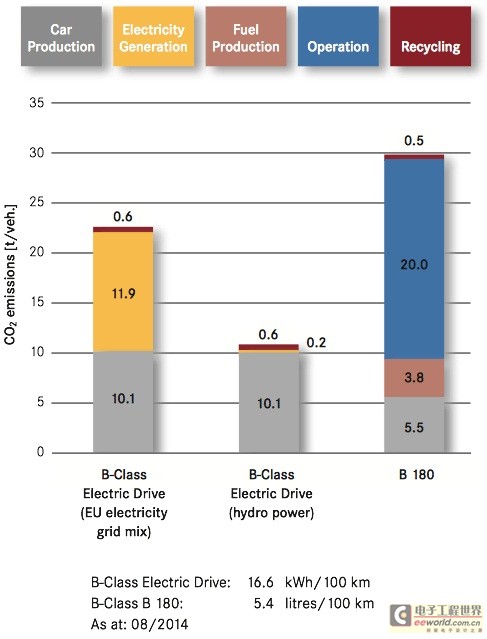
Recently, Mercedes-Benz and Süddeutsche Group jointly released a report on the carbon dioxide emissions of Mercedes-Benz B-Class electric vehicles. The report pointed out that when the charging electricity of Mercedes-Benz B-Class electric vehicles is hydroelectric, its carbon dioxide emissions throughout its life cycle can be reduced by 64% compared with the ordinary Mercedes-Benz B180 model. The output power of Mercedes-Benz B-Class electric vehicles can reach 132 kilowatts, and its cruising range can reach 200 kilometers (about 124 miles). In addition, Süddeutsche Group also evaluated the carbon dioxide emissions of Mercedes-Benz B-Class electric vehicles throughout their life cycle according to the ISO standard TR 14962. Based on the evaluation results, Süddeutsche Group awarded the Sports Tourer model the title of green and environmentally friendly car.
Although the carbon dioxide emissions generated by electric vehicles during the manufacturing process are relatively higher than those of ordinary vehicles, for Mercedes-Benz B-Class electric vehicles, the total mileage can exceed 160,000 kilometers (about 99,419 miles) during its entire life cycle (including the manufacturing process), and its battery charge and discharge cycle also meets the life requirements. Under the same conditions, when the charging power is hydropower, the carbon dioxide emissions during its entire life cycle can be reduced by 19 tons compared with the ordinary Mercedes-Benz B180 model, and the reduction can reach 64%; when the charging power is the ordinary European hybrid power, the carbon dioxide emissions during its entire life cycle can be reduced by 7.2 tons compared with the ordinary Mercedes-Benz B180 model, and the reduction can reach 24%.
The main reason why the Mercedes-Benz B-Class electric car can significantly reduce the total carbon dioxide emissions throughout its life cycle is that it uses an electric motor with very high working efficiency. Using an electric motor to drive the vehicle is very significant in reducing carbon dioxide emissions during the use of the vehicle. For the Mercedes-Benz B-Class electric car, the key is that it uses an advanced energy management system based on brake energy recovery based on a radar system. Through the application of this system, the vehicle can optimize the brake energy recovery according to the radar system, which further improves the working efficiency of the drive system and ensures a longer driving range.
The carbon dioxide emissions of Mercedes-Benz B-Class electric vehicles during use mainly depend on the process of generating electricity. Under the condition of 160,000 mileage, the carbon dioxide emissions of Mercedes-Benz B-Class electric vehicles when charging electricity is European hybrid electricity are 11.9 tons, which is equivalent to the comprehensive power consumption of 16.6 kWh per 100 kilometers in the European fuel consumption and emission assessment standards. When the charging electricity of Mercedes-Benz B-Class electric vehicles is hydroelectric, the carbon dioxide emissions in the process of generating electricity can be completely ignored, which greatly reduces the overall carbon dioxide emissions of the vehicle. In comparison, the carbon dioxide emissions of ordinary Mercedes-Benz B180 models during use can reach 23.8 tons, and its comprehensive fuel consumption per 100 kilometers in the European fuel consumption and emission assessment standards is 5.4 liters.
Professor Herbert Kohler, Daimler's Chief Environmental Officer, said: "The purpose of launching the Mercedes-Benz B-Class Electric Vehicle is not only to show people that our Mercedes-Benz B-Class has the potential to be developed and improved into an electric vehicle, but more importantly, we want to further provide consumers with a model with lower carbon dioxide emissions while ensuring the vehicle's driving space, safety and comfort. The launch of the Mercedes-Benz B-Class Electric Vehicle is a milestone in the development of zero-emission vehicles for us at Daimler-Benz."
Mercedes-Benz B-Class Electric Vehicle
The Mercedes-Benz B-Class electric car was jointly developed by Mercedes-Benz and Tesla, and the car's power system comes from Tesla. Before that, the battery of Mercedes-Benz's smart fortwo electric car model also came from Tesla.
The electric motor used in the Mercedes-Benz B-Class electric car can reach a maximum output torque of 340 Nm (about 251 lb-ft), and the peak torque data can reach the level of a modern 3.0-liter naturally aspirated gasoline engine. The car can accelerate from 0 to 100 km/h in 7.9 seconds. At the same time, considering the range, its top speed is limited to 160 km/h (about 99 mph).
In the Mercedes-Benz B-Class electric vehicle, steel accounts for the highest proportion of the vehicle weight, accounting for 51.4%, which is about half of the total weight. Composite materials account for the second largest proportion, accounting for 17%. Light alloys account for 12.8%, ranking third. Other materials such as glass and graphite account for 5.9%; non-ferrous materials account for 5%; precious metals account for 4%; and working fluids account for 2.4%. In addition to materials, the remaining components mainly include polymer materials and electronic devices, accounting for 1.5% of the total vehicle weight.
High molecular polymer materials mainly include thermoplastics, synthetic rubber materials, duromer isolation casting resins and non-specific plastics. Among them, thermoplastics have the highest usage ratio, accounting for 11% of the total usage of high molecular polymer materials. Synthetic rubber materials account for 3.6% of the total usage of high molecular polymer materials, ranking second.
The material composition of the Mercedes-Benz B-Class electric car is significantly different from that of the ordinary Mercedes-Benz B-Class gasoline car. Since the Mercedes-Benz B-Class electric car is equipped with a separate power drive system, the proportion of steel used in the whole vehicle is reduced by 8%, the proportion of light alloy and non-ferrous materials is increased by about 3%, and the proportion of precious metals is increased by about 4%. Since the Mercedes-Benz B-Class electric car does not use fuel, the proportion of working fluid used is reduced by 2%.
Previous article:Smart car lithium batteries can warn of fire signs
Next article:New self-tinting glass combines sunshade and battery functions
- Popular Resources
- Popular amplifiers
- Car key in the left hand, liveness detection radar in the right hand, UWB is imperative for cars!
- After a decade of rapid development, domestic CIS has entered the market
- Aegis Dagger Battery + Thor EM-i Super Hybrid, Geely New Energy has thrown out two "king bombs"
- A brief discussion on functional safety - fault, error, and failure
- In the smart car 2.0 cycle, these core industry chains are facing major opportunities!
- The United States and Japan are developing new batteries. CATL faces challenges? How should China's new energy battery industry respond?
- Murata launches high-precision 6-axis inertial sensor for automobiles
- Ford patents pre-charge alarm to help save costs and respond to emergencies
- New real-time microcontroller system from Texas Instruments enables smarter processing in automotive and industrial applications
- Innolux's intelligent steer-by-wire solution makes cars smarter and safer
- 8051 MCU - Parity Check
- How to efficiently balance the sensitivity of tactile sensing interfaces
- What should I do if the servo motor shakes? What causes the servo motor to shake quickly?
- 【Brushless Motor】Analysis of three-phase BLDC motor and sharing of two popular development boards
- Midea Industrial Technology's subsidiaries Clou Electronics and Hekang New Energy jointly appeared at the Munich Battery Energy Storage Exhibition and Solar Energy Exhibition
- Guoxin Sichen | Application of ferroelectric memory PB85RS2MC in power battery management, with a capacity of 2M
- Analysis of common faults of frequency converter
- In a head-on competition with Qualcomm, what kind of cockpit products has Intel come up with?
- Dalian Rongke's all-vanadium liquid flow battery energy storage equipment industrialization project has entered the sprint stage before production
- Allegro MicroSystems Introduces Advanced Magnetic and Inductive Position Sensing Solutions at Electronica 2024
- Car key in the left hand, liveness detection radar in the right hand, UWB is imperative for cars!
- After a decade of rapid development, domestic CIS has entered the market
- Aegis Dagger Battery + Thor EM-i Super Hybrid, Geely New Energy has thrown out two "king bombs"
- A brief discussion on functional safety - fault, error, and failure
- In the smart car 2.0 cycle, these core industry chains are facing major opportunities!
- The United States and Japan are developing new batteries. CATL faces challenges? How should China's new energy battery industry respond?
- Murata launches high-precision 6-axis inertial sensor for automobiles
- Ford patents pre-charge alarm to help save costs and respond to emergencies
- New real-time microcontroller system from Texas Instruments enables smarter processing in automotive and industrial applications
- Briefly describe the application technology of RFID truck frame management
- Filter interference issues
- Application of FPGA in image processing
- [Experience sharing] [Scene reproduction project based on AI camera] AI recognition solution based on Allwinner v831
- How to isolate power modules and non-isolated power supplies respectively
- High Voltage Impedance Tuning Quick Guide
- Will 5G really bring about big changes?
- Today I suddenly thought of this: If resistors of the same resistance are first connected in series and then in parallel, what is the resistance after N?
- Let’s talk about high technology today… Why is a chip so difficult to make?
- I thought foreign manufacturers were indifferent to the RISC-V core...