is 350kW, supporting battery charging from 10% to 80% in just 18 minutes; all components including high-voltage power battery, front drive motor, rear drive motor, battery heater, cabin heater and high-voltage air conditioner all adopt 800V voltage platform.
As for domestic car manufacturers, new car-making forces and smart electric brands of traditional car manufacturers have almost all "entered the market", including Xiaopeng, Ideal, Leapmotor, BYD e-platform 3.0, Great Wall Salon, Dongfeng Lantu, Geely Zeekr, BAIC Arcfox, GAC Aion, etc., as shown in the table above.
Adopt 800V high voltage system
What are the advantages over the 400V system?
First, the charging power can be higher, eliminating anxiety about charging time. The industry generally believes that 500A is the limit of automotive-grade wiring harness connectors. If the current is higher, the complexity of electrical system design will increase significantly, which means that the charging power of about 200kW under the 400V system will become the limit of many vehicle designs; and the 800V high-voltage system can break the limit to 400kW. In this case, if the long-range vehicle battery is charged at 100kWh@20%-80%, it only takes 9 minutes, which is basically the same as the time it takes to refuel a traditional fuel vehicle, completely eliminating anxiety about charging time.
Second, the fast charging system is low cost.
There are also fast charging based on 400V system on the market, but 800V high-voltage system can achieve lower system cost in high-power charging applications. Table 1 shows the qualitative comparison of vehicle assembly cost between 400V system and 800V high-voltage system, which is further reflected as follows: In the short term, 800V charging power range above 250kW, and in the long term, 800V charging power range above 150kW, 800V high-voltage system has obvious system cost advantage.
Table 1 Vehicle assembly cost under fast charging application
Third, fast charging has low charging loss.
Compared with the 400V system, the 800V high-voltage system has a small charging current, and the battery loss, wiring harness loss and charging pile loss can all be reduced, achieving energy-saving charging.
Fourth, the vehicle's driving energy consumption is low, and a longer driving range can be achieved with the same battery capacity, or the battery capacity can be reduced and the assembly cost can be lowered with the same driving range.
Compared with the 400V system, the 800V high-voltage system battery, electric drive and other high-voltage components have small currents, and the losses of related components and wiring harnesses can be reduced; secondly, with the introduction of the third-generation semiconductor silicon carbide technology, the energy consumption of various high-voltage components, especially electric drive components, can be greatly reduced, enabling energy-saving driving of the vehicle.
Why use Silicon Carbide Semiconductors
What are the advantages compared to silicon semiconductors?
Silicon carbide has significant performance advantages at the power semiconductor level. Compared with silicon semiconductors, the bandgap width of silicon carbide is three times that of silicon, which enables it to work stably at high temperatures; the electric field strength of silicon carbide is 15 times that of silicon, which makes its on-resistance low and the on-energy consumption low; the electron saturation rate of silicon carbide is twice that of silicon, which can have faster switching speed and reduce switching energy consumption; the thermal conductivity of silicon carbide is 3.5 times that of silicon, which brings better heat dissipation performance (see Figure 1).
Figure 1 Comparison of SiC and Si at the semiconductor level
These advantages contribute to the optimization of high-voltage component design and vehicle optimization, mainly in the following two aspects:
First, silicon carbide MOSFET can significantly improve inverter efficiency and electric drive efficiency, and reduce the energy consumption of the entire vehicle.
Compared with 400V system silicon IGBT, whether it is a 400V system or an 800V high-voltage system, the inverter loss of silicon carbide MOSFET can be reduced by about 50%, improving the efficiency of electric drive and thus reducing the energy consumption of the whole vehicle. The energy consumption analysis of vehicles of different levels (as shown in Figure 2) shows that from the A00 level to the large SUV level, silicon carbide MOSFET electric drive products can reduce the power consumption of the whole vehicle by 5%-7%, that is, the battery life of the same capacity battery can be increased by at least 5%. The data may be a bit confusing, but in plain words, it means saving money.
Figure 2 Analysis of the impact of silicon carbide electric drive technology on vehicle energy consumption
Second, silicon carbide MOSFET has almost irreplaceable advantages in 800V high-voltage electric drive system applications.
As the impedance of high-voltage IGBTs increases, the frequency performance decreases. When the system is increased from 400V to 800V, at the same frequency, the conduction loss and switching loss of Si-IGBT devices increase significantly. If the silicon IGBT technology route is adopted in the 800V high-voltage system field, the cost will increase but the efficiency will decrease. Therefore, in the current 800V high-voltage electric drive field, silicon carbide MOSFET is the only option for efficient electric drive.
The 800V high-voltage system has attracted much attention in the industry. The reasons can be briefly summarized into two aspects: high-power fast charging is the market selling point, and low-cost and high-efficiency system is the technical selling point.
Previous article:Types and main components of ADAS Applications and related technologies of LiDAR
Next article:New energy electric vehicle motor controller composition and working process
Recommended ReadingLatest update time:2024-11-16 10:28
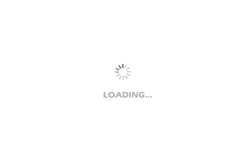
- Popular Resources
- Popular amplifiers
-
Operational Amplifier Practical Reference Handbook (Edited by Liu Changsheng, Zhao Mingying, Liu Xu, etc.)
-
Multi-port and shared memory architecture for high-performance ADAS SoCs
-
Test solutions in the 800V electric drive development and design process (Tektronix China)
-
Research and design of electric vehicle drive motor ECU control software based on AUTOSAR
- Huawei's Strategic Department Director Gai Gang: The cumulative installed base of open source Euler operating system exceeds 10 million sets
- Analysis of the application of several common contact parts in high-voltage connectors of new energy vehicles
- Wiring harness durability test and contact voltage drop test method
- Sn-doped CuO nanostructure-based ethanol gas sensor for real-time drunk driving detection in vehicles
- Design considerations for automotive battery wiring harness
- Do you know all the various motors commonly used in automotive electronics?
- What are the functions of the Internet of Vehicles? What are the uses and benefits of the Internet of Vehicles?
- Power Inverter - A critical safety system for electric vehicles
- Analysis of the information security mechanism of AUTOSAR, the automotive embedded software framework
Professor at Beihang University, dedicated to promoting microcontrollers and embedded systems for over 20 years.
- Innolux's intelligent steer-by-wire solution makes cars smarter and safer
- 8051 MCU - Parity Check
- How to efficiently balance the sensitivity of tactile sensing interfaces
- What should I do if the servo motor shakes? What causes the servo motor to shake quickly?
- 【Brushless Motor】Analysis of three-phase BLDC motor and sharing of two popular development boards
- Midea Industrial Technology's subsidiaries Clou Electronics and Hekang New Energy jointly appeared at the Munich Battery Energy Storage Exhibition and Solar Energy Exhibition
- Guoxin Sichen | Application of ferroelectric memory PB85RS2MC in power battery management, with a capacity of 2M
- Analysis of common faults of frequency converter
- In a head-on competition with Qualcomm, what kind of cockpit products has Intel come up with?
- Dalian Rongke's all-vanadium liquid flow battery energy storage equipment industrialization project has entered the sprint stage before production
- Allegro MicroSystems Introduces Advanced Magnetic and Inductive Position Sensing Solutions at Electronica 2024
- Car key in the left hand, liveness detection radar in the right hand, UWB is imperative for cars!
- After a decade of rapid development, domestic CIS has entered the market
- Aegis Dagger Battery + Thor EM-i Super Hybrid, Geely New Energy has thrown out two "king bombs"
- A brief discussion on functional safety - fault, error, and failure
- In the smart car 2.0 cycle, these core industry chains are facing major opportunities!
- The United States and Japan are developing new batteries. CATL faces challenges? How should China's new energy battery industry respond?
- Murata launches high-precision 6-axis inertial sensor for automobiles
- Ford patents pre-charge alarm to help save costs and respond to emergencies
- New real-time microcontroller system from Texas Instruments enables smarter processing in automotive and industrial applications
- Configuration example of ModbusTCP to Profinet gateway connecting to tightening shaft drive
- What books should Linux newbies read?
- C6000 embedded assembly C and assembly comparison and function description
- MicroPython 1.17 released
- EEWORLD University Hall----Live Replay: ADI's Vital Signs Monitoring Solutions in Wearable Products
- FPGA implementation of SPI42 interface.pdf
- Human-machine ring material——Good to see——【Quality knowledge】
- Three gifts for registering for the conference | Live broadcast of Siemens' full-stack automotive semiconductor solutions - helping automakers form a closed R&D loop!
- MSP430Ware use notes to initialize XT1
- Arrow Electronics' award-winning live broadcast starts at 10:00 this morning: Intel FPGA Deep Learning Acceleration Technology