Project name: A_Based on the process of debugging CAN communication products with Letuo oscilloscope.
This post is based on the last unboxing. It introduces a tuning capacitor to adjust the oscilloscope probe, which will affect the acquisition of the oscilloscope signal waveform. Let's analyze the basic principle:
Figure a above is the direct connection mode, which is equivalent to directly connecting the signal to be tested and the oscilloscope probe with two wires.
Figure b above is the oscilloscope probe we most commonly use, that is, a passive probe. There are attenuation resistors and input equivalent capacitors inside the probe. The common bandwidth is below 500MHz, and the OSC482M model oscilloscope is equipped with a P2060 oscilloscope probe. The detailed specifications are as follows: The
third column: 60MHz gear (10x), the surface of the probe has an effective bandwidth of 60MHz, and using it beyond this range will cause more measurement deviations. In addition, the rise time is 5.8ns, the input capacitance: 1x gear is 70-120pf, 10x gear is 14-18pf, and the compensable capacitance range is: 15-45pf. The input resistance is 1MHE 10M ohm.
There are also active probes, which require power supply and have op amp circuits inside. There are also differential probes, current probes, etc.
Next, let's look at the hardware parameters of this model of oscilloscope:
Vertical resolution: 8-13 bits
, that is, the ADC device bit number of the oscilloscope is 8 bits. The resolution of the oscilloscope is generally determined by the hardware device, either 8 bits, 10 bits, 12 bits or 14 bits. Here the manufacturer has written a range value, and it is possible that a 14-bit ADC device is used. In actual use, the low-bit data can be removed and converted to a lower bit number.
If the measurement range of the oscilloscope is ±5 V, and the peak-to-peak value is 10V, it means that the minimum voltage that the oscilloscope can resolve is 10V/256=39.06mV. So choose the smallest possible measurement range to get more accurate measurement results. The minimum voltage that can be resolved with a measurement range of ±1V and 8-bit resolution is 7.813mV. But please note that the signal peak value needs to be considered.
Maximum sampling rate: 50M
The sampling rate unit is MS/s (Megasamples per second) or GS/s (Gigasamples per second). If two channels are used at the same time, the maximum sampling rate is halved.
Are you familiar with Nyquist's theorem? It is easy to assume that the sampling rate is only twice the bandwidth of the signal to be measured.
But in reality, this is not possible. The distortion is serious. Generally, the sampling rate needs to be increased by 3-5 times to minimize the distortion.
As shown in the figure below: Let's try sampling an 8MHz crystal oscillation waveform:
You can see that the current sampling rate of 50M is marked in the upper right corner, which has reached the nominal limit of the oscilloscope, 8Bit per bit.
It can be seen that the oscilloscope can still restore the sine wave well, and the automatic measurement below is also very accurate. There is no need to manually adjust the cursor and then measure.
Bandwidth (-3dB): 20MHz
bandwidth means inputting a sine wave, keeping the amplitude unchanged, and increasing the signal frequency. When the signal displayed on the oscilloscope is 70.7% of the actual signal amplitude (i.e. 3dB attenuation), the corresponding frequency is equal to the oscilloscope bandwidth. However, we often measure square waves or digital signals. The most commonly used principle is to choose an oscilloscope with a high signal frequency of 5 times.
So the oscilloscope here can probably accurately measure 4MHz signals. The higher the signal frequency, the more serious the distortion.
Input sensitivity: 10mV/grid-2v/grid, that is, the smallest unit of each grid of the oscilloscope.
Input range (1x): +-100mV - +-5V and other 7 fixed ranges.
Time base: 50ns - 25s/grid, that is, the smallest unit of horizontal axis time.
Storage depth: 512B - 62MB, storage depth = sampling rate * sampling time, that is, how many samples can be stored.
Next, let's actually test it on the host computer interface:
Dual-channel test 1KHz square wave:
Here, adjust the adjustment capacitor on the probe and find that the waveform changes (A signal is undercompensated and B signal is overcompensated). Note that you should use a plastic screwdriver. Metal will affect the capacitor with a very small capacitance, resulting in inaccurate adjustment.
Then adjust the PWM signal frequency to 10KHz, and find that the compensation effect of the probe is weakened. This is the sampling rate problem mentioned earlier.
Let's amplify the signal and see:
we can see the triangle wave. In fact, this is the fluctuation of the ADC sampling value. You can see a few mV change in the upper and lower bits, but this does not affect our observation and measurement of conventional basic signals. Because we usually measure low-speed signals and do not pay attention to the rising edge speed of the signal. Generally, we need to pay attention to the changing trend of the waveform and the logical function.
Next, let's talk about the difference between AC and DC coupling. In fact, the most important thing is that DC is directly connected, while AC is separated by capacitors, that is, what we measure in AC is the AC signal, and the DC signal is filtered. Therefore, the most common application of AC is to measure power supply ripple.
However, the oscilloscope probe is not equipped with an AC spring, so we will not do measurement signal analysis here, because the ground clip will introduce more noise signals, resulting in inaccurate measurement and no test significance.
Why is this? This involves the field of high-frequency signals. As we have learned about high-frequency electronics, we know that the higher the frequency of the signal, the easier it is to generate EMC, and the longer the signal return path, the greater the noise. This is why high-frequency circuits require multiple grounding points. The power supply ripple contains mostly high-frequency components, so we will not do test analysis here.
Common signal capture: When we actually use an oscilloscope, it seems that the most common thing we do is to connect it to see the waveform. Hey, is the signal pulled up, is it pulled down, how many V? How does it change?
However, if you use a trigger function well, you can make waveform capture more efficient. Here we will focus on how to trigger the waveform capture for this oscilloscope.
As shown in the figure above, set the rising edge trigger, select channel A, click single trigger, drag T to set the trigger level threshold, and the capture will be triggered as long as there is a signal that exceeds the threshold from low to high. In this way, you don’t have to keep looking at the waveform.
Here is another FFT picture:
FFT is a fast algorithm for discrete Fourier transform, which can transform a signal into the frequency domain. It is difficult to see the characteristics of some signals in the time domain, but if they are transformed into the frequency domain, it is easy to see the characteristics. This is why many signal analyses use fft transforms. In addition, FFT can extract the spectrum of a signal, which is also often used in spectrum analysis.
So you can see the performance of the signal in the frequency domain below the above figure. The horizontal axis is frequency, and the vertical axis is amplitude. The first circle indicates that the signal has the strongest energy at 8MHz, and here you can see how much the frequency point where the energy peak is offset, that is, the frequency deviation. How about it? Doesn't it feel very powerful? The circle on the lower right shows that there is energy at 2 times the frequency, but it is very weak. But it can also be measured.
Summary:
1. The oscilloscope interface has rich basic functions, and the measurement bandwidth and sampling rate meet the common signal measurement needs.
2. It contains an adjustable signal source output, which is convenient for experimental testing.
3. The AC/DC function can also meet conventional tests, especially the FFT function, which can further analyze the measured signal.
The next issue will conduct an in-depth practical exercise of the oscilloscope: measurement and protocol analysis based on CAN communication.
Previous article:[Free trial of Letuo USB oscilloscope] Comparison test of Letuo USB oscilloscope
Next article:[Free trial of Letuo USB oscilloscope] Complementary PWM signal measurement with dead zone
Recommended ReadingLatest update time:2024-11-16 13:34
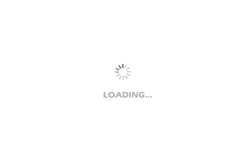
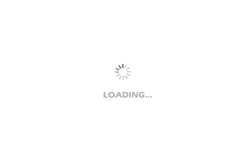
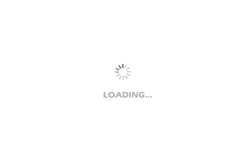
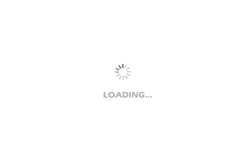
- Keysight Technologies Helps Samsung Electronics Successfully Validate FiRa® 2.0 Safe Distance Measurement Test Case
- From probes to power supplies, Tektronix is leading the way in comprehensive innovation in power electronics testing
- Seizing the Opportunities in the Chinese Application Market: NI's Challenges and Answers
- Tektronix Launches Breakthrough Power Measurement Tools to Accelerate Innovation as Global Electrification Accelerates
- Not all oscilloscopes are created equal: Why ADCs and low noise floor matter
- Enable TekHSI high-speed interface function to accelerate the remote transmission of waveform data
- How to measure the quality of soft start thyristor
- How to use a multimeter to judge whether a soft starter is good or bad
- What are the advantages and disadvantages of non-contact temperature sensors?
- Innolux's intelligent steer-by-wire solution makes cars smarter and safer
- 8051 MCU - Parity Check
- How to efficiently balance the sensitivity of tactile sensing interfaces
- What should I do if the servo motor shakes? What causes the servo motor to shake quickly?
- 【Brushless Motor】Analysis of three-phase BLDC motor and sharing of two popular development boards
- Midea Industrial Technology's subsidiaries Clou Electronics and Hekang New Energy jointly appeared at the Munich Battery Energy Storage Exhibition and Solar Energy Exhibition
- Guoxin Sichen | Application of ferroelectric memory PB85RS2MC in power battery management, with a capacity of 2M
- Analysis of common faults of frequency converter
- In a head-on competition with Qualcomm, what kind of cockpit products has Intel come up with?
- Dalian Rongke's all-vanadium liquid flow battery energy storage equipment industrialization project has entered the sprint stage before production
- Allegro MicroSystems Introduces Advanced Magnetic and Inductive Position Sensing Solutions at Electronica 2024
- Car key in the left hand, liveness detection radar in the right hand, UWB is imperative for cars!
- After a decade of rapid development, domestic CIS has entered the market
- Aegis Dagger Battery + Thor EM-i Super Hybrid, Geely New Energy has thrown out two "king bombs"
- A brief discussion on functional safety - fault, error, and failure
- In the smart car 2.0 cycle, these core industry chains are facing major opportunities!
- The United States and Japan are developing new batteries. CATL faces challenges? How should China's new energy battery industry respond?
- Murata launches high-precision 6-axis inertial sensor for automobiles
- Ford patents pre-charge alarm to help save costs and respond to emergencies
- New real-time microcontroller system from Texas Instruments enables smarter processing in automotive and industrial applications
- Pingtouge RISC-V Low Power Board-RVB2601 Development Board Quick Start Guide
- [Ateli Development Board AT32F421 Review] -1
- Analyze the faults in the resistor parallel circuit
- Today's live broadcast: New opportunities in the UWB market
- What is the principle of this power supply rectification method and what are its advantages?
- Four-level gain amplifier
- We have officially resumed work. Have all the measures been implemented?
- Free application: Beneng cost-effective ATSAMD51 evaluation board (evaluation invitation coupons available)
- MSP430:AD10
- Infineon Position2Go Development Kit Review——by landeng1986