When developing a test system, you must be mindful of the cost and time required to build it. A poorly planned test system can quickly add up and cause frustrating delays. In this article, we'll introduce you to new trends, such as using LAN as system I/O. You'll also discover new ways to evaluate and select system hardware and software. The new concepts explored in this article can help you enhance your existing and future test system designs.
Electronic Functional Test
Let's look at the testing requirements throughout the product lifecycle and define an architecture that accelerates system development. For functional testing, we offer a number of solutions, with the choice of a custom system developed to your specifications or a pre-configured platform to ease the burden of developing a test system.
Testing in the Product Lifecycle
Let's look at our test system portfolio and how it relates to the product lifecycle. We'll start by focusing on the test requirements of three phases: design validation, design verification, and product manufacturing. We'll explore some of the ways Agilent has translated the requirements of each lifecycle into hardware, software, and connectivity tools that provide open connectivity and easy-to-integrate system solutions.
Design validation typically requires the most accurate and advanced signal sources and measurements. Test instruments should have interactive capabilities and full panel controls, and must be able to provide rapid feedback on well-defined tests. This work requires easy connectivity to tools such as Microsoft Excel, but rarely requires extensive programming or automated testing. The
design verification phase also has accuracy requirements, but other aspects become increasingly important. For example, the process of drilling down into the problem mentioned earlier means pushing the design to its limits, which means performing many tests and perhaps some statistical analysis. Some programming is required, so the software must provide easy programming capabilities but still have the versatility to perform any type of analysis. The
main goal of the product manufacturing phase is to reduce costs. Test instruments contribute greatly to providing fast throughput and high reliability. Test instruments with more built-in capabilities can also help reduce costs, but accuracy may be compromised. Less complete product testing (compared to the validation phase) can also help reduce costs because the number of instruments used, system cost, and test time can usually be reduced in this case. In short, various combinations of software and hardware must be used to address the needs of these different applications.
Impact of Hardware Options on Development and Output
During the system design process, the instruments you choose and how you configure the instruments in the system have a great impact on the time it takes to develop the system and finally perform a series of tests.
As you begin to outline the system architecture, use the following sample questions as a starting point:
Do you need greater flexibility to accommodate changing measurement requirements, second-generation product development, or future expansion requirements? Do
you need to combine and reuse unused instruments on hand?
Can an interconnect panel be set up to handle multiple DUTs?
Can the system (or a replica) be shipped to locations with different line voltages?
Answers to questions like these can inspire you to look for ways to improve the reuse of the system architecture from a broader and longer-term perspective.
Benefits of Using Open Standards
The foundation of our test approach is the widespread adoption of PC industry standards, which are ubiquitous, reliable, and economical. Here are the three main parts of our test approach:
Standard software - We support a wide range of standard PC software, which means you can work in your preferred environment, such as spreadsheets, text programming, or visual programming. Standard
I/O - The right I/O helps you tune your system to the best fit for the primary application: GPIB for stand-alone systems with legacy equipment; USB for simple stand-alone systems; LAN for complex systems that must communicate with the rest of the organization.
System Instruments - Stand-alone instruments optimized for use in systems, these instruments can help you address all of your test needs from R&D to manufacturing without changing hardware.
Using LAN
In the past, GPIB (or HP-IB) was the default choice for instrument I/O. Like software, the best interface to work with is also related to the product life cycle. For manufacturing, LAN interfaces provide the best system flexibility and cross-organizational connectivity. Our newest line of power supplies, the Agilent N5700 and N6700, are available with three types of I/O: GPIB, USB, and LAN. You just use the interface that has the right advantages and capabilities for your system.
LXI is the future of test
A consortium of well-known test and measurement companies and users announced a new standard for test systems, LXI (LAN eXtensions for Instruments), on September 26, 2005. Founded a year ago, the LXI Consortium has set out to increase system speed, reduce system cost, reduce system size, reduce system setup time, and enhance software applications. Using Ethernet (IEEE 802.3) as the primary communication medium, they attempted to leverage existing achievements in the computer industry. Directly leveraging some existing Ethernet standards, Internet tools, LAN protocols, IEC physical dimensions, and IVI drivers, they saw an opportunity to move toward faster I/O, remove card slots and expensive I/O wiring, and properly utilize software. The consortium found that they could develop a more durable architecture than one based on rapidly changing computer backplanes. Developing an architecture based on reliable industry standards allows them to leverage existing achievements and provide a durable solution for test system developers. The
LXI standard includes the following:
- The three categories of LXI (A, B, and C)
- entity
- LAN specifications
- LAN Configuration
- LAN Search
- Program interface
- Web Interface
- Inter-module communication
- LAN Trigger
- Hardware trigger
- safety
- Documentation
- Authorization
- Compliance
The LXI standard is centered around four major areas: physical requirements, Ethernet protocol, LXI interface, and LXI triggering.
The three categories of LXI
Category C is the base category of LXI. All categories must meet the above requirements. Category C devices must comply with the physical requirements, Ethernet protocol, and LXI interface standards.
Category B complies with all the requirements of Category C, and also adds LAN triggering and IEEE 1588 timing synchronization protocol. Category A complies with all the requirements of Category C and B, and adds a hardware trigger bus. [page]
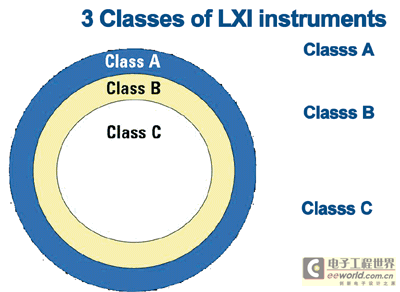
LXI's physical form
LXI is designed to provide maximum flexibility. The standard provides panels for benchtop instruments; modules without front interfaces that can be easily installed in a rack; or small devices that can be placed in a fixture, hung on a wall, or connected to a device. Unlike VXI and PXI, which have specific restrictions on module size, LXI can be sized according to application requirements.
For instruments to be installed in a test rack, the LXI specification recommends that they must conform to the IEC specification for full or half rack width and a number of rack units high (one unit = 1.75"). The IEC specification covers half-rack width instruments of 2RU (rack units) or higher. The new 1RU, half-rack width modules defined by the LXI Consortium are an attractive size for test system builders. These modules provide high-quality instruments with sufficient printed circuit board space while still fitting smoothly into a standard rack without the need for card slots.
LXI modules differ from VXI and PXI in that they are self-contained. These modules have their own power supply, cooling system, triggering, EIM isolation, and Ethernet communication. If AC power is required, they implement global power (100Vac-240Vac and 47-66Hz), and if DC power is required, they also have 48V isolated power. Power over Ethernet is also an option. LXI devices must have a LAN port and comply with IEEE 802.3 Ethernet rules.
Ethernet Requirements for LXI
All LXI devices must implement the IEEE 802.3 Ethernet standard interface (RJ-45 connectors are recommended). They must use at least TCP/IP version 4 and support IP TCP and UDP messages. The LXI standard recommends using 10-megabit Ethernet (although 10 and 100-megabit LANs are also possible).
For addressing, each LXI device must have a fixed MAC address and an IP address that can be changed via DHCP, AutoIP, or ManualIP. LXI devices support dynamic host name registration, where the IP address of the device is mapped from the network host to a name that is easier for the user to remember. Addressing rules allow LXI instruments to coexist on the network without much effort.
Communication Interface for LXI Instruments
The LXI standard specifies two methods for communicating with LXI devices - programmatically using an IVI driver, or interactively using a standard W3C web browser.
In terms of programming, LXI instruments must support IVI drivers (IVI-COM or IVI-C). IVI-COM drivers can handle all the latest programming languages (such as Microsoft Suite), while IVI-C drivers can handle the older ANSI-C language supported by LabWindows CVI. The LXI Alliance believes that supporting a standard driver interface will help reduce the programming required to use LXI instruments.
In terms of conversational features, LXI instruments must provide HTML pages that can be viewed using any standard web browser. Figure 4 shows the homepage and important information of the Agilent N6700B modular power supply.
LXI devices must also support the following user configurations through the instrument's web page.
-
Host Name
-
illustrate
-
TCP/IP configuration, including IP address, subnet, default gateway, and DNS server
-
Status and Error Conditions (Suggested Items)
-
Web page password protection function (recommended item)
The following figure is an example of an Agilent 34980A switch/measurement matrix plug-in module, showing how the user can click the mouse to turn on/off switching operations through a web page. Note: Instrument monitoring and control are optional features, not required by the LXI standard.
Previous article:Designing a new generation of automated test systems
Next article:Aircraft engine test system solutions
Recommended ReadingLatest update time:2024-11-17 02:51
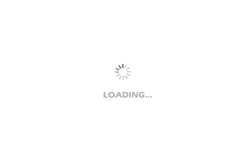
- Popular Resources
- Popular amplifiers
- Keysight Technologies Helps Samsung Electronics Successfully Validate FiRa® 2.0 Safe Distance Measurement Test Case
- From probes to power supplies, Tektronix is leading the way in comprehensive innovation in power electronics testing
- Seizing the Opportunities in the Chinese Application Market: NI's Challenges and Answers
- Tektronix Launches Breakthrough Power Measurement Tools to Accelerate Innovation as Global Electrification Accelerates
- Not all oscilloscopes are created equal: Why ADCs and low noise floor matter
- Enable TekHSI high-speed interface function to accelerate the remote transmission of waveform data
- How to measure the quality of soft start thyristor
- How to use a multimeter to judge whether a soft starter is good or bad
- What are the advantages and disadvantages of non-contact temperature sensors?
- Innolux's intelligent steer-by-wire solution makes cars smarter and safer
- 8051 MCU - Parity Check
- How to efficiently balance the sensitivity of tactile sensing interfaces
- What should I do if the servo motor shakes? What causes the servo motor to shake quickly?
- 【Brushless Motor】Analysis of three-phase BLDC motor and sharing of two popular development boards
- Midea Industrial Technology's subsidiaries Clou Electronics and Hekang New Energy jointly appeared at the Munich Battery Energy Storage Exhibition and Solar Energy Exhibition
- Guoxin Sichen | Application of ferroelectric memory PB85RS2MC in power battery management, with a capacity of 2M
- Analysis of common faults of frequency converter
- In a head-on competition with Qualcomm, what kind of cockpit products has Intel come up with?
- Dalian Rongke's all-vanadium liquid flow battery energy storage equipment industrialization project has entered the sprint stage before production
- Allegro MicroSystems Introduces Advanced Magnetic and Inductive Position Sensing Solutions at Electronica 2024
- Car key in the left hand, liveness detection radar in the right hand, UWB is imperative for cars!
- After a decade of rapid development, domestic CIS has entered the market
- Aegis Dagger Battery + Thor EM-i Super Hybrid, Geely New Energy has thrown out two "king bombs"
- A brief discussion on functional safety - fault, error, and failure
- In the smart car 2.0 cycle, these core industry chains are facing major opportunities!
- Rambus Launches Industry's First HBM 4 Controller IP: What Are the Technical Details Behind It?
- The United States and Japan are developing new batteries. CATL faces challenges? How should China's new energy battery industry respond?
- Murata launches high-precision 6-axis inertial sensor for automobiles
- Ford patents pre-charge alarm to help save costs and respond to emergencies
- Nexperia ESD Webinar Invitation
- What is the four-wire resistance measurement? What are the advantages?
- msp430 contains ADC12 module program implementation
- This circuit for detecting mobile phones is no longer usable, right?
- STM32 stepper motor trapezoidal acceleration and deceleration program
- What is the way to distinguish whether series resonance is good or bad?
- Improved Snowy Night Christmas Tree Program
- National Geographic China and "Beautiful China - China's Most Beautiful Places Selection Event"
- 2020 is about to pass, and the problems brought by these new technologies are still there
- [2022 Digi-Key Innovation Design Competition] Material Unboxing - ESP32-S2-KALUGA-1