1. Introduction
Automobile noise, vibration and the ride comfort caused by them, namely NVH (Noise, Vibration & Harshness), is a comprehensive issue to measure the quality of automobile products. It gives the most direct feeling to users and increasingly affects the reputation and market share of products. Therefore, it is generally concerned by major vehicle manufacturers and parts companies. The noise and vibration phenomenon inside the car is often caused by the superposition of multiple excitations that reach the target position through different transmission paths. In the process of developing new automobile products today, in order to further optimize the NVH performance of the whole vehicle, it is often necessary to comprehensively consider the conditions of various excitations and transmission paths, and transfer path analysis (TPA) is an effective method. Through transfer path analysis, the proportion of the excitation energy flowing into each path in the entire problem is determined, and the link that plays a leading role in the transmission path on the vehicle interior noise is found. By controlling these main links, such as making the intensity of the sound source, the acoustic sensitivity of the path and other parameters within a reasonable range, the vehicle interior noise can be controlled within the predetermined target value. This paper analyzes the acoustic vibration transmission path in a domestic car based on the LMS SCANDAS MOBILE SCM05 portable acquisition front end and LMS Test. lab 8A software, and obtains the analysis results, which lays a foundation for further improving the NVH performance of the vehicle.
2. Principle of vehicle acoustic vibration transmission path analysis
In the engineering vibration and noise test and analysis work, spectrum analysis and probability statistical analysis are widely used, but they all have a common disadvantage, which is that the conditions and working conditions of the comparative test are required to be exactly the same, otherwise the comparison cannot be made. At the same time, the working conditions of such tests are very complicated, requiring a lot of data to be processed, and the workload is very large, and it is difficult to fully illustrate the problem with simple charts. The analysis of transfer characteristics can solve the above problems very well, and its analysis results have good comparability. In order to obtain the results, generally only one working condition needs to be selected for the test to obtain satisfactory results. Due to this outstanding advantage of transfer characteristic analysis, it is widely used in practical engineering problems and has been rapidly developed.
In general, the noise inside a car can be divided into two types: structure-borne sound and airborne sound. In the case of structure-borne sound, the excitation source and the target point belong to two different systems. The structure on the excitation source side is called the active side, and the structure on the target point side is called the passive side. Generally, the two are connected at the boundary (which can be called the coupling point) through some coupling elements, which can be specifically manifested as the support, hinges and rubber bushings of the engine and chassis components on the body. For example, the engine as the excitation source is the active side, the body structure is the passive side, and the support between them is the coupling element. The target can be the sound pressure at a certain point, or the vibration of the point in a certain degree of freedom. In the case of airborne sound, there is no coupling point on the path. If there are N radiating sound sources, N transmission paths are formed.
Assuming that the system is linear and time-invariant, the sound pressure or vibration level at the target point in the vehicle is equal to the superposition of the energy propagated into the vehicle along different paths when each excitation source is excited by the working load, as shown in Figure 1. The purpose of TPA is to study the propagation of energy along these paths.
Figure 1 Transfer path analysis model
From the above analysis and assumptions, it can be seen that all partial contributions from different paths constitute the total response
From formula (2), we can see that the main tasks of transfer path analysis include:
(1) Obtaining the working load. For structure-borne sound, it is the working force input on each degree of freedom at each coupling point; for airborne sound, it is the volume velocity/acceleration of the sound source. This work requires a large amount of test data as input, which is the most arduous part of TPA and directly determines the credibility of the analysis results.
(2) Obtaining the path frequency response function. For structure-borne sound, measure the frequency response function from each degree of freedom at the coupling point to the response position. During measurement, the passive and active sides should be decoupled at each coupling point. For airborne sound, measure the frequency response function from the target point to the sound source.
3. Experimental testing
During the trial production of a new domestic B-class car, resonance was found at around 1500rpm. This paper used the LMS SCANDAS MOBILE SCM05 portable acquisition front end and LMS Test. lab 8A software to analyze the acoustic vibration transmission path of the car, found the root cause of the problem, and proposed a solution, laying a solid foundation for further improving the NVH performance of the car.
3.1 Test system
The LMS SCADAS Mobile SCM05 front end and LMS Test. Lab 8A real-time analysis software are seamlessly integrated to form a powerful sound-vibration analyzer and recorder. It has the ease of use of a traditional analyzer, and at the same time it is an advanced noise and vibration measurement system with high-speed performance and powerful measurement capabilities. At the same time, LMS Test. Lab 8A can make the test more efficient and convenient; it can greatly improve the work efficiency of the test department and obtain higher returns from the existing test equipment; even if the available physical prototypes are greatly reduced, it can still obtain more comprehensive and reliable test results and effectively utilize the test data. The test system is shown in Figure 2, which mainly consists of the LMS SCADAS Mobile SCM05 front end (24 channels), LMS Test. Lab 8A analysis software, ICP acceleration sensor and ICP acoustic sensor.
Test system kernel model
Figure 2 Test system composition
3.2 Test condition design
When a car is driving, the excitation force on the car body mainly comes from two aspects. On the one hand, the vibration of the engine and transmission system is transmitted to the car body through the elastic suspension; on the other hand, the uneven road surface causes the tire vibration, which is transmitted to the car body through the suspension and frame. In order to correctly distinguish the source of in-car vibration and noise and its transmission path analysis, the overall isolation test method is adopted, and three different test conditions are designed to analyze the contribution of the engine to the in-car noise and the impact of road excitation on the in-car noise:
(1) Parking test. In the parking test, the car is placed on a lift, the engine is running, and the car remains stationary on the lift. At this time, only the engine excites the car, so the impact of the engine on the car interior noise and the transmission characteristics of the engine vibration noise can be obtained by analyzing the test data at this time;
(2) Coasting over speed bump test. The engine is stopped and the car coasts over the speed bump. At this time, the main excitation of the car is from the road surface. By analyzing the test data at this time, the influence of the road surface on the noise inside the car and the transmission characteristics of the engine vibration noise can be obtained.
(3) Road test. Carry out a normal driving test on the same road surface as the speed bump test. By analyzing the vibration and noise signals of the car at this time and combining the conclusions of the in-situ test and the speed bump test, analyze the impact of engine and road excitation on the car interior noise under normal driving conditions.
Through the tests of the above three working conditions, we can find a correct, reliable and convenient test means and analysis method to study the noise inside the car, which is convenient for correctly analyzing the source and transmission path of the noise inside the car.
3.3 Data Collection and Analysis
The data acquisition and analysis part of the test system uses the LMS Test. Lab 8A/Advanced Signature Testing module. After the computer, acquisition front end and sensor are connected, the software automatically completes data acquisition and storage through channel setting, measurement bandwidth and trigger setting, and automatic setting of input signal range. It is worth mentioning that the "Time Recording During Signature Testing" function module must be checked in the function option "add-in" so that the test data can be used in the subsequent analysis. The layout positions of sensors for various working conditions are shown in Table 1.
The test data of the road test were analyzed by order, as shown in Figures 3 and 4. At about 1500rpm, the noise and vibration in the car reached their maximum values, and the second-order vibration played a major role at this time. The data were then analyzed by spectrum, as shown in Figures 5 and 6. At about 50Hz, the noise and vibration in the car reached their peak values. The fundamental frequency formula of the main exciting force of a four-stroke engine is: (f=n/(60*t))=1500/(60×2)=12.5Hz, and as a four-cylinder engine, its fundamental frequency is 12.5Hz×2=25Hz, and the second order is 50Hz. The above situation shows that 50Hz is the frequency that causes the noise and vibration in the car to reach their peak values, and it is also in the main frequency band (20Hz~200Hz) that causes people to feel subjectively uncomfortable.
Previous article:Research and Analysis on Vibration Characteristics and Optimization Process of Automobile Exhaust System
Next article:The structural principle of LMS QTV and its use to measure the torsional vibration of the engine crankshaft
Recommended ReadingLatest update time:2024-11-16 09:37
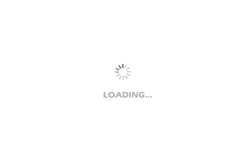
- Huawei's Strategic Department Director Gai Gang: The cumulative installed base of open source Euler operating system exceeds 10 million sets
- Analysis of the application of several common contact parts in high-voltage connectors of new energy vehicles
- Wiring harness durability test and contact voltage drop test method
- Sn-doped CuO nanostructure-based ethanol gas sensor for real-time drunk driving detection in vehicles
- Design considerations for automotive battery wiring harness
- Do you know all the various motors commonly used in automotive electronics?
- What are the functions of the Internet of Vehicles? What are the uses and benefits of the Internet of Vehicles?
- Power Inverter - A critical safety system for electric vehicles
- Analysis of the information security mechanism of AUTOSAR, the automotive embedded software framework
Professor at Beihang University, dedicated to promoting microcontrollers and embedded systems for over 20 years.
- Innolux's intelligent steer-by-wire solution makes cars smarter and safer
- 8051 MCU - Parity Check
- How to efficiently balance the sensitivity of tactile sensing interfaces
- What should I do if the servo motor shakes? What causes the servo motor to shake quickly?
- 【Brushless Motor】Analysis of three-phase BLDC motor and sharing of two popular development boards
- Midea Industrial Technology's subsidiaries Clou Electronics and Hekang New Energy jointly appeared at the Munich Battery Energy Storage Exhibition and Solar Energy Exhibition
- Guoxin Sichen | Application of ferroelectric memory PB85RS2MC in power battery management, with a capacity of 2M
- Analysis of common faults of frequency converter
- In a head-on competition with Qualcomm, what kind of cockpit products has Intel come up with?
- Dalian Rongke's all-vanadium liquid flow battery energy storage equipment industrialization project has entered the sprint stage before production
- Allegro MicroSystems Introduces Advanced Magnetic and Inductive Position Sensing Solutions at Electronica 2024
- Car key in the left hand, liveness detection radar in the right hand, UWB is imperative for cars!
- After a decade of rapid development, domestic CIS has entered the market
- Aegis Dagger Battery + Thor EM-i Super Hybrid, Geely New Energy has thrown out two "king bombs"
- A brief discussion on functional safety - fault, error, and failure
- In the smart car 2.0 cycle, these core industry chains are facing major opportunities!
- The United States and Japan are developing new batteries. CATL faces challenges? How should China's new energy battery industry respond?
- Murata launches high-precision 6-axis inertial sensor for automobiles
- Ford patents pre-charge alarm to help save costs and respond to emergencies
- New real-time microcontroller system from Texas Instruments enables smarter processing in automotive and industrial applications
- Some misunderstandings in FPGA learning.zip
- MSP430F5438A supports communication scheme verification based on COAP protocol
- I want to design a sine wave generator.
- [RT-Thread reading notes] Part 1 Simple principles of the kernel
- I worked hard to drive the CC2640 Hanshuo electronic tag.
- Solution to the error empty character constant
- Newbie wants to use PLC to control air conditioner
- Looking for a microcontroller model
- Measurement of radar power, spectrum and related parameters
- [ESP32-Audio-Kit Audio Development Board Review]——(2): Questions about play_mp3_control