The Lexus UX300e released at the Guangzhou Auto Show is the first e-TGNA model we have seen with detailed battery system and vehicle parameters. We can talk about what the details of this system reflect, which we divide into three parts: overall Pack parameters, module design, and electrical design.
The overall parameters of the Pack
UX300e are positioned as a compact SUV, with a NEDC comprehensive range of 400km. It will be sold in China in 2020. The battery energy is 54.3kWh and the fast charging power is 50kW. According to the definition given in the previous "Toyota challenge Aiming to Popularize BEVs", this is a medium-capacity battery system. What's even more strange about this car is that it is designed with the main front drive, which is different from the current mainstream pure electric vehicle products planned for rear-wheel drive. From the perspective of driving pleasure and power, it is different from the path opened up by Tesla.
If we compare it with MEB, the fast charging power is relatively conservative, and the capacity is 10 kWh less than MEB's 62kWh. Overall, it is still a trial product, which will be promoted from high-end brands first. It is estimated that Toyota still has to plan a higher flagship product above e-TGNA.
The overview of this battery system is shown below. Based on the available information, Toyota mainly insists on two things:
1) Still following the route of small square shell battery cells , a long module is made by extending in the Y direction
2) The distance between modules is quite large, leaving a lot of space for air ducts
From the perspective of layout, the space behind the seats is fully utilized
as shown in the figure below. This car is quite consistent with the previous e-TGNA layout, and the yellow modules at the back are indeed used to stack two layers, making full use of the space behind the seats and the trunk. However, due to the design of the air cooling system, the previous fan is used.
We can preliminarily guess that this module
should be the same as the previous one, and after stacking, it should be constrained by the structure to form a very long module. There are two considerations here.
The cell is pressurized through structural constraints, leaving room for expansion
There are gaps between the cells. After the valve is opened and ruptured under thermal runaway conditions, there is a certain natural thermal resistance in the Y direction. The directionality of heat release is mainly derived through the design of the valve.
The space between modules prevents propagation in the X direction from being too fast.
This module is actually going in the same direction as before, and its advantages and disadvantages are very obvious. Generally, we do not accept such a low volume grouping rate.
The electrical design is considered
in this electrical, divided into two units on the left and right: I can't see how the two are divided. Assuming that according to the color, the yellow ones are all high-voltage collection lines, the BMS on the right is probably also integrated, and both sides use a total of 9 high-voltage collection units with connectors. The two units are connected through the communication line in the middle.
In terms of electrical, the fuse and high-voltage MSD are specially placed in the middle of the battery, and independent round wires are used for connection (which may be the bottleneck of high-current charging). In this regard, there are fewer and fewer battery platforms with this independent MSD design.
Considerations for protective structures
At present, Toyota's engineers have given a lot of consideration to the design of the bottom protection, and adopted a bottom longitudinal and transverse beam structure to resist the impact from the ground. This structure should be more effective for the bottom ball impact experiment currently emphasized in Europe and the United States, but the cost and weight here are a bit of a headache.
The picture below looks like there is only a bottom protection plate, but in fact, combined with the structure above, it takes up a lot of space in the Z direction.
Judging from the performance parameters, the battery system defined by Toyota is similar to the 52kWh & 400km car that we are currently using on a large scale in early 2019. There are no outstanding features in terms of parameters, but the design of the battery system has obvious inertia and conservative safety considerations.
Previous article:Is the tech giant Huawei also "crossing over" into the automotive field?
Next article:Tesla stock downgraded from 'buy' to 'hold' over pickup truck?
Recommended ReadingLatest update time:2024-11-16 11:32
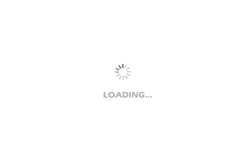
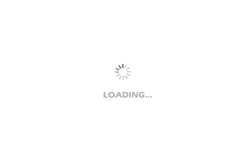
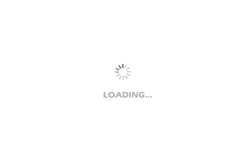
- Huawei's Strategic Department Director Gai Gang: The cumulative installed base of open source Euler operating system exceeds 10 million sets
- Analysis of the application of several common contact parts in high-voltage connectors of new energy vehicles
- Wiring harness durability test and contact voltage drop test method
- Sn-doped CuO nanostructure-based ethanol gas sensor for real-time drunk driving detection in vehicles
- Design considerations for automotive battery wiring harness
- Do you know all the various motors commonly used in automotive electronics?
- What are the functions of the Internet of Vehicles? What are the uses and benefits of the Internet of Vehicles?
- Power Inverter - A critical safety system for electric vehicles
- Analysis of the information security mechanism of AUTOSAR, the automotive embedded software framework
Professor at Beihang University, dedicated to promoting microcontrollers and embedded systems for over 20 years.
- Innolux's intelligent steer-by-wire solution makes cars smarter and safer
- 8051 MCU - Parity Check
- How to efficiently balance the sensitivity of tactile sensing interfaces
- What should I do if the servo motor shakes? What causes the servo motor to shake quickly?
- 【Brushless Motor】Analysis of three-phase BLDC motor and sharing of two popular development boards
- Midea Industrial Technology's subsidiaries Clou Electronics and Hekang New Energy jointly appeared at the Munich Battery Energy Storage Exhibition and Solar Energy Exhibition
- Guoxin Sichen | Application of ferroelectric memory PB85RS2MC in power battery management, with a capacity of 2M
- Analysis of common faults of frequency converter
- In a head-on competition with Qualcomm, what kind of cockpit products has Intel come up with?
- Dalian Rongke's all-vanadium liquid flow battery energy storage equipment industrialization project has entered the sprint stage before production
- Allegro MicroSystems Introduces Advanced Magnetic and Inductive Position Sensing Solutions at Electronica 2024
- Car key in the left hand, liveness detection radar in the right hand, UWB is imperative for cars!
- After a decade of rapid development, domestic CIS has entered the market
- Aegis Dagger Battery + Thor EM-i Super Hybrid, Geely New Energy has thrown out two "king bombs"
- A brief discussion on functional safety - fault, error, and failure
- In the smart car 2.0 cycle, these core industry chains are facing major opportunities!
- The United States and Japan are developing new batteries. CATL faces challenges? How should China's new energy battery industry respond?
- Murata launches high-precision 6-axis inertial sensor for automobiles
- Ford patents pre-charge alarm to help save costs and respond to emergencies
- New real-time microcontroller system from Texas Instruments enables smarter processing in automotive and industrial applications
- TI eSports training video recommendation
- How to choose world-class automotive RF products?
- Good information on clock division
- I thought there was something wrong with IAR, but it turns out that I can input in multiple locations at the same time.
- Permanent magnet brushless motor and its driving technology
- Using cartridges and the ESP8266 microcontroller, a master gave Game Boy the ability to surf the Internet
- A way to significantly improve the distortion of audio playback systems
- MSP430F149
- It is time to accumulate some knowledge on GaN power device design when developing switching power supplies
- Brief Introduction to the Principle and Design of Flyback Converter