According to a survey by the International Energy Agency, Asia and Australia used 1.65 trillion liters of oil for energy in 2004. The survey also showed that since 1990, the demand for oil has been rising every year, causing the price of this nearly exhausted natural resource to continue to rise. Fuel cells As an alternative energy source, it is expected to be used to solve the problem of energy shortage.
Space travel was an early adopter of fuel cell technology. In the early 1960s, proton exchange membrane (PEM) fuel cells manufactured by General Electronics powered NASA's Gemi NI radio receivers and the power systems of the Apollo space capsules. Since then, fuel cell technology has come a long way and is now used in everything from laptops and MP3 players to hybrid cars and even buildings. As fuel cell applications continue to grow, design engineers need to understand not only how the technology works, but also how to test the reliability and functionality of fuel cell stacks. This article focuses on two key criteria for building a fuel cell test system: scalability and isolation.
Testing requirements
A fuel cell is a device that converts chemical energy into electrical energy using hydrogen, the most abundant element on Earth. In a PEM fuel cell (the most commonly used type of fuel cell), there is an electrolyte membrane between a porous anode and a cathode. This electrolyte membrane is made of a special material that allows protons to pass through but blocks electrons. When a PEM cell is in operation, it passes hydrogen and oxygen through the anode and cathode, respectively, to generate an electric current. A contact reaction at the anode breaks down the hydrogen into protons, which travel through the PEM to the cathode. Electrons cannot pass through the PEM, so they follow a circuit around it to the cathode, and the movement of electrons in this circuit forms an electric current.
PEM fuel cells are mainly used in automotive applications, and each battery cell in the battery stack can generate a voltage of 1.1V to 1.23V. So what is the difference between fuel cells and ordinary batteries? Ordinary batteries can only store a limited amount of charge, so their use time is limited. Fuel cells are different. As long as there is a constant supply of hydrogen and oxygen, fuel cells can always provide energy. This ability to continuously generate energy makes fuel cells very suitable for providing energy for cars and buildings. However, some applications that require a very reliable energy source require that the fuel cell be thoroughly tested before use.
Fuel cells are scalable, minimally complex systems that can generate "a lot of power." The flexibility of fuel cells also dictates that a flexible approach to testing them is required to ensure safe, long-term use. Therefore, it is critical to build fuel cell test applications on a modular platform that can add I/O points.
In addition to being modular and scalable, the test system should be able to measure the voltage of the entire battery stack as well as the voltage of each battery cell. In each cell of the battery stack, the flow rate of hydrogen and oxygen through the anode and cathode is different, so each cell provides a different voltage. Therefore, it is very important to monitor these voltages to understand whether each cell is working properly and control the gas flow rate to achieve the best state of energy production. In addition to the gas flow rate, the temperature of the fuel cell must also be controlled. Taking PEM fuel cells as an example, 60℃ to 80℃ is the optimal operating temperature.
Figure 1: Working process of various fuel cells
To ensure reliable measurement of the voltage of the entire battery stack, the test system must have sufficient isolation between the channel and the ground, and the system must have sufficient ability to suppress common-mode signals. Although the voltage generated by each battery cell may not exceed 1V, multiple battery cells stacked together may output very high voltages and currents. High-performance battery stacks often contain hundreds or thousands of cells. Therefore, to accurately reflect the characteristics of the fuel cell stack, the system must be able to perform multi-channel measurements of small voltages under large common-mode voltages (often up to several hundred volts).
Test Method
One approach to testing fuel cells is to use an embedded programmable automatic control (PAC) system that can measure cell voltages and control factors such as gas flow rate and temperature. NI's CompactRIO high-speed CAN connectivity, NI's latest communication technology to show its strength" target=_blank>Modular off-the-shelf solutions such as CompactRIO not only provide these features, but also have more extensive expansion capabilities. CompactRIO adopts a scalable design and uses an open embedded architecture industrial I/O modules with small size, high durability and hot-swappable features.
Figure 2: The NI 9206 can withstand common-mode voltages up to 600V and has up to 10V isolation between two battery cells.
The NI 9206 CompactRIO analog input module for fuel cells features 16 differential channels and a built-in 16-bit 模数转换\'); companyAdEvent.show(this,\'companyAdDiv\',[5,18])"> analog-to-digital converter for measuring battery stacks. The number of channels can be easily expanded by adding more modules to the backplane. To overcome errors introduced by common-mode voltage, the NI 9206 provides 600V of channel-to-ground isolation in its two groups of eight channels. The two groups use the same COM terminal and can achieve 10V of isolation between them. Therefore, the voltage difference between the two groups (each with eight differential channels) on the NI 9206 cannot exceed 10V in total, but the COM terminal itself can be as high as 600V relative to ground. Therefore, the NI 9206 is best suited for measuring battery stacks such as PEMs, where the unit cell measurement value does not exceed 1.2V. In addition, although this module is ideal for measuring individual battery cells, it does not meet the isolation requirements required to test a group of battery cells or measure the total voltage of a battery stack. [page]
When the cell voltage under test is higher than 1.2V or the overall voltage of the battery stack is tested, higher channel isolation is required. A popular choice for building such a test system is the PXI or CompactPCI platform, which combines the electronic bus characteristics of PCI and the rugged Eurocard package of CompactPCI with dedicated synchronization bus and software features. PXI is scalable, and if you want to increase I/O channels, you only need to insert an additional module in the empty slot on the backplane. In addition, the PXI platform is an open industrial standard that has been rapidly adopted in markets that require measurement, control, and automation. These features make PXI very suitable for fuel cell testing.
Figure 3: The voltage of each cell in a fuel cell stack may be only about 1V, but the common-mode voltage (due to the cells lower in the stack) may raise the measurement of a single cell to a higher voltage level
NI PXI switches and digital multimeters (DMMs) can be used to test fuel cell stacks with voltages up to 500V. Since a PEM fuel cell cell typically has a voltage of 1V, such an application would require connecting approximately 500 channels to a single-channel DMM. To build such a system, a set of switch modules can be used with an NI PXI-4071 FlexDMM to measure current and voltage. The signals from the first 98 cells in the stack can be sent out through an NI PXI-2575 98-channel differential multiplexer module. Since this module is rated for 100V, it cannot be used to route signals from cells in the stack that are rated for voltages above that. For the remaining 202 cells, which can have voltages up to 300V, seven 32-channel differential multiplexers, the NI PXI-2527, can be used. Since the PXI-2527 has high channel-to-ground isolation, it can safely switch signals up to 300V. The cell signals with voltages above 300V in the battery stack can be sent to the DMM through the 11-channel 600V differential multiplexer NI PXI-2584. The channel-to-ground isolation of the PXI-2584 is 600V, so it can be used to transmit these small 1V signals in the presence of high common-mode voltages. The flexibility of the PXI platform and the wide variety of optional modules allow test engineers to easily build a test system that meets their specific requirements and can be expanded as needed in the future. At the same time, because the PXI system has much higher channel-to-channel isolation than CompactRIO (up to 300V), it is also very suitable for measuring the cell group of fuel cells.
However, the right hardware is only part of the test system. An ideal test system should have both modular hardware and scalable system-level software. The DMM/switch solution mentioned above contains several different hardware modules, which makes it difficult to build an efficient test program under normal circumstances. NI's LabVIEW graphical programming software solves this problem for most engineers by using the intuitiveness of data flow programming. In addition, LabVIEW also provides users with a configuration wizard in the form of Express VI (virtual instrument), which shortens development time and increases test system flexibility by minimizing the code modifications required when adding additional hardware.
Conclusion
As technology in the fuel cell field continues to advance, society's reliance on scarce natural resources such as oil will inevitably decrease. Investing in fuel cells will not only bring great economic benefits to investors, but also help reduce pollution and greenhouse gas emissions. Once the demand for fuel cell manufacturing increases, the demand for its testing will inevitably increase. Therefore, it is very important to study modular and scalable test systems to meet the ever-changing fuel cell testing needs.
Previous article:Comparison between virtual instruments and traditional instruments
Next article:Using LabVIEW to Rapidly Prototype a Measurement System for Detecting High-Frequency Transients in Power Systems
Recommended ReadingLatest update time:2024-11-17 04:46
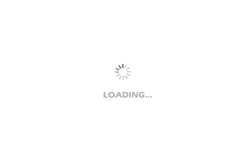
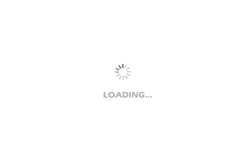
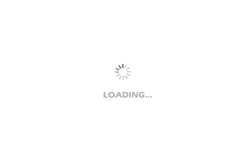
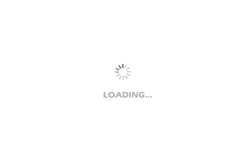
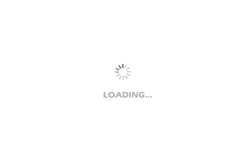
- Popular Resources
- Popular amplifiers
-
100 Examples of Microcontroller C Language Applications (with CD-ROM, 3rd Edition) (Wang Huiliang, Wang Dongfeng, Dong Guanqiang)
-
Arduino Nano collects temperature and humidity data through LabVIEW and DHT11
-
Modern Testing Technology and System Integration (Liu Junhua)
-
Computer Control System Analysis, Design and Implementation Technology (Edited by Li Dongsheng, Zhu Wenxing, Gao Rui)
- Keysight Technologies Helps Samsung Electronics Successfully Validate FiRa® 2.0 Safe Distance Measurement Test Case
- From probes to power supplies, Tektronix is leading the way in comprehensive innovation in power electronics testing
- Seizing the Opportunities in the Chinese Application Market: NI's Challenges and Answers
- Tektronix Launches Breakthrough Power Measurement Tools to Accelerate Innovation as Global Electrification Accelerates
- Not all oscilloscopes are created equal: Why ADCs and low noise floor matter
- Enable TekHSI high-speed interface function to accelerate the remote transmission of waveform data
- How to measure the quality of soft start thyristor
- How to use a multimeter to judge whether a soft starter is good or bad
- What are the advantages and disadvantages of non-contact temperature sensors?
- Innolux's intelligent steer-by-wire solution makes cars smarter and safer
- 8051 MCU - Parity Check
- How to efficiently balance the sensitivity of tactile sensing interfaces
- What should I do if the servo motor shakes? What causes the servo motor to shake quickly?
- 【Brushless Motor】Analysis of three-phase BLDC motor and sharing of two popular development boards
- Midea Industrial Technology's subsidiaries Clou Electronics and Hekang New Energy jointly appeared at the Munich Battery Energy Storage Exhibition and Solar Energy Exhibition
- Guoxin Sichen | Application of ferroelectric memory PB85RS2MC in power battery management, with a capacity of 2M
- Analysis of common faults of frequency converter
- In a head-on competition with Qualcomm, what kind of cockpit products has Intel come up with?
- Dalian Rongke's all-vanadium liquid flow battery energy storage equipment industrialization project has entered the sprint stage before production
- Allegro MicroSystems Introduces Advanced Magnetic and Inductive Position Sensing Solutions at Electronica 2024
- Car key in the left hand, liveness detection radar in the right hand, UWB is imperative for cars!
- After a decade of rapid development, domestic CIS has entered the market
- Aegis Dagger Battery + Thor EM-i Super Hybrid, Geely New Energy has thrown out two "king bombs"
- A brief discussion on functional safety - fault, error, and failure
- In the smart car 2.0 cycle, these core industry chains are facing major opportunities!
- Rambus Launches Industry's First HBM 4 Controller IP: What Are the Technical Details Behind It?
- The United States and Japan are developing new batteries. CATL faces challenges? How should China's new energy battery industry respond?
- Murata launches high-precision 6-axis inertial sensor for automobiles
- Ford patents pre-charge alarm to help save costs and respond to emergencies
- The continuous operation mode CCM and the interruption mode DCM of the inductor
- Free application: ST motion sensor kit worth 638 yuan, advanced machine learning
- Design of Multi-machine Communication Dispatch and Command System with I2C Bus
- Happy Sharing: 51 Programs
- Tetris_Verilog Course Design.rar
- Several questions about MmwaveStudio
- [RVB2601 Creative Application Development] Establish a development environment and run a flashing DEMO
- I would like to ask, in the following picture, what is the best communication method between ZigBee?
- How to Improve Electronic Product Heat Dissipation through Good PCB Design
- The output waveform of the Wien oscillator circuit is abnormal