introduction
Proton Exchange Membrane Fuel Cell (PEMFC) is a power generation device that converts chemical energy stored in fuel and oxidant into electrical energy. It has the characteristics of high energy, low noise, no pollution, zero emission and high energy conversion efficiency, and is suitable for electric vehicle power source. Governments, enterprises and scientific research institutions of various countries are committed to the research of PEM fuel cell electric vehicles, and the fuel cell engine as its core is currently in the early stage of breakthrough and is becoming a new research and development hotspot. However, many studies only focus on improving the performance of fuel cell stacks, and the research on control systems is relatively small. Traditional control systems are designed according to specific engine characteristics. Their fixed control strategies, line interfaces and operating parameters largely limit the expansion of control functions and cannot meet the user's use and development needs of the control system. The system software is also degraded due to continuous modification during maintenance. In view of this, this paper proposes and designs a new fuel cell engine control system, which not only meets all control objectives but also has the functions of secondary development and upgrading, multiple control strategies optional, etc., which greatly improves the flexibility and adaptability of the control system and achieves good control effects.
System Structure
The system structure of the secondary development control system of the fuel cell engine can be divided into the following parts according to its functions: host computer configuration terminal, soft configurable controller, fuel cell stack, hydrogen supply system, air supply system, humidification system, cooling water management system, safety alarm system and communication monitoring system, as shown in Figure 1. The fuel cell engine uses the host computer as the soft configuration terminal, the controller as the control and coordination center, and the fuel cell stack as the core of the engine. The hydrogen and oxygen entering the stack react under certain conditions to generate electricity and water. The host computer configuration terminal can select different control strategies and perform secondary development and upgrade of the controller; the hydrogen supply system is responsible for providing the fuel cell with pure hydrogen of a certain pressure and flow rate; the air supply system provides the fuel cell with sufficient air for reaction; the humidification system is responsible for providing the fuel cell with appropriate humidity to improve the reaction efficiency; the cooling water management system mainly removes the excess heat from the fuel cell through circulating deionized water and dissipates it through the cooler, so that the fuel cell works under efficient reaction conditions; the safety alarm system detects various states and parameters of the fuel cell in real time during operation, and promptly issues alarm information when a fault occurs; the communication monitoring system can display the current various physical data and operating status in real time, and can record the required data for research and analysis.
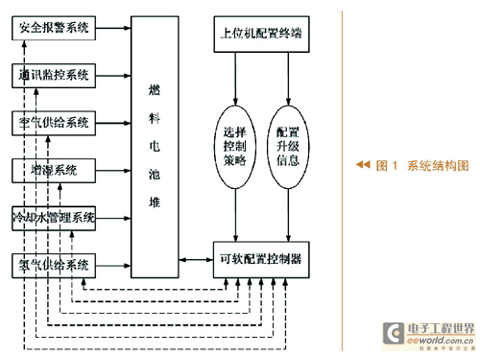
Secondary development and upgrade mechanism
A feature of the secondary development control system of the fuel cell engine is that it can be upgraded online. Existing statistics show that the maintenance workload of the integrity and adaptability of the control system accounts for about 70% of its lifetime workload. It is relatively expensive to passively maintain and modify the control system whose requirements change during its life cycle and then re-burn or even design the controller. The fuel cell engine control system is a control system whose internal structure can be reconfigured and control parameters can be continuously adjusted to meet the hardware environment. According to its upgraded functions, it can be divided into controller port upgrade and parameter upgrade.
Controller
The controller is designed with full consideration of various factors that may change. The main program only retains the main framework, and all variable information is stored separately in a dedicated module. The host configuration terminal is responsible for selecting the system operation strategy and configuring various upgrade information into the controller. Once the system needs to be upgraded, the user can perform simple operations without understanding the control program, which greatly shortens the development cycle of the controller and improves the applicability and operability of the system.
As shown in Figure 2, the controller is mainly composed of a microprocessor (DSP), a watchdog module, a power monitoring module, a soft configuration module, a signal conditioning and analog-to-digital conversion module, a digital-to-analog conversion circuit, an I/O module, an SCI and a CAN communication module. The host configuration terminal is designed with VB software, integrating the upgrade configuration system and the data monitoring system. It can perform soft configuration upgrades and display and record data in real time, and uses 485 communication with the DSP. The soft configuration module uses EEPROM to receive and store upgrade information from the host computer and communicates with the DSP through SPI. The controller is connected to various external analog and digital signals through interfaces. Analog signals include voltage, current, pressure, flow, temperature, humidity, etc., and digital signals include various solenoid valves and relays. The controller realizes the modularization and miniaturization design of the control system, and has high flexibility, high reliability, high anti-interference, high-speed signal processing capability, and advanced secondary development and upgrade.
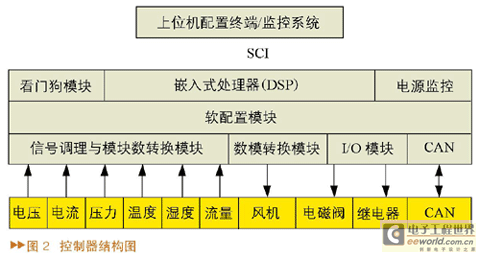
Controller port upgrade
The controller has many control ports in hardware. For example, the analog-to-digital conversion module is connected to a variety of A/D sampling ports. The D/A port of the digital-to-analog conversion module controls several fans at the same time. The I/O module controls the opening and closing of the relay and receives hydrogen alarm information through the I/O port. These hardware ports connected to the controller can be upgraded through software configuration. When the subsystems or stacks of the fuel cell engine control system are tested and rectified, the connection between some lines and the controller ports will inevitably change. At this time, the internal interface settings of the controller can be easily adjusted through the host computer configuration terminal, so that the controller can quickly adapt to the new hardware requirements.
As shown in Figure 3, A/D sampling is the main input channel for signals, and the collected signals include hydrogen inlet and outlet pressure, voltage and current of the battery stack, fan current, inlet and outlet temperature, water level flow of cooling water and humidifying water, etc.; I/O port mainly refers to the digital input and output of DSP, and the output quantity controls the switches of various solenoid valves, water pumps, and motors through the control relay, such as charging load switch, hydrogen and nitrogen tail gas valve, humidifying water pump, and hydrogen circulation pump, etc.; I/O input quantity includes the switch signals of multiple hydrogen alarms; the digital-to-analog conversion module converts the digital quantity output by DSP into analog quantity to control the fan. Each D/A controls a fan, and the size of the output quantity determines the speed of the fan. When the hardware port changes due to the displacement of the battery stack, circuit reorganization, etc., the reconfiguration of the port by the host computer terminal can keep the control system updated with the new hardware requirements without programming.
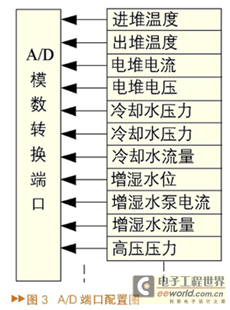
Parameter upgrade
Common parameters used in fuel cell engine control systems include various control parameters, safety parameters, and calibration parameters of different sensors. Among them, control parameters include on/off process control, fan power control, humidification water flow control, exhaust emission control, etc.; safety parameters include various alarm parameters, stack protection parameters (self-shutdown, load reduction), protection delay parameters, etc.; various sensors such as voltage, current, water level, pressure, etc. Sensors are an important channel for A/D sampling. The controller integrates the calculation and conversion parameters of the initial sampling values of various sensors. The parameters include the sensor's range, signal type, etc., but when the sensor is damaged and needs to be replaced, the calculation parameters in the controller must also be adjusted accordingly. Experiments have shown that the reasonable configuration of various parameters can timely reorganize the control strategy of the entire control system, and can more safely and reliably achieve the optimal net power output of the fuel cell engine.
For example, in the self-shutdown conditions, the temperature of the battery stack, the pressure of hydrogen, the fan current, etc. are all important factors that affect normal operation. Once they exceed the allowable range, the control system will execute the self-shutdown command. When the performance of the battery stack is upgraded, the working range that the battery stack can withstand becomes wider accordingly. At this time, the new self-shutdown conditions can be configured through the host computer to enable the controller to obtain the corresponding configuration upgrade.
Secondary development and upgrade implementation strategy
The host computer transmits the configuration information to the controller. After judging and identifying, the controller classifies and partitions the information and saves it in the EEPROM of the soft configuration module. Then the DSP main program calls it from the classified fixed address in the EEPROM. When the host computer configures the upgrade information, it is equivalent to changing the storage order or size of the data in the EEPROM. The EEPROM space used in this system is 64kB, and each page of data storage area has 32 bytes (0x0000-0x0031), which can store 256 pages (0x0000-0xFF00), and each page can store one configuration information.
(1) Projection model
During the configuration and upgrade process of the controller port, the host configuration terminal and the controller soft configuration module form a mapping model for the collaborative definition of each hardware port (as shown in Figure 4). The so-called mapping model can be abstracted into a function mapping, namely f: x→y, where x and y are two component sets, which can be represented here as the controller hardware port serial number and its actual application function. f is a mapping from x to y, which is variable. The mapping relationship is expressed and saved through EEPROM as a medium. Every time the host computer sends a new port configuration, f changes once, and the new hardware port function also changes accordingly. For example, the original controller's first A/D interface is initially set to "collect the in-stack temperature signal", and the second A/D is set to "collect the out-stack temperature signal". "The first" and "the second" are x in the mapping model, indicating that this is the hardware port serial number on the controller; "in-stack temperature" and "out-stack temperature" are y to be configured by the host computer, indicating the actual application function of the port; and f associates the two, indicating the mapping relationship from x to y. When the host computer swaps the configuration of these two A/D interfaces, f also changes accordingly. The result of the configuration is that the "first channel" A/D port becomes "collecting the stack temperature signal", and the "second channel" A/D port becomes "collecting the stack temperature signal".
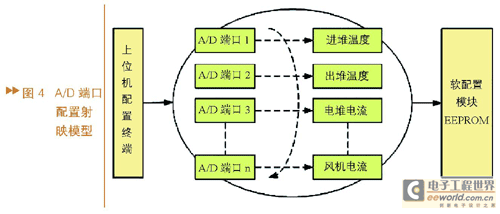
(2) Execution Incentive
After the host computer completes the configuration of the controller, the mapping models of each upgrade information in the soft configuration module are also established accordingly. At this time, the DSP calls each mapping model to the corresponding program module of the main program through the execution engine. The execution engine is a mapping model at a higher level than the mapping model representing the configuration information. Similarly, it can also be abstracted into a function mapping f: x→y. Here, x refers to the upgrade information mapping model in the soft configuration module, such as the A/D port mapping model, I/O port mapping model, self-shutdown condition mapping model, sensor calibration mapping model, etc.; and y is the program module in the main program that executes this part of the upgrade information, and f completes the mapping of the corresponding mapping model to the program execution module.
Multi-performance coordinated control strategy
Another feature of the secondary development control system of the fuel cell engine is the diversity of its control strategies. Traditional control systems usually have only one control strategy for a single control object, which cannot meet the needs of users or function expansion during the control process. Sometimes, in order to meet different control goals, the program has to be re-burned or even the controller has to be redesigned. As shown in Figure 5, this system can easily use a variety of different control strategies to control the fuel cell engine through the strategy library integrated in the upper computer soft switching controller. The available control strategies include the system global normal operation coordination control strategy, the system local normal operation coordination control strategy, and the system local fault operation coordination control strategy. The selection of multiple control strategies largely meets the different needs of the control system, and its operation is simple and the human-computer dialogue is friendly.
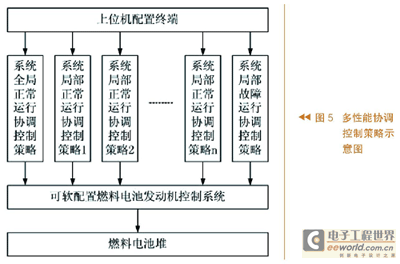
in conclusion
According to the functional requirements of the fuel cell engine secondary development system, this paper designs a soft-configurable controller and a corresponding secondary development upgrade mechanism. The controller realizes the secondary development upgrade of the internal port structure and the control system operating parameters. This paper also proposes a multi-performance coordinated control strategy for the fuel cell engine control system and conducts a preliminary exploration of its application in the control system. Practice shows that the control system operates stably and reliably, and obtains good control effects.
Previous article:Study on the safety performance of electric vehicle lithium battery during combustion
Next article:Hybrid power is the general direction. Analysis of Honda's multiple new technologies
- Popular Resources
- Popular amplifiers
- Car key in the left hand, liveness detection radar in the right hand, UWB is imperative for cars!
- After a decade of rapid development, domestic CIS has entered the market
- Aegis Dagger Battery + Thor EM-i Super Hybrid, Geely New Energy has thrown out two "king bombs"
- A brief discussion on functional safety - fault, error, and failure
- In the smart car 2.0 cycle, these core industry chains are facing major opportunities!
- The United States and Japan are developing new batteries. CATL faces challenges? How should China's new energy battery industry respond?
- Murata launches high-precision 6-axis inertial sensor for automobiles
- Ford patents pre-charge alarm to help save costs and respond to emergencies
- New real-time microcontroller system from Texas Instruments enables smarter processing in automotive and industrial applications
- Innolux's intelligent steer-by-wire solution makes cars smarter and safer
- 8051 MCU - Parity Check
- How to efficiently balance the sensitivity of tactile sensing interfaces
- What should I do if the servo motor shakes? What causes the servo motor to shake quickly?
- 【Brushless Motor】Analysis of three-phase BLDC motor and sharing of two popular development boards
- Midea Industrial Technology's subsidiaries Clou Electronics and Hekang New Energy jointly appeared at the Munich Battery Energy Storage Exhibition and Solar Energy Exhibition
- Guoxin Sichen | Application of ferroelectric memory PB85RS2MC in power battery management, with a capacity of 2M
- Analysis of common faults of frequency converter
- In a head-on competition with Qualcomm, what kind of cockpit products has Intel come up with?
- Dalian Rongke's all-vanadium liquid flow battery energy storage equipment industrialization project has entered the sprint stage before production
- Allegro MicroSystems Introduces Advanced Magnetic and Inductive Position Sensing Solutions at Electronica 2024
- Car key in the left hand, liveness detection radar in the right hand, UWB is imperative for cars!
- After a decade of rapid development, domestic CIS has entered the market
- Aegis Dagger Battery + Thor EM-i Super Hybrid, Geely New Energy has thrown out two "king bombs"
- A brief discussion on functional safety - fault, error, and failure
- In the smart car 2.0 cycle, these core industry chains are facing major opportunities!
- Rambus Launches Industry's First HBM 4 Controller IP: What Are the Technical Details Behind It?
- The United States and Japan are developing new batteries. CATL faces challenges? How should China's new energy battery industry respond?
- Murata launches high-precision 6-axis inertial sensor for automobiles
- Ford patents pre-charge alarm to help save costs and respond to emergencies
- MSP430F5529 RCT official routine
- Has anyone used Renesas' RH850 MCU?
- The second day of the journey ~ Shenzhen ~ Jiangmen
- [Speech and vision module based on ESP32S3] First version of schematic diagram and circuit design
- Share MSP430 serial port receiving control LED
- What is the *.axf file in MDK?
- Today's live broadcast: Third-generation TI C2000 new features resource update
- Xunwei-iMX6ULL development board-transplant mjpg-streamer to achieve remote monitoring
- Can you tell me the steps to construct a distance 3 Hamming code?
- CC3200-LAUNCHXL development board experience sharing - CC3200 Getting Started - cugxiao