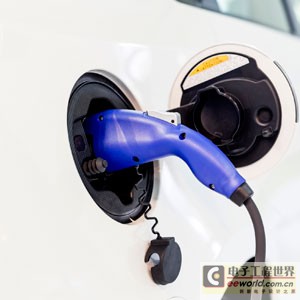
Tesla Model S is the new darling of the electric car industry, but it has recently experienced three consecutive fire incidents (including 60 kWh and 85 kWh battery versions of the car). The detailed cause of the fire is still under investigation.
Thanks to the application of new technology and lightweight materials, the battery pack in the Model S allows it to accelerate from 0-60 mph in just 4.4 seconds. Due to the active nature of these materials, the lithium batteries in the car need to have complete protection measures. The lithium battery pack in the car weighs 500 pounds. It is located in the chassis of the vehicle, the same width as the wheelbase, and slightly shorter than the wheelbase. The actual physical dimensions of the battery pack are: 2.7 meters long, 1.5 meters wide, and 0.1 meters to 0.18 meters thick. The thicker part of 0.18 meters is caused by the superposition of two battery modules. This physical size refers to the overall size of the battery pack, including the upper and lower, left and right, front and back wrapping panels. The structure of this battery pack is a universal design. In addition to the 18650 model battery, other qualified batteries can also be installed. In addition, the battery pack adopts a sealed design, isolated from the air, and most of the materials are aluminum or aluminum alloy. It can be said that the battery is not only an energy center, but also a part of the Model S chassis. Its sturdy shell can provide good support for the vehicle.
But even so, fires still occurred, which is why researchers need to speed up the development of next-generation electric vehicle battery technology.
This summer, the U.S. Department of Energy's Advanced Research Projects Agency (APRA-E) invested $36 million to help researchers lay a solid foundation for the development of next-generation battery designs. The program includes 22 technical projects, all of which aim to make electric vehicles more efficient and less expensive.
Nickel-metal hydride batteries: from hybrid vehicles to pure electric vehicles
Michael Fetcenko, a chemical engineer at BASF, is one of many battery researchers who, with funding from APRA-E, are trying to expand the application of nickel-zinc battery technology originally used in hybrid vehicles to pure electric vehicles.
Generally speaking, the energy density of nickel-metal hydride batteries is 1 kWh/kg. To apply it to pure electric vehicles, BASF must increase the energy density of nickel-metal hydride batteries to 30-50 kWh/kg. The key to the success of this application lies in whether the energy density of nickel-metal hydride batteries can be increased to the required value and the cost can be reduced.
One possible way to achieve this goal is to replace the rare earth elements needed in the battery. Rare earth elements are a general term for 17 elements in this group. They are called rare earth elements not because of their small reserves, but because they are mainly found in mines and will cost a lot of money to develop. In traditional nickel-metal hydride batteries, more than 50% of the energy is generated by the reaction of rare earth elements. However, the storage performance of these elements is poor.
To solve this problem, BASF tried to use low-cost metal hydride alloys. Professor Fetcenko believes that this material can improve the chemical properties of nickel-hydrogen batteries and reduce their costs. However, for pure electric vehicles, improving the chemical properties of nickel-hydrogen batteries is not enough to replace lithium batteries, because lithium batteries also have a crucial characteristic - light weight, or low density.
Zinc-air batteries: from hearing aids to cars
A California-based company called EnZinc believes that zinc-air batteries will lead the next generation of electric vehicle battery technology. Michael Burz, head of the company's research team, said that the next generation of electric vehicle batteries should have three elements: high performance, safety, and low cost. He and his team are trying to change the design mode/architecture of the battery to achieve these three points.
He pointed out that the battery architecture has not changed for more than 100 years, and people still cannot break out of their fixed mindset. The so-called battery architecture consists of three elements: positive electrode, negative electrode, and electrolyte. The positive electrode releases electrons, and the negative electrode receives electrons. The positive and negative electrodes are separated by the electrolyte, which serves as a medium for the free flow of ions.
In lithium-ion batteries, lithium ions move from the lithium oxide positive electrode to the carbon-based compound negative electrode, and an organic electrolyte is used. Zinc-air batteries are different. The positive electrode uses carbon to absorb oxygen from the air, and the negative electrode is a zinc alloy. Zinc is also a benign substance. Its byproduct in the battery is zinc oxide, which is the main ingredient of sunscreen.
Through the above method, zinc-air batteries can achieve the three characteristics of high efficiency, low cost and safety.
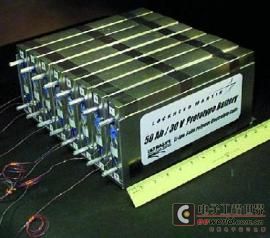
In this case, why not popularize this technology now? Zinc-air batteries cannot be recharged. This is why they are currently only used in small devices such as hearing aids. In order to make zinc-air batteries rechargeable, EnZinc has developed a new solution that places ordinary oxygen and zinc metal in an alkaline electrolyte to generate current through the oxidation reaction of zinc. After recharging, oxygen and zinc can be regenerated, and the cycle repeats, thereby improving the energy density of the battery.
New approach: battery weight reduction
There are many directions for the development of electric vehicle batteries. Some researchers are committed to improving their energy density and performance, while others focus on reducing the weight of batteries. For example, Professor Gabriel Veith and his team at Oak Ridge National Laboratory in the United States are studying how to reduce the weight of battery protection systems.
Gabriel Veith is a materials scientist who wants to develop a lightweight electrolyte material that can perform the same function as a battery safety system.
Veith explained: "When the electric car crashes, the material undergoes a phase change, making it difficult to penetrate." This property may solve the recent Tesla battery fire problem. The problem his team is facing now is to increase the responsiveness of the material. Veith said: "If it only changes phase five minutes after the electric car crashes, it will not make any sense."
Previous article:McLaren's new technology: using high-frequency sound waves to replace windshield wipers
Next article:Defects and solutions of electric vehicle charging
- Popular Resources
- Popular amplifiers
- Car key in the left hand, liveness detection radar in the right hand, UWB is imperative for cars!
- After a decade of rapid development, domestic CIS has entered the market
- Aegis Dagger Battery + Thor EM-i Super Hybrid, Geely New Energy has thrown out two "king bombs"
- A brief discussion on functional safety - fault, error, and failure
- In the smart car 2.0 cycle, these core industry chains are facing major opportunities!
- The United States and Japan are developing new batteries. CATL faces challenges? How should China's new energy battery industry respond?
- Murata launches high-precision 6-axis inertial sensor for automobiles
- Ford patents pre-charge alarm to help save costs and respond to emergencies
- New real-time microcontroller system from Texas Instruments enables smarter processing in automotive and industrial applications
- Innolux's intelligent steer-by-wire solution makes cars smarter and safer
- 8051 MCU - Parity Check
- How to efficiently balance the sensitivity of tactile sensing interfaces
- What should I do if the servo motor shakes? What causes the servo motor to shake quickly?
- 【Brushless Motor】Analysis of three-phase BLDC motor and sharing of two popular development boards
- Midea Industrial Technology's subsidiaries Clou Electronics and Hekang New Energy jointly appeared at the Munich Battery Energy Storage Exhibition and Solar Energy Exhibition
- Guoxin Sichen | Application of ferroelectric memory PB85RS2MC in power battery management, with a capacity of 2M
- Analysis of common faults of frequency converter
- In a head-on competition with Qualcomm, what kind of cockpit products has Intel come up with?
- Dalian Rongke's all-vanadium liquid flow battery energy storage equipment industrialization project has entered the sprint stage before production
- Allegro MicroSystems Introduces Advanced Magnetic and Inductive Position Sensing Solutions at Electronica 2024
- Car key in the left hand, liveness detection radar in the right hand, UWB is imperative for cars!
- After a decade of rapid development, domestic CIS has entered the market
- Aegis Dagger Battery + Thor EM-i Super Hybrid, Geely New Energy has thrown out two "king bombs"
- A brief discussion on functional safety - fault, error, and failure
- In the smart car 2.0 cycle, these core industry chains are facing major opportunities!
- The United States and Japan are developing new batteries. CATL faces challenges? How should China's new energy battery industry respond?
- Murata launches high-precision 6-axis inertial sensor for automobiles
- Ford patents pre-charge alarm to help save costs and respond to emergencies
- New real-time microcontroller system from Texas Instruments enables smarter processing in automotive and industrial applications