Summary
轮毂马达已经开始在电动汽车(EV)中得到应用,这项技术的采用可去除差速器(differential)和传动轴(driveshaft)等装置,能够使电动汽车显著地节省空间。但是,该方法也带来了一些技术挑战,例如增加了簧下重量(unsprung weight)。本文将介绍轮毂马达的发展状况,并讨论驱动电子设备等一些设计集成问题。
In-wheel motors: an innovative approach to electric vehicle drivetrains
The development of automotive technology has always been a conservative but evolving process, and even in the context of profound technological changes in electric vehicles, designers are "trying to make it safe", hoping to make the overall layout, shape and feel of electric vehicles as similar as possible to traditional internal combustion engine (ICE) powered vehicles. As a result of this approach, electric vehicle designs have so far tended to use a single motor instead of a gasoline or diesel engine , combined with a traditional drive shaft, differential gearbox and front-wheel drive, constant velocity joint arrangement. Designs with multiple motors do exist, but these motors are usually still fixed within the vehicle chassis and connected to the wheels through mechanical connections.
At the end of the 19th century, Ferdinand Porsche had a great idea. He developed a "horseless carriage" based on the "Lohner-Porsche Electric Vehicle" (Figure 1), which had a battery-powered motor embedded in the center of each wheel hub, which was then charged by the onboard gasoline engine. The control of the motor was a basic requirement, but it eliminated the power loss of the traditional powertrain and ICE transmission. The design at the time was very heavy due to its low power, and the weight of one and a half tons, and the endurance was poor. Therefore, the car disappeared in history due to its weird performance.
Figure 1: Lohner-Porsche electric vehicle with central wheel hub motor drive.
However, the concept of in-wheel motors is now seeing a resurgence, notably in the Lunar Roving Vehicle (LRV) of the early 1970s, and more recently in road-going vehicles. Sometimes referred to as “drive wheel” technology, in-wheel motors were pioneered by Michelin in the late 2000s[1] and continue to be developed today, with concept demonstrations such as Nissan’s “BladeGlider”[2] showing that the technology is a viable option.
Advantages of wheel hub motors
Up to four wheel hub motors may seem more complex than a single chassis-mounted motor, but from a system-wide perspective, this layout has real advantages: Direct wheel drive eliminates energy losses from the centralized motor to the drivetrain, eliminates the need for a mechanical differential, and reduces overall system weight. One company working on wheel hub drive systems claims that the overall weight savings and energy savings from direct wheel drive can increase driving range by more than 30%, depending on battery size and driving cycle[3]. Wheel hub motors can be very compact and can be removed along with the drive shaft and differential, allowing for more cab space and greater layout flexibility. If the drive electronics are also integrated, wiring can be simplified to just one power and return line, compared to at least three power cables to each motor if the traction drive inverter is mounted on the chassis. Keeping the VFD inside the wheel hub motor also reduces electromagnetic radiation from the cabling.
A major benefit of wheel hub motors is that they can improve driving dynamics and safety. In conventional internal combustion engines, complex mechanical devices are needed to provide anti-lock braking and traction control to prevent the wheels from slipping on bad roads and when turning. Differentials also allow the wheels to rotate at different speeds when turning to reduce tire wear and improve handling performance, and some include some advanced configurations such as "limited slip" for off-roading. These systems can be very complex, requiring electronics to sense wheel speed and actual torque, but in the end, the only control available is to increase or decrease the power of the entire engine, or brake a certain wheel.
With a single fixed motor, some mechanical and electrical complexity must be retained, despite differences from ICEs such as reversing the motor to use its torque for an overall braking effect. In-wheel motors can control torque, target wheel speed, and braking separately, and react to sensors and driver inputs at each wheel. So-called “torque vectoring” can apply power to each wheel separately for optimal handling and safety (see Figure 2). Although the in-wheel motor can convert energy to battery power and achieve braking effect by reversing its torque, hydraulic/friction brakes are still required to avoid overloading the motor drive during strong braking.
Figure 2: In-wheel motors allow for simple torque vectoring.
However, in-wheel motors also have disadvantages, requiring multiple motors, each with its own electronic drive, and total cost higher than a single motor of equivalent power output. However, it can be concluded that the energy savings of in-wheel motors will eventually offset these costs, while their safety and performance advantages, additional cabin space and range improvements are also very valuable.
But there are still some practical issues. The wheel hub motors are now part of the vehicle's "unsprung weight", that is, they are part of the components that are not supported by the suspension system. This will undoubtedly affect the handling, but testing has shown that in normal driving within certain weight limits, the effects are not disruptive. The wheel hub motors, drive electronics and mechanical components are also in a harsher working environment than if a single motor were enclosed inside the chassis and cushioned by coil suspension and shock absorbers.
Harsh environment
Unsprung components in a vehicle are subject to the harshest working environment. They are subject to vibration and shock caused by the road, are easily affected by road debris, and may be exposed to corrosive fluids such as water and salt generated during road treatment. The adjacent friction brakes generate heat, and the wheel hub motor and its drive electronics generate a lot of heat even if they are very energy-efficient. In order to maintain a long service life and reliable operation, the wheel hub motor and its components must be very robust and reliable. Any failure resulting in locking or even sudden loss of power may be fatal. Of course, they need to meet the automotive quality standard ISO 26262, and for functional safety and systems, the highest level of Automotive Safety Integrity Level (ASIL) D must be achieved. The individual components need to be properly certified, passive and active components from qualified automotive electronics suppliers need to be AEC-Qxx certified, and design and manufacturing must meet ISO/TS 16949 quality standards at the Production Part Approval Process (PPAP) level.
Drive electronics
Although technological advances have enabled motor miniaturization, drive electronics are always a size and weight consideration when embedding a motor in a wheel hub. The traction motors used are mostly permanent magnet synchronous motors (PMSMs), which require a three-phase variable frequency drive through a "bridge" arrangement of semiconductor switches under pulse width modulation (PWM) control. The bridge switches at high frequency, and its output effective amplitude is set by the pulse width to meet the torque demand (see Figure 3).
Figure 3: Electric vehicle motor drive using MOSFETs.
Electric vehicles have also followed the usual conservative approach, with designs so far mainly using IGBTs as switches, a technology that has been around since the 1960s and, despite years of improvements, has limited the bridge PWM clock speed required to achieve reasonable efficiency, as higher frequencies when the devices are switched mean more transients per second, resulting in more losses. For this reason, especially at high power, motor drives are often switched at frequencies below 10kHz, resulting in relatively high ripple voltages and currents that are detrimental to the motor's control response, in addition to generating differential and common-mode interference currents that are difficult to filter out. The limited efficiency that can be achieved also reflects the large heat sinks that must be used for in-wheel motor drives, resulting in a heavy and bulky system.
In order to achieve better results in terms of motor control and EMI, faster switching speeds, improved efficiency, and reduced system size and weight, hub motors are adopting some new semiconductor switching technologies. Silicon carbide (SiC) MOSFET, as a wide bandgap device, is a typical choice to meet the above requirements. This technology has low conduction losses, high operating temperature, and the device can switch very quickly with very low losses, so that the PWM frequency can reach tens of kHz. SiC devices can switch at MHz rates, and unlike in general power applications, where the size of the transformer is greatly reduced, this does not have any practical significance in motor control. A characteristic of the motor control bridge circuit is that "commutation" occurs, that is, during the switching "dead time" and regeneration, the current flows in the opposite direction to the normal direction. Therefore, a fast parallel diode must be added to the IGBT for this purpose. However, with SiC MOSFETs, there is a built-in "body" diode that can perform this function, although in some cases it can be bypassed by an external diode for the highest efficiency. SiC MOSFETs have appropriate voltage and current ratings to provide the highest required battery voltage and wheel power levels, currently typically around 80kW. For a single chassis-mounted motor, the electronic drive must provide the full vehicle power, which can be hundreds of kilowatts, so choosing between IGBTs and SiC MOSFETs is not an easy task, as IGBTs typically offer the highest current ratings.
Mouser Electronics offers a broad range of automotive-grade SiC MOSFETs, IGBTs, and other active/passive and electromechanical components, including products from Infineon, STMicroelectronics, Texas Instruments, and Wolfspeed Cree.
Previous article:What changes will Bosch's first electric CVT transmission bring to electric vehicles?
Next article:Power Distribution Control Solutions
Recommended ReadingLatest update time:2024-11-16 12:57
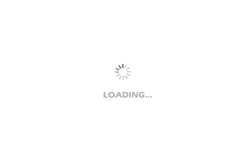
- Popular Resources
- Popular amplifiers
- Car key in the left hand, liveness detection radar in the right hand, UWB is imperative for cars!
- After a decade of rapid development, domestic CIS has entered the market
- Aegis Dagger Battery + Thor EM-i Super Hybrid, Geely New Energy has thrown out two "king bombs"
- A brief discussion on functional safety - fault, error, and failure
- In the smart car 2.0 cycle, these core industry chains are facing major opportunities!
- The United States and Japan are developing new batteries. CATL faces challenges? How should China's new energy battery industry respond?
- Murata launches high-precision 6-axis inertial sensor for automobiles
- Ford patents pre-charge alarm to help save costs and respond to emergencies
- New real-time microcontroller system from Texas Instruments enables smarter processing in automotive and industrial applications
- Innolux's intelligent steer-by-wire solution makes cars smarter and safer
- 8051 MCU - Parity Check
- How to efficiently balance the sensitivity of tactile sensing interfaces
- What should I do if the servo motor shakes? What causes the servo motor to shake quickly?
- 【Brushless Motor】Analysis of three-phase BLDC motor and sharing of two popular development boards
- Midea Industrial Technology's subsidiaries Clou Electronics and Hekang New Energy jointly appeared at the Munich Battery Energy Storage Exhibition and Solar Energy Exhibition
- Guoxin Sichen | Application of ferroelectric memory PB85RS2MC in power battery management, with a capacity of 2M
- Analysis of common faults of frequency converter
- In a head-on competition with Qualcomm, what kind of cockpit products has Intel come up with?
- Dalian Rongke's all-vanadium liquid flow battery energy storage equipment industrialization project has entered the sprint stage before production
- Allegro MicroSystems Introduces Advanced Magnetic and Inductive Position Sensing Solutions at Electronica 2024
- Car key in the left hand, liveness detection radar in the right hand, UWB is imperative for cars!
- After a decade of rapid development, domestic CIS has entered the market
- Aegis Dagger Battery + Thor EM-i Super Hybrid, Geely New Energy has thrown out two "king bombs"
- A brief discussion on functional safety - fault, error, and failure
- In the smart car 2.0 cycle, these core industry chains are facing major opportunities!
- The United States and Japan are developing new batteries. CATL faces challenges? How should China's new energy battery industry respond?
- Murata launches high-precision 6-axis inertial sensor for automobiles
- Ford patents pre-charge alarm to help save costs and respond to emergencies
- New real-time microcontroller system from Texas Instruments enables smarter processing in automotive and industrial applications
- Does the boost topology circuit limit the duty cycle?
- Op amp differential amplification problem
- FAQ_How to fill in the BQB certification application form
- [2022 Digi-Key Innovation Design Competition] Material Unboxing Raspberry Pi 400
- HC6800 EM3 V2.0 CD-ROM
- Share the temperature and humidity monitoring of LoRa communication technology
- [TI star product limited time purchase] + AWR6843 purchase experience and unboxing
- EEWORLD University ---- VLSI Testing
- 【STEVAL-MKI109V3+LSM6DSOX】Build a test environment from scratch
- Python3 string substring search, replacement, deletion, splitting, connection related methods