1. Proposal of reconfigurable measurement and control system
The measurement and control system generally refers to a system based on computers to realize data acquisition and control. The measurement and control system is widely used in industrial field control, home digital management, communication and network, and is constantly moving towards low cost, high speed, high performance, intelligence and openness. However, modern measurement and control systems still face many problems in design and application:
① The design speed is difficult to adapt to the rapid changes in product upgrades. Generally, the design of measurement and control systems is aimed at a specific task, and the cycle from design to commissioning is at least 1 to 2 years, or even as long as 4 to 5 years. Therefore, the advanced solutions in the design stage are often outdated at the beginning of commissioning.
② The design solution has fixed functions and poor versatility, making it difficult to meet the changing needs of users at different levels. The measurement and control system is designed for specific users, with different configurations and poor versatility. How to meet the needs of different users at different levels, especially the needs of multi-tasking users, is a major problem.
③The application of virtual instrument technology makes software reconstruction possible, but it is still difficult to achieve hardware reconstruction and "plug and play" effects.
Therefore, studying a measurement and control system that is reconfigurable in both software and hardware, open and universal, has a high application value for realizing the rapid and open design of the measurement and control system and reducing the user's cost. Based on the universal structural characteristics of modern measurement and control systems and the development of reconfigurable field programmable gate array (FPGA) technology, this paper proposes a design concept of a reconfigurable measurement and control system ( RMS ) and gives its application example.
1.1 Structural model and multi-task characteristics of measurement and control system
With the continuous in-depth integration of computer hardware and software technology and measurement and control technology, modern measurement and control systems have shown universal characteristics in structure, namely the "system front end (information data acquisition (A/D)) + digital signal processing ( DSP ) + system back end (output (D/A) and display)" model. This clear and universal structural model creates conditions for users to realize the self-organization, redefinition and reuse of measurement and control systems.
Modern measurement and control systems generally have multi-tasking capabilities, that is, the system needs to complete several separate spatially related (parallel) tasks at the same time, or complete several time-related (sequential) tasks in sequence. The traditional multi-tasking design method is to achieve multi-tasking by increasing the amount of hardware or increasing the control function of the software. On the one hand, it increases the difficulty and cost of engineering design and debugging, making the application system increasingly large and complex; on the other hand, the complexity of circuits and software brings many troubles to users. The emergence of reconfigurable technology provides a new idea for solving multi-tasking problems.
1.2 Reconfigurable Technology and Reconfigurable Devices
Reconfigurable technology has been a hot topic in information technology research since the beginning of the 21st century. It is a computer technology that can reorganize its own resources according to the needs of system function changes, and realize self-optimization and self-generation of software and hardware structures. Reconfigurable technology includes two aspects: hardware reconstruction and software reconstruction. Software reconstruction according to the needs of application tasks is already common in traditional system design, while hardware reconstruction (referring to changes in the hardware logical structure of the system) is impossible to achieve in traditional system design. The widespread application of reconfigurable technology must be based on reconfigurable hardware that provides programmable resources.
With the continuous development of microelectronics technology, programmable logic devices (PLDs) and programmable analog devices (PADs) that appeared at the end of the 20th century provided the hardware foundation for the functional reconstruction of measurement and control systems. Reconfigurable devices mainly include the following:
(1) Reconfigurable logic device FPGA
FPGA's programmable devices are based on SRAM and can be quickly reprogrammed, which is called "field programmable". This feature makes FPGA widely used and becomes a continuous driving force for the development of reconfigurable measurement and control systems. FPGA is an indispensable key device for building reconfigurable measurement and control systems.
(2) Reconfigurable Analog Devices
Programmable analog devices (PADs) are analog integrated circuits with typical functions such as signal conditioning, analog computing, and medium and high frequency applications. Like PLD devices, users can change their internal connections and component parameters through on-site programming and configuration to obtain the required circuit functions. With the corresponding development tools, their design and use can be as convenient, flexible, and fast as PLDs. For example, Lattice's programmable analog chip ispPAC30 contains 4 input instrument amplifiers , 2 independent internal controllable reference sources, and 2 enhanced DACs , providing an analog interface between the system and the measurement and control object, which can be used to connect analog inputs to realize the data acquisition function of the system; using its programmable function, its functions can be reconfigured for different applications. However, compared with programmable logic devices, programmable analog devices came out later, with fewer varieties, and cannot be used as mainstream reconfigurable devices.
(3) Reconfigurable DSP Devices
DSP devices are suitable for occasions with intensive calculations, complex algorithms, outstanding concurrency and real-time requirements, such as consumer products with intelligent logic, biometric information recognition terminals, keyboards with encryption and decryption algorithms, ADSL access, real-time voice compression, virtual reality display, etc. This type of intelligent algorithm generally has a large amount of calculations, especially vector operations, pointers, linear addressing, etc., which are the strengths of DSP processors . However, conventional DSPs do not have hardware reconstruction functions, and the technology that supports hardware reconstruction of DSP devices is still under development and difficult to put into large-scale applications. Of course, DSP function redefinition can be achieved through traditional software reconstruction design, but this is not what we discuss here. A practical method to realize reconfigurable DSP devices is to use FPGA devices to realize reconfigurable DSP functions (such as references). Its essence is to realize the reconstruction of DSP functions based on reconfigurable FPGA devices.
In summary, the field programmable features of FPGA devices have become the key to the application of reconfigurable technology, providing feasibility for the design of reconfigurable measurement and control systems. RMS is to build a system hardware platform with reconfigurable devices, and generate different overload data streams under the control of the software platform to change the hardware structure formed by FPGA to meet different task requirements. Its essence is a hardware-software collaborative design technology.
2 Design of RMS based on FPGA
2.1 Design principles of FPGA-based RMS
The design of a reconfigurable test system should follow the following basic principles:
(1) Interface standardization
In the interface design of the measurement and control system, try to adopt open and standardized system interface standards, such as universal read and write, control bus structure, standard servo drive interface, etc.
(2) Functional Implementation Modularity
The software and hardware design of RMS adopts modular design concept. The modules are divided according to the functions and reasonably allocated to FPGA devices and DSP devices. For the functions of FPGA devices, hardware description language is used for logical description. After functional design, timing simulation , circuit testing, and module packaging, a special measurement and control IP is made for the design platform to call.
(3) System integration and openness
The measurement and control IP developed by the company and the standard IP purchased from other IP suppliers are integrated into a measurement and control system using specialized integrated software. The design can also be changed by cutting and reorganizing different IPs, so as to achieve both functional customization and meet current measurement and control requirements, and openness and adaptability to future functional expansion.
(4) Flexibly select the main controller according to the system scale
As the core of RMS, the reconfigurable main controller is a key device that reflects the different scales and functions of RMS. Its implementation devices and functional modules can be flexibly selected according to the needs of the measurement and control object to achieve a reasonable balance between function and cost. A low-cost FPGA solution can be selected to complete the functional design in the finite state machine (FSM) mode, and static reconstruction can be achieved by downloading in the JTAG passive serial mode for simple and low-speed data acquisition; a high-performance SOPC solution can also be selected to achieve dynamic reconfiguration to meet the needs of high-speed and complex data processing.
(5) Embedded Features
RMS is a typical embedded system with the features of function tailorability, structural redefinition and hardware and software co-design. [page]
2.2 Structure and Design of FPGA-based RMS
RMS can be regarded as a general measurement and control design platform, and its basic hardware structure is shown in Figure 1.
Click to see the original image
The measurement and control system consists of two parts: the main control computer and the relatively independent measurement and control system based on FPGA devices, which are connected through a communication interface. The main control computer mainly realizes the human-computer dialogue function, including the processing and display of test data and the control of the instrument soft panel , which can be realized using virtual instrument technology. The measurement and control system based on FPGA devices includes a data acquisition and output control unit, an FPGA unit and a DSP unit. All three units have reconfigurable functions and are controlled by the main controller unit. The basic function block refers to the power supply, system monitoring module and memory module that are indispensable for computer systems.
2.2.1 Reconfigurable Data Acquisition and Output Control Unit
This unit is directly connected to the measured and controlled object as the forward and backward channels of RMS. The signal conditioning circuit can be designed in a universal form and redefined and adjusted according to the number, range, analog /digital type, filtering parameters, etc. of the measured and controlled objects. For example, a reconfigurable PAD device can be used to directly connect to the analog test object, and the main control computer completes the design, simulation , and testing, and the reconstruction is realized through the main controller unit.
2.2.2 Reconfigurable FPGA Unit and Reconfigurable DSP Unit
The functions of the FPGA unit and the DSP unit can be reasonably divided in advance according to the needs of the actual test object, and the entire process of design, simulation, testing and integration can be completed in the form of IP cores on the host computer. The final configuration data stream file is pre-stored in the corresponding configuration memory (usually SRAM or Flash memory). This static reconstruction method is suitable for general occasions where the real-time requirements for configuration are not too high. SRAM-based FPGA devices and general-purpose DSPs can be selected. If the real-time requirements for configuration switching are high, specific FPGA devices suitable for dynamic configuration can be selected, but the cost is much higher.
2.2.3 Reconfigurable Main Controller
The main controller unit is the key part to realize the reconfigurable function. It is not only the channel for data transmission between the measurement and control system and the main control computer, but also the control center of the data acquisition and output control unit, FPGA unit and DSP unit. In the system reconfiguration mode, it receives the reconfiguration instructions and data from the main control computer, and performs online programming on the configuration memory of FPGA and DSP; in the normal measurement and control mode, the main controller obtains the collected and processed data from FPGA and DSP, and sends it to the main control computer for processing.
The design of the main controller can be reasonably selected according to the system scale. It can use general MCU (such as 51 series single-chip microcomputer) and embedded SoC (such as ARM); it can also be implemented using FPGA devices, such as A1tera's Nios soft processor core based on the SoC method .
2.2.4 Communication Structure
The choice of RMS communication structure is crucial to the system's operating speed, real-time performance and cost.
From the perspective of versatility, the communication structure of RMS can choose different forms according to the needs of the system scale. Large-scale measurement and control systems can use dedicated measurement and control buses (such as GPIB, CPI, CPCI, etc.) to connect to the main control computer in a standardized, modular plug-in card form; small systems can use universal buses (such as RS232, UART, USB, CAN bus) as needed, and selectively add programmable I/O ports, ZigBee 无线通信\'); companyAdEvent.show(this,\'companyAdDiv\',[5,18])"> wireless communication interfaces, TCP/IP protocols, Ethernet interfaces and other communication and network expansion interfaces to meet the needs of wireless communication and network measurement and control function expansion. Regardless of the size and type of interface, they can be designed in the form of IP modules and configured on FPGA devices to meet the needs of different applications.
It is worth noting that the communication structure design of the measurement and control system should not only include the design of the system bus, but also the design of the FPGA on-chip communication structure. Typical reconfigurable FPGA on-chip communication structures usually have two strategies: on-chip bus and on-chip network. Although the on-chip network structure can better reflect the structural parameter requirements, it costs a huge area; while the on-chip bus structure has the advantages of high flexibility, scalability, low design overhead, low bandwidth requirements, and short latency, and has become the first choice for RMS. Considering the configuration needs of FPGA, corresponding JTAG interfaces should be designed in the communication module, main controller module and FPGA device to meet the needs of data flow configuration and online testing.
2.2.5 Software Refactoring
Software reconstruction is a necessary part of the reconstruction of the measurement and control system as a collaborative design of software and hardware. Traditional measurement and control software is often designed for specific measurement and control, objects and hardware resources, which limits the use of measurement and control devices of different models, different manufacturers and different hardware interfaces. In order to realize the software reconstruction of the measurement and control system, the design ideas of traditional measurement and control software should be broken, and the software reuse ideas based on program framework and reusable components should be adopted. As shown in Figure 2, the measurement and control software is divided into two parts: the measurement and control software platform and the measurement and control driver program, and dynamic links are realized between them through the software interface provided by the software platform. The measurement and control software platform mainly realizes the control of the main control computer functions and the data communication between the main control computer and the driver program of the measurement and control system.
The reconfigurability and identifiability of the measurement and control terminal application software includes two aspects: first, the reconfigurability of the measurement and control software platform, that is, the software platforms of different measurement and control applications can recognize the same control instructions and accurately complete the measurement and control tasks assigned by the main control computer; second, the reconfigurability of the measurement and control driver program, that is, the drivers of various types of measurement and control applications can be dynamically linked to the software platform to achieve "hot plugging and unplugging".
There are many options for the reconstruction platform of measurement and control software: it can be a dedicated virtual instrument software based on graphical GUI, such as Labview (the interface with the instrument driver is realized through CLF nodes, and the instrument driver is given in the form of a dynamic link library, which encapsulates all I/O operations related to the instrument into functions, and realizes data input and output by accessing USB or other interface drivers); it can also use a general visual software programming environment, such as VB, VC, etc. For small and simple measurement and control systems, it is recommended to use the graphical and efficient Labview.
3 Implementation of RMS based on CPCI bus
The example given below is an RMS based on the CPCI bus for real-time detection of radar signals. Traditional radar detection requires the development of multiple independent detection cards (such as pulse radar detection cards, continuous wave radar detection cards, IFF signal detection cards, and more than a dozen other devices) and corresponding measurement and control software due to different signal characteristics and processing methods. A general hardware platform is used, consisting of a CPCI industrial control computer and two CPCI reconfigurable hardware circuit boards . FPGA and DSP are designed according to different types of radar signals, and the configuration files are stored in the computer. In actual work, for different radar signals, the corresponding software and hardware configuration files are selected through the application software for dynamic reconfiguration, achieving the effects of miniaturization, generalization, and software and hardware reconfiguration, saving nearly 70% of R&D costs and shortening the development cycle by 50%. Figure 3 is the hardware block diagram of the system.
Click to see the original image
In Figure 3, the core device, the reconfigurable main controller EP2$30, is a channel for data exchange between the control center and the main control computer through the CPCI bus, which is connected to the signal acquisition and control processing output part through the reconfigurable FPGA and DSP devices. Based on the design concept of SOPC, the main controller function is realized by using Altera's NiosII processor IP soft core and peripheral logic programming. The main controller exchanges instructions and data with the CPCI controller through the PCI local bus, and exchanges acquisition and output data with the FPGA and DSP through the custom bus and DSP bus. In the system reconstruction mode, the main controller receives the reconstruction instructions and data of the host through the CPCI controller, and programs the configuration memory of the FPGA and the program memory of the DSP online; at the same time, the FPGA can also be directly loaded online in parallel to complete the hardware reconstruction of the system. In the normal working mode of the system, the main controller transmits the real-time data obtained from the acquisition part to the main control computer through the CPCI bus, or sends it to the DSP for data processing and control output.
For data acquisition modules and control output modules, "reconfigurable" means that their module composition can be tailored according to measurement and control needs. For example, PAD modules, motor speed control modules based on FPGA, stepper motor control modules, etc. can be selected.
Conclusion
Based on the general structural model of the measurement and control system and the reconfigurable functional characteristics of FPGA, this paper proposes a platform-based design concept of RMS based on FPGA devices, which effectively shortens the development cycle and design and application costs for embedded applications, meets the requirements of parallelism, multi-tasking, openness and integration, and achieves a breakthrough in the "only defined and designed by the manufacturer, only used by users" mode and "single task" mode of the measurement and control system. RMS technology has broad application prospects in industrial field control, urban municipal management, intelligent building monitoring, smart home and other fields, and is also worth studying in remote reconstruction and network measurement and control.
Previous article:Design of Ultrasonic Distance Measurement System
Next article:Measuring the leakage resistance of a capacitor using the Model 6487 Picoammeter Source or the Model 6517A Electrometer
Recommended ReadingLatest update time:2024-11-16 21:26
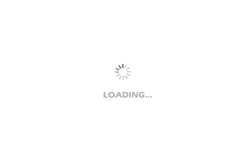
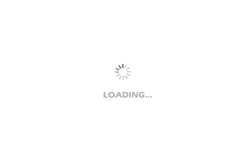
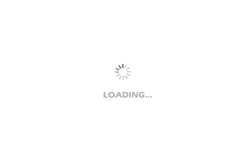
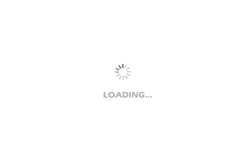
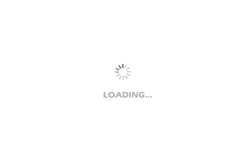
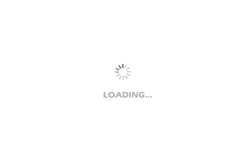
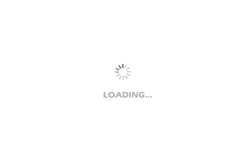
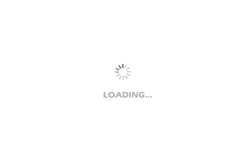
- Popular Resources
- Popular amplifiers
-
Analysis and Implementation of MAC Protocol for Wireless Sensor Networks (by Yang Zhijun, Xie Xianjie, and Ding Hongwei)
-
MATLAB and FPGA implementation of wireless communication
-
Intelligent computing systems (Chen Yunji, Li Ling, Li Wei, Guo Qi, Du Zidong)
-
Summary of non-synthesizable statements in FPGA
- Keysight Technologies Helps Samsung Electronics Successfully Validate FiRa® 2.0 Safe Distance Measurement Test Case
- From probes to power supplies, Tektronix is leading the way in comprehensive innovation in power electronics testing
- Seizing the Opportunities in the Chinese Application Market: NI's Challenges and Answers
- Tektronix Launches Breakthrough Power Measurement Tools to Accelerate Innovation as Global Electrification Accelerates
- Not all oscilloscopes are created equal: Why ADCs and low noise floor matter
- Enable TekHSI high-speed interface function to accelerate the remote transmission of waveform data
- How to measure the quality of soft start thyristor
- How to use a multimeter to judge whether a soft starter is good or bad
- What are the advantages and disadvantages of non-contact temperature sensors?
- Innolux's intelligent steer-by-wire solution makes cars smarter and safer
- 8051 MCU - Parity Check
- How to efficiently balance the sensitivity of tactile sensing interfaces
- What should I do if the servo motor shakes? What causes the servo motor to shake quickly?
- 【Brushless Motor】Analysis of three-phase BLDC motor and sharing of two popular development boards
- Midea Industrial Technology's subsidiaries Clou Electronics and Hekang New Energy jointly appeared at the Munich Battery Energy Storage Exhibition and Solar Energy Exhibition
- Guoxin Sichen | Application of ferroelectric memory PB85RS2MC in power battery management, with a capacity of 2M
- Analysis of common faults of frequency converter
- In a head-on competition with Qualcomm, what kind of cockpit products has Intel come up with?
- Dalian Rongke's all-vanadium liquid flow battery energy storage equipment industrialization project has entered the sprint stage before production
- Allegro MicroSystems Introduces Advanced Magnetic and Inductive Position Sensing Solutions at Electronica 2024
- Car key in the left hand, liveness detection radar in the right hand, UWB is imperative for cars!
- After a decade of rapid development, domestic CIS has entered the market
- Aegis Dagger Battery + Thor EM-i Super Hybrid, Geely New Energy has thrown out two "king bombs"
- A brief discussion on functional safety - fault, error, and failure
- In the smart car 2.0 cycle, these core industry chains are facing major opportunities!
- The United States and Japan are developing new batteries. CATL faces challenges? How should China's new energy battery industry respond?
- Murata launches high-precision 6-axis inertial sensor for automobiles
- Ford patents pre-charge alarm to help save costs and respond to emergencies
- New real-time microcontroller system from Texas Instruments enables smarter processing in automotive and industrial applications
- [Recruitment] Shenzhen foreign companies are urgently recruiting RF antenna engineers, looking forward to your joining
- No more confusion! A guide to choosing a cordless vacuum cleaner
- How to Go from Beginner to Expert in FPGA
- "51 MCU Easy to Get Started Based on STC15W4K Series" 429 pages HD electronic version
- [Raspberry Pi 3B+ Review] GCC Compiles HelloWorld & Lighting Program
- How to improve the hardware delivery cycle
- 【Evaluation of EVAL-M3-TS6-665PN development board】——by landeng1986
- [GD32E231 DIY Contest] (I): Development Environment Construction + TIMER5
- How to use the USB port as an external circuit to power other devices
- Detailed explanation of the three major weapons to eliminate EMC: capacitors/inductors/magnetic beads