1 Introduction to DVI
In 1999, the Digital Display Working Group (DDWG) jointly formed by Silicon Image, Intel, Compaq, IBM, HP, NEC, Fuiitsu and other companies launched the Digital Display Interface (DVI, Digital Visual Interface) standard.
The DVI standard was officially launched by DDWG in April 1994. It is based on the PanalLink interface technology of Silicon Image. The PanalLink interface technology uses the Transition Minimized Differential Signaling (TMDS) as the basic electrical connection. The image information generated in the computer is transmitted to the display processing unit (graphics card), processed and encoded into a data signal. The data signal contains some pixel information, synchronization information and some control information. The information is output through three channels. At the same time, there is a channel for transmitting the clock signal that synchronizes the sending and receiving ends. The data in each channel is transmitted in differential signal mode, so each channel requires 2 transmission lines. Due to the use of differential signal transmission, the voltage difference signal is recognized in data transmission and reception, so the length of the transmission cable has little effect on the signal, and long-distance data transmission can be achieved. The received data is decoded at the receiving end, and the image information is processed to be displayed by the digital display device. The DVI standard strictly defines and regulates the physical mode, electrical indicators, clock mode, encoding mode, transmission mode, data format, etc. of the interface. For digital display devices, since there is no D/A and A/D conversion process, the loss of image details is avoided, thereby ensuring the complete reproduction of computer-generated images. A hot plug monitoring signal is also added to the DVI interface standard, thus truly realizing plug and play.
DVI has two standards, DVI1.0 and DVI2.0. DVI1.0 only uses one set of signal transmission channels (data0~data2). The highest pixel clock for transmitting images is 165M, the highest signal transmission code stream in the channel is 1.65 GHz, and the highest resolution can reach 1600x1200x60. DVI2.0 uses all two signal transmission channels (data0~data5), with the highest pixel clock of the transmitted image being 330M, supporting 1920x1280 resolution and HDMI format, and the highest signal transmission code rate in each channel is also 1.65 GHz. DVI signals have
their particularity in the transmission process, that is, due to the excessively fast data code rate, the transmission distance is limited. Taking 1600×1200×60 as an example, according to regulations, it can be transmitted for 5m, but in current practical applications, it can be completed for about 7m. Taking 1280x1024x70 as an example, it can be transmitted for 10m; 1024x768x75 can be transmitted for 13~14m.
2 DVI types and parameters
There are three types of DVI connectors, namely DVI-Digital (DVI-D), DVI-Analog (DVI-A) and DVI-Integrated (DVI-I). DVI-Digital (DVI-D) only supports digital display devices, DVI-Analog (DVI-A) only supports analog display devices, and DVI-Integrated (DVI-I) supports both digital and analog display. From the interface definition, it can be seen that DVI-I actually adds an analog interface on the basis of DVI-D. The reason for this combination is that although DVI is a standard set for digital display devices, the effect of the picture will not be reduced through digital transmission, and in order to consider the ability to convert into analog signals, there are three types of connectors: DVI-D, DVI-A and DVI-I. Among them, DVI-I is compatible with DVI-D devices (including connecting cables), but DVI-D connectors cannot use DVI-I connecting cables, so digital display devices are DVI-D connectors, connecting cables are DVI-I connectors, and display cards are DVI-I connectors. And DVI-I can also be converted to D-sub 15pin.
DVI can achieve several different resolutions from VGA to 0XGA as shown in Table 1.
The resolution comparison table of dual-link DVI and single-link DVI is shown in Table 2.
The video frame consists of VSYNC video lines, each line consists of HSYNC pixels, the "AND" function of the horizontal gate and the vertical gate is the visible area, and the other areas of the image are blanking areas. There are many different VGA modes. The following is an explanation of the parameters of various common modes. The various timing parameters in the VGA mode are given for reference. The horizontal (line) timing is shown in Table 3, and the vertical (field) timing is shown in Table 4.
When the effective time increases, it exceeds the rising edge of the field synchronization signal, so the leading edge is -1. In actual design, how to determine the appropriate display mode through different system frequencies? For example, in a certain development board, the system clock frequency of the FPGA is 50 MHz. This clock frequency can be used to design a display mode of 800x600. In order to achieve a good display effect, the field frequency (refresh frequency) is 75 Hz, so the frame length can be determined as 666, and the total line length is designed to be 1 000 pixels.
3 Application in airborne radar systems In the
past, airborne radars mostly used PAL video signals or VGA signals. In this design, according to the relevant characteristics of DVI and the specific needs of airborne radars, a DVI system as shown in Figure 1 was designed.
The implementation process is as follows: PPC405 writes the image data to be displayed into the display memory according to the row and column requirements, and the video timing circuit and the display memory address formation circuit send the display memory data to the DVI interface circuit according to the DVI display requirements. The DVI interface circuit then forms a differential high-speed serial signal and a clock signal and sends them to the DVI display through a DVI dedicated cable. In Figure 1, except for the DVI interface circuit, all other circuits are formed by FPGA, which can flexibly form different row and field signals and display buffer areas that meet the requirements.
The design diagram of SiI1160, a key component of DVI (DVI interface chip), is shown in Figure 2. The digital video signal is generated by FPGA (XC2VPS0). Since XC2VP50 has relatively rich internal resources, the CPU (PPC405) that controls the entire graphics generation uses the hard core inside the chip to implement almost all devices except the DVI interface device (including VRAM, CPU, FLASH, control logic circuit, etc.). Since many signals of SiI1160 are high-speed digital signals, sufficient electromagnetic protection components should be added around the device. The CLK signal of SiI1160 is determined by the resolution of the displayed image. The specific selection is as described in the previous table. The device has a digital phase-locked loop circuit inside the chip for frequency multiplication. In order to ensure the stable and reliable operation of the phase-locked loop circuit, it is necessary to provide a stable power supply to the phase-locked loop circuit, such as W1 in Figure 2. The analog power supply needs to be provided after inductive isolation, and the output digital image signal needs to be processed by the filter circuit shown in the figure before output, so as to ensure the stable transmission of high-speed data.
In the past, airborne radars generally used TV-format video signals or VGA-format signals. These signals are all analog signals. When analog signals are used for liquid crystal display, they need to be converted from D/A to A/D first, so there is a certain degree of information loss. The use of DVI display interface design can effectively avoid the information loss introduced by digital-to-analog conversion, and maximize the authenticity and integrity of radar display signals.
The successful application of DVI display interface has introduced a fully digital display method for airborne radars without any information loss in the signal transmission link. Due to the above advantages, this method will be used more and more in future airborne radars. In the engineering design
of printed circuit boards, it is necessary to design according to the requirements of digital high-frequency circuits, pay attention to the protection of differential signals, and route according to the requirements of differential signals (such as keeping equal length and parallel, etc.). Pay attention to electromagnetic protection when routing around DVI interface devices to reduce signal loss.
4 Conclusion
From the current trend, DVI will be applied in more and more fields due to its advantages of supporting high-resolution display (up to 2 048x1 536 in dual-channel) and no information loss, and the increasing popularity of digital display devices. More and more radars have proposed to use DVI for display due to many considerations, and DVI is mature in technology. I believe that in the near future, the application of DVI display interface in radar will increase.
Previous article:Design of knife switch interface control box based on dual FPGA
Next article:Design and implementation of SoC prototype verification based on FPGA
Recommended ReadingLatest update time:2024-11-16 16:37
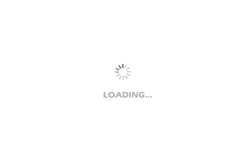
- Popular Resources
- Popular amplifiers
-
Raspberry Pi Development in Action (2nd Edition) ([UK] Simon Monk)
-
FPGA Verilog Development Practical Guide Based on Intel Cyclone IV (Part 2) (Wildfire)
-
Teach you how to design FPGA step by step: the simplest design method based on the principle of simplicity (Pan Wenming)
-
FPGA Technology Basic Engineering Practice-Based on Vivado and Verilog HDL
- Huawei's Strategic Department Director Gai Gang: The cumulative installed base of open source Euler operating system exceeds 10 million sets
- Analysis of the application of several common contact parts in high-voltage connectors of new energy vehicles
- Wiring harness durability test and contact voltage drop test method
- Sn-doped CuO nanostructure-based ethanol gas sensor for real-time drunk driving detection in vehicles
- Design considerations for automotive battery wiring harness
- Do you know all the various motors commonly used in automotive electronics?
- What are the functions of the Internet of Vehicles? What are the uses and benefits of the Internet of Vehicles?
- Power Inverter - A critical safety system for electric vehicles
- Analysis of the information security mechanism of AUTOSAR, the automotive embedded software framework
Professor at Beihang University, dedicated to promoting microcontrollers and embedded systems for over 20 years.
- Innolux's intelligent steer-by-wire solution makes cars smarter and safer
- 8051 MCU - Parity Check
- How to efficiently balance the sensitivity of tactile sensing interfaces
- What should I do if the servo motor shakes? What causes the servo motor to shake quickly?
- 【Brushless Motor】Analysis of three-phase BLDC motor and sharing of two popular development boards
- Midea Industrial Technology's subsidiaries Clou Electronics and Hekang New Energy jointly appeared at the Munich Battery Energy Storage Exhibition and Solar Energy Exhibition
- Guoxin Sichen | Application of ferroelectric memory PB85RS2MC in power battery management, with a capacity of 2M
- Analysis of common faults of frequency converter
- In a head-on competition with Qualcomm, what kind of cockpit products has Intel come up with?
- Dalian Rongke's all-vanadium liquid flow battery energy storage equipment industrialization project has entered the sprint stage before production
- Allegro MicroSystems Introduces Advanced Magnetic and Inductive Position Sensing Solutions at Electronica 2024
- Car key in the left hand, liveness detection radar in the right hand, UWB is imperative for cars!
- After a decade of rapid development, domestic CIS has entered the market
- Aegis Dagger Battery + Thor EM-i Super Hybrid, Geely New Energy has thrown out two "king bombs"
- A brief discussion on functional safety - fault, error, and failure
- In the smart car 2.0 cycle, these core industry chains are facing major opportunities!
- The United States and Japan are developing new batteries. CATL faces challenges? How should China's new energy battery industry respond?
- Murata launches high-precision 6-axis inertial sensor for automobiles
- Ford patents pre-charge alarm to help save costs and respond to emergencies
- New real-time microcontroller system from Texas Instruments enables smarter processing in automotive and industrial applications
- 【GD32L233C-START Review】17. Completed work: Indoor environment monitoring equipment
- [Atria AT32WB415 Series Bluetooth BLE 5.0 MCU] Part 3: Lightble Control OLED Display
- Car sunlight sensor, urgent help
- Communication Principles_matlab.pdf
- Fundamentals of Spectrum Analysis
- Linux/UNIX System Programming Manual (Volumes 1 and 2)
- [ESK32-360 Review] + Serial communication and applications
- EEWORLD University Hall----Live Replay: TI's new generation of low-power Bluetooth microcontrollers helps you reduce application costs
- [Hua Diao Experience] 05 Building a development environment for Xingkong board: SSH connection and Jupyter programming
- What birthday gift should I give to my mother?