1. Introduction to Enlafu Liquid Level Meter
1. Basic principles of measurement
The measuring principle of the servo level gauge is: the force sensor detects the change in the buoyancy on the float. The float is suspended by a strong and soft measuring wire wrapped around a grooved measuring drum. The drum is connected to the stepper motor through magnetic coupling. The actual weight of the float is measured by the force sensor . The float weight measured by the force sensor is compared with the pre-set float weight. If there is a deviation between the measured value and the set value, the advanced software control module will adjust the position of the stepper motor to move the float down or up, and finally the servo motor will stop rotating when the forces are balanced.
1.1 Liquid level measurement
The change of product level causes the float immersion depth to change, and the buoyancy of the float also changes. The change of buoyancy is detected by the force sensor. The deviation between the measured value and the set value causes the stepper motor position to change, raising and lowering the position of the float until the measured value and the set value are equal.
To avoid vibration, the software can also adjust the hysteresis and integration time. This can get a more stable and accurate average level. The stepper motor moves the float up and down about 10mm per revolution. Each revolution is divided into 200 steps, so each step is equivalent to 0.05mm.
This directly determines the resolution of the motor. At the same time, the position of the stepper motor is constantly detected. This is achieved by a unique code disc mounted on the motor shaft.
1.2 Interface between the two products
Measuring the interface between two products is accomplished by sending commands to the level gauge. When your set point (a float minus a portion of the buoyancy) is equal to the weight of the float at the average of the buoyancy of the two liquids, the instrument can detect the position of the interface. This is superior to floats and differential pressure (floats and differential pressures are greatly affected by temperature, pressure and composition interference).
1.3 Relative density
To measure relative density, the float is stopped at a specific location and the weight of the float is measured. Knowing the volume of the float, its weight in air, and the actual weight measured, the relative density of the product at that specific location can be calculated. Software to measure density is an optional feature.
1.4 Other functions
It can have high and low level alarm output of dry node, can communicate with pressure transmitter with hart function, and transmit pressure signal to control room through bus for centralized display.
MRT and 862 MIR temperature detection boards can detect temperature and can also detect multi-point average temperature. They can output 4~20mA intrinsically safe signals to display liquid level values on the ground meter.
2. Installation
Once the meter is selected , proper installation is the key to its smooth operation.
The flange on which the level gauge is mounted should be kept horizontal. The 854 ATG can be connected to flanges of different types using adapters and calibration connectors. It is necessary to confirm whether the maximum pressure of the adapter and calibration connector is compatible with the maximum pressure of the installation site.
For maintenance purposes, when the 854 ATG is installed on a sealed tank, a suitable ball valve can be installed between the tank and the 854ATG. The maximum opening of the ball valve must ensure that the float can pass smoothly.
Install on the tank in the following two ways
2.1 Tanks without guide posts: 854ATG installation orientation on the tank
2.2 When installing on the liquid stabilizing pipe and guide tank, it can be installed in any direction.
3. Debugging:
The parameters of the 854ATG level meter are in the form of projects. Before using a new meter, you only need to enter the following parameters:
TT = Tank top position
The format is in accordance with the LD directive. The tank top position must be set taking into account the compensation of the wire weight. The tank top position value entered now must be replaced by the highest position where the float stops after the liquid level is calibrated.
MH = Motor High Limit Position format as specified in command LD. This position is the highest position the float is allowed to reach during normal operation.
MZ = The highest position of the float is set in the format specified by instruction LD. Instruction MZ sets the highest position the float reaches when LT is executed.
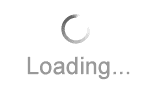
ML = Motor lower limit position format as specified in instruction LD. This position is the lowest position the float is allowed to reach during normal operation. [page]
DC Drum circumference standard floating point format; unit: meter. Check that the preset drum circumference is consistent with the circumference engraved on the installed drum. If incorrect, enter the value engraved on the drum.
DW Float Weight
Standard floating point format; unit: grams. The standard float weight is 223g. If you are using a density float, you must compare the weight engraved on the float with the initial value in the command. If they are different, modify the value in the command to the value engraved on the float.
DA Float cross-sectional area in standard floating point format; units:
cm2. Check that the preset value is consistent with the float cross-sectional area used. For the values of various float cross-sectional areas, see Appendix B. If incorrect, enter the correct float area value.
S1 Setpoint Standard floating point format; unit: grams. If a standard float is installed, the setting value for interface 1 (liquid level) should be 208 g. If a density float is used,
S1 should be set to: (DW - 15).
TA= Two-digit correspondence address.
The communication address defines the address of the level meter on the Enraf two-wire communication bus. Each level meter has a unique address, so the TA must be set to a different value. When connected to the 858 CIU, please note that the 858
CIU has three buses, and the addresses are assigned as follows:
TI= Tank ID 6 characters. As a label; the name of the tank can be used as the tank ID (no spaces allowed).
TS = four-digit communication speed; 1200 (default) or 2400. Unit: baud
GT= Gauge Type One character. Describes the type of level gauge. 854 ATG, GT=B.
2. MODBUS data output parameters of the Enlafu level meter in this project:
1. The slave Enlafu level meter provides each tank level data to the master host computer through the RS485 conversion module. The red line is A, the black line is B, and the white line is GND.
2. The transmission protocol is MODBUS.
3. Communication port settings: RTU address: 01 Baud rate: 9600, Data bit: 8 bits, Stop bit: 1
Parity None: None, Flow Control None
4. Output data: 41201-41206 outputs the liquid level values of tanks 2301, 2302, 2303, 3001, 3002, and 3003 in sequence.
16-bit unsigned integer data, unit: millimeter, no decimal place, negative liquid level is not supported. When there is no material in the tank, the MODBUS output is 0.
3. Software and hardware configuration steps of HPCS3000 in this project:
1. The main station uses USB-RS485 module to receive RS485 signals from the site and display the liquid level data of each tank on this computer; (the encryption lock needs to support this communication protocol);
1.1. Install the USB-RS485 module and driver, and confirm the occupied port number;
1.2. Install the encryption lock and connect the RS485 cable.
2. Software installation and configuration:
2.1. Copy the Standard_Umodbus folder to D:Huawen_DCSIO
Servers (the installation directory of Huawen_DCS);
2.2. Open the Huawen_DCS configuration software and enter the engineering development state: open the real-time database IO device driver
The configuration of the new standard MODBUS modbus (RTU serial port) device is as follows:
2.3 Enter the database configuration and configure the measurement point connection according to the parameters provided by the field equipment as shown below: (Output data: 41201-41206 Sequential output
Output the liquid level values of tanks 2301, 2302, 2303, 3001, 3002, and 3003.
16-bit unsigned integer data, unit: millimeter, negative liquid level is not supported. When there is no material in the tank, the MODBUS output is 0.)
After making changes, save and exit, and run the process screen. At this point, the spherical tank liquid level data is displayed on the upper screen.
Previous article:Building a new type of instrument: software-defined instrumentation
Next article:Datapaq helps Wimbledon stay safe
- Keysight Technologies Helps Samsung Electronics Successfully Validate FiRa® 2.0 Safe Distance Measurement Test Case
- From probes to power supplies, Tektronix is leading the way in comprehensive innovation in power electronics testing
- Seizing the Opportunities in the Chinese Application Market: NI's Challenges and Answers
- Tektronix Launches Breakthrough Power Measurement Tools to Accelerate Innovation as Global Electrification Accelerates
- Not all oscilloscopes are created equal: Why ADCs and low noise floor matter
- Enable TekHSI high-speed interface function to accelerate the remote transmission of waveform data
- How to measure the quality of soft start thyristor
- How to use a multimeter to judge whether a soft starter is good or bad
- What are the advantages and disadvantages of non-contact temperature sensors?
- Innolux's intelligent steer-by-wire solution makes cars smarter and safer
- 8051 MCU - Parity Check
- How to efficiently balance the sensitivity of tactile sensing interfaces
- What should I do if the servo motor shakes? What causes the servo motor to shake quickly?
- 【Brushless Motor】Analysis of three-phase BLDC motor and sharing of two popular development boards
- Midea Industrial Technology's subsidiaries Clou Electronics and Hekang New Energy jointly appeared at the Munich Battery Energy Storage Exhibition and Solar Energy Exhibition
- Guoxin Sichen | Application of ferroelectric memory PB85RS2MC in power battery management, with a capacity of 2M
- Analysis of common faults of frequency converter
- In a head-on competition with Qualcomm, what kind of cockpit products has Intel come up with?
- Dalian Rongke's all-vanadium liquid flow battery energy storage equipment industrialization project has entered the sprint stage before production
- Allegro MicroSystems Introduces Advanced Magnetic and Inductive Position Sensing Solutions at Electronica 2024
- Car key in the left hand, liveness detection radar in the right hand, UWB is imperative for cars!
- After a decade of rapid development, domestic CIS has entered the market
- Aegis Dagger Battery + Thor EM-i Super Hybrid, Geely New Energy has thrown out two "king bombs"
- A brief discussion on functional safety - fault, error, and failure
- In the smart car 2.0 cycle, these core industry chains are facing major opportunities!
- Rambus Launches Industry's First HBM 4 Controller IP: What Are the Technical Details Behind It?
- The United States and Japan are developing new batteries. CATL faces challenges? How should China's new energy battery industry respond?
- Murata launches high-precision 6-axis inertial sensor for automobiles
- Ford patents pre-charge alarm to help save costs and respond to emergencies
- [HC32F460 Development Board Review] NO.2 Familiarity with the development process and different peripheral functions
- Classification of RFID readers and their advantages
- [Repost] Correctly select low noise amplifier
- NTC thermistor driver for MicroPython
- How does Cyclone2's ep2c8 provide clock to external ADC?
- Comparison of Autoliv 2nd and 3rd generation night vision cameras
- If I use a battery to power a DCDC circuit, how can I be sure that the battery has enough power?
- Standard USB keyboard data packet
- 【Small home weather station】+ Hardware design, board proofing
- Forever power_A tiny device that turns your universal power bank into an uninterruptible power supply