Introduction At present, power modules are developing in the direction of integration, intelligence and modularization. Power modules provide an ideal interface for the connection between weak current and strong current in mechatronic equipment. In any operating state, the power module needs to be protected to avoid it from being subjected to unacceptable current stress, that is, to avoid the operating area of the power module from exceeding the given safe working area. Operation beyond the safe working area will cause damage to the power module, and its life will be shortened. In severe cases, it will immediately cause damage to the power module. Therefore, the most important thing is to detect the critical current state and fault first, and then respond to them appropriately. The description in this article is mainly for the overcurrent protection of IGBT, but it can also be applied to power MOSFET by analogy.1 Types of fault currents Fault current refers to collector or drain current that exceeds the safe operating area. It can be caused by incorrect control or load. Fault current can cause damage to power semiconductors through the following mechanisms; 1) Thermal damage caused by high power loss; 2) Dynamic avalanche breakdown; 3) Static or dynamic holding effect; 4) Overvoltage caused by overcurrent. Fault current can be further divided into overcurrent, short-circuit current and ground fault current. 1.1 Overcurrent Characteristics: 1) The di/dt of the collector current is low (depending on the load inductance and drive voltage); 2) The fault current forms a loop through the DC bus; 3) The power module does not leave the saturation area. Causes: 1) The load impedance is reduced; 2) The inverter control is wrong. 1.2 Short-circuit current Characteristics: 1) The collector current rises sharply; 2) The fault current forms a loop through the DC bus; 3) The power module leaves the saturation area. Causes: 1) Bridge arm direct short circuit (Case 1 in Figure 1) - caused by power module failure; - caused by wrong drive signal. 2) Load short circuit current (Case 2 in Figure 1) - caused by insulation failure; - caused by human error (such as wrong wiring). 1.3 Ground fault current Case 3 in Figure 1. 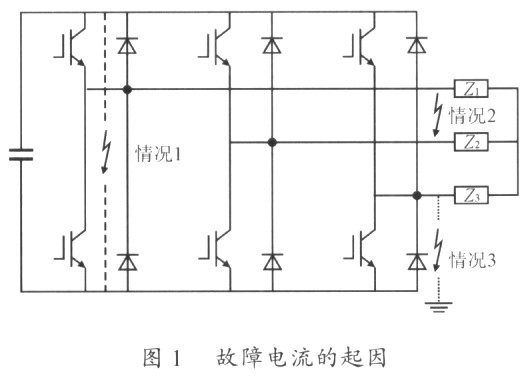 Characteristics: 1) The rising speed of the collector current depends on the grounding inductance and the voltage acting on the loop; 2) The ground fault current does not pass through the DC bus to form a closed loop; 3) Whether the power module leaves the saturation zone depends on the magnitude of the fault current. Cause: Due to insulation failure or human error, there is a connection between the live wire and the ground potential. 2 Characteristics of ICBT and MOSFET under overload and short circuit 2.1 Overcurrent In principle, the switching and on-state characteristics of the device under overcurrent are no different from those under rated conditions. Since larger load currents cause higher losses in the power module, the overload range of the power module should be limited to avoid exceeding the maximum allowable junction temperature. Here, not only the absolute value of the junction temperature under overload, but also the temperature variation range under overload are limiting factors. The specific limit values of several ICBTs and MOSFETs are given by the safe operating area of a typical power module shown in Figure 2. 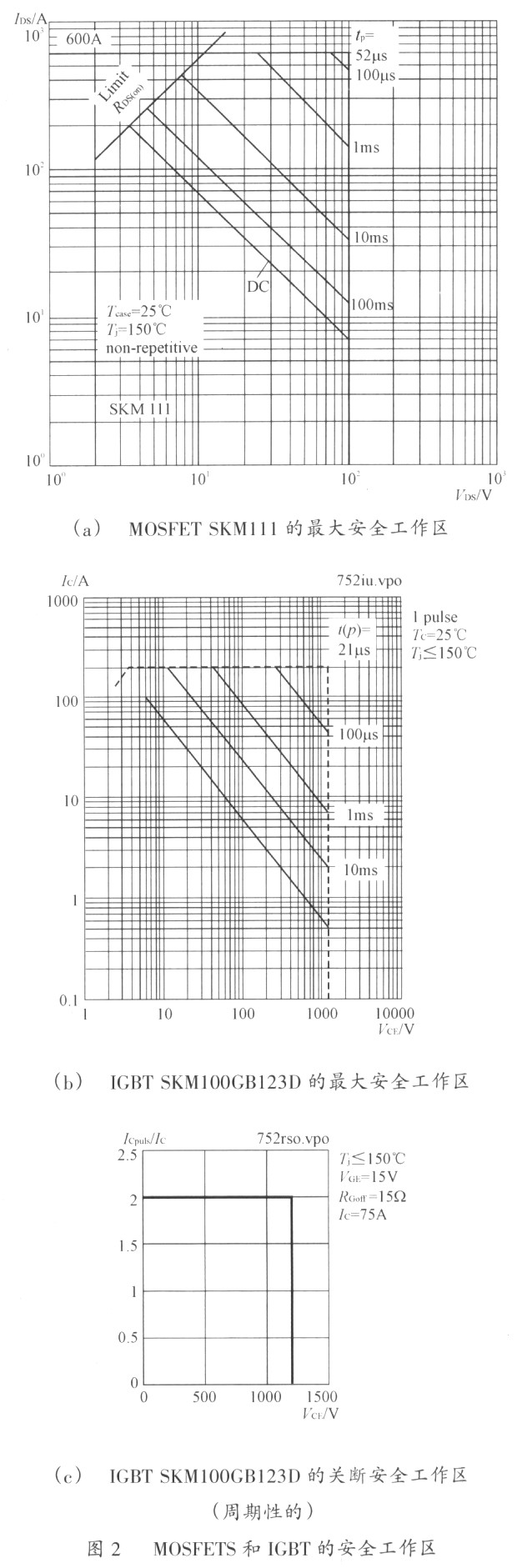 2.2 Short Circuit In principle, both ICBT and MOSFET are short-circuit-safe devices. That is, they can withstand a short circuit under certain external conditions and then be turned off without damage to the device. When examining a short circuit (taking IGBT as an example), the following two situations should be distinguished. 1) Short Circuit I Short Circuit I refers to the power module being turned on in a short-circuited load circuit. That is, under normal circumstances, the DC bus voltage is completely dropped on the power module. The rising speed of the short-circuit current is determined by the drive parameters (drive voltage, gate resistance). Due to the presence of parasitic inductance in the short-circuit loop, this current change will produce a voltage drop, which is manifested as a steep voltage drop on the collector-emitter voltage characteristic, as shown in Figure 3. 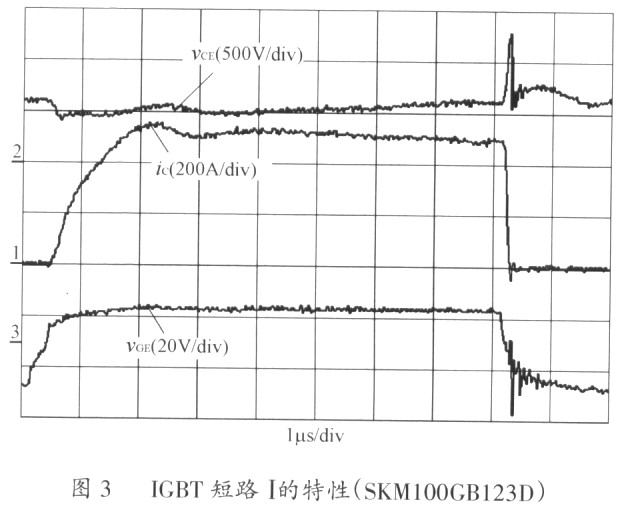 The steady-state short-circuit current value is determined by the output characteristics of the power module. For IGBT, the typical value can reach 8 to 10 times the rated current. 2) Short Circuit II In this case, the power module is already in the on state before the short circuit occurs. Compared with the short circuit II case, the impact on the power module is far greater. To explain this process, Figure 4 shows the equivalent circuit diagram of short circuit II and its qualitative characteristic curve. 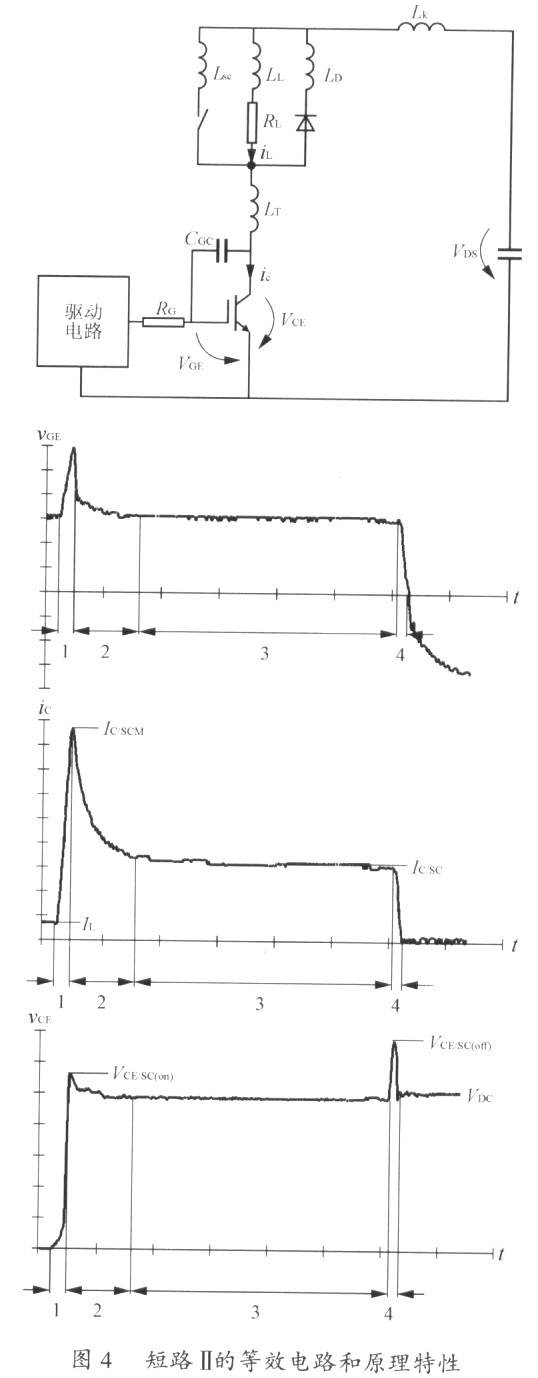 Once a short circuit occurs, the collector current rises rapidly, and its rising speed is determined by the DC bus voltage VDC and the inductance in the short-circuit loop. In time period 1, the IGBT leaves the saturation region. The rapid change of the collector-emitter voltage will generate a displacement current through the gate-collector capacitance, which in turn causes the gate-emitter voltage to rise, resulting in a dynamic short-circuit peak current IC/SCM. After the IGBT completely leaves the saturation region, the short-circuit current tends to its steady-state value (time period 2). During this period, the parasitic inductance of the loop will induce a voltage, which manifests as an overvoltage of the IGBT. After the short-circuit current stabilizes (time period 3), the short-circuit current is turned off. At this time, the inductance Lx in the commutation loop will induce an overvoltage on the IGBT again (time period 4). The overvoltage induced by the IGBT during the short-circuit process may be several times that of its normal operation, as shown in Figure 5. 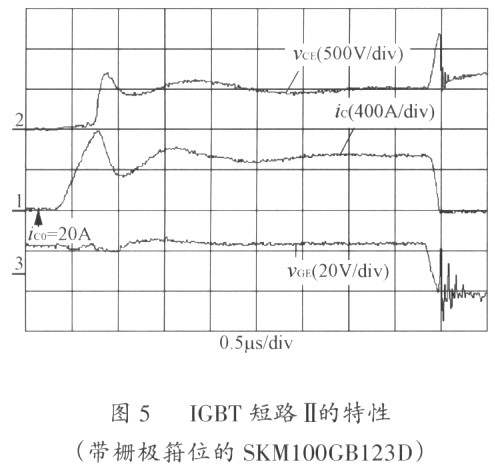 To ensure safe operation, the following critical conditions must be met: 1) The short circuit must be detected and closed within 10μs; 2) The time interval between two short circuits must be at least 1s; 3) The number of short circuits must not exceed 1000 times during the total operating time of the IGBT. Both short circuit I and short circuit II will cause losses in the power module, thereby increasing the junction temperature. Here, the positive temperature coefficient of the collector-emitter voltage has an advantage (also applicable to the drain-source voltage), which allows the collector current to be reduced during the steady-state short circuit, as shown in Figure 6. 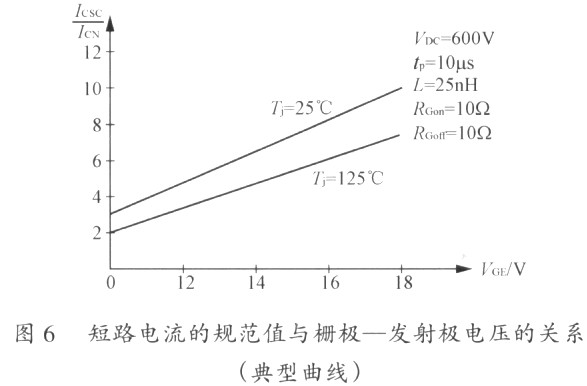 3 Fault detection and protection The fault current in the inverter can be detected at different nodes, and the response to the detected fault current may also be different. Here we will discuss fast protection, provided that the fault current is detected inside the power module and the power module is directly shut down by the driver. The total response time of the power module may be only tens of ns. If the fault current detection is located outside the power module, the fault current signal is first sent to the control board of the inverter, and from there it triggers the fault response program. This process is called slow protection. This process can even be handled by the control and regulation system of the inverter (for example, the system's response to overload). 3.1 Fault current detection Figure 7 shows a voltage-type inverter circuit. Here, the test points where the fault current may be detected are all noted. 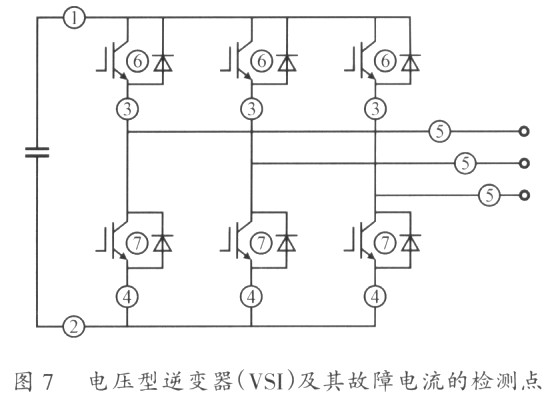 The detection of fault current can be divided into the following categories: 1) Overcurrent can be detected at points ①~⑦; 2) Bridge arm through short circuit can be detected at points ①~④ and ⑥~⑦; 3) Load short circuit can be detected at points ①~⑦; 4) Short circuit to ground can be detected at points ①, ③, ⑤, ⑥, or by calculating the difference between the currents at points ① and ②. In principle, controlling the short circuit current requires fast protection measures to achieve direct control at the output of the drive circuit, because the power module must be turned off within 10μs after the short circuit occurs. For this purpose, the fault current can be detected at detection points ③, ④, ⑥ and ⑦. The measurement at points ①~⑤ can be achieved by measuring shunts or inductive current transformers. 3.1.1 Measuring shunts 1) The measurement method is simple; 2) A power shunt with low resistance (10~100mΩ) and low inductance is required; 3) The measurement signal is highly sensitive to interference; 4) The measurement signal does not have potential isolation. 3.1.2 The current transformer for measurement 1) is much more complex than the shunt; 2) compared with the shunt, the measurement signal is not easily disturbed; 3) the measured value has been isolated. At test points ⑥ and ⑦, the fault current can be detected directly at the terminals of the IGBT or MOSIEET. Here, the protection method can be vCEsat or vDS (os) detection (indirect measurement), or mirror current gun measurement. The latter uses a small part of the sensor to detect the IGBT unit to reflect the main current (direct measurement). Figure 8 shows the principle circuit diagram. 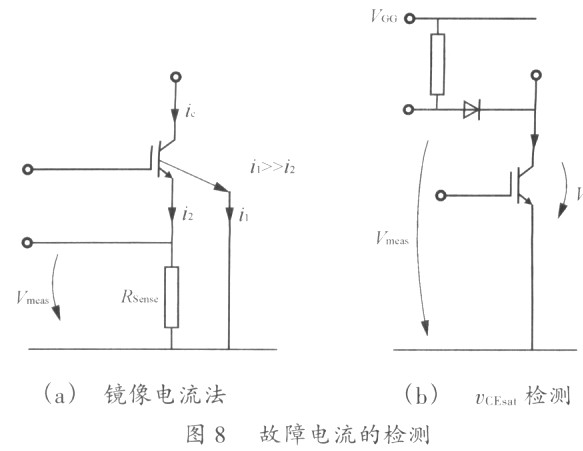 3.1.3 Current sensing with mirror ICBT In a mirror IGBT, a small portion of the ICBT unit is combined with an emitter resistor for sensing and connected in parallel to the current arm of the main IGBT. Once the collector current is conducting through the measuring resistor, its information can be obtained. When Rsense=0, the current ratio between the two emitters is equal to the ideal value, which is the ratio of the number of mirror IGBT units to the total number of units. If Rsense increases, the current conducted in the measurement circuit will decrease due to the feedback of the measurement signal. Therefore, the resistor Rsense should be controlled in the range of 1~5Ω in order to obtain sufficiently accurate collector current measurement results. If the current threshold for shutdown is only slightly greater than the rated current of the power module, the current sensing must be turned off during the IGBT turn-on period (in hard switching circuits) due to the effect of the reverse recovery current peak of the reverse freewheeling diode. If the sensing resistor tends to infinity (Rsense→∞), its measured voltage is equal to the collector-emitter saturation voltage. Therefore, the mirror current sensing is transformed into vCEsat sensing. 3.2 Fault current reduction By reducing or limiting high fault currents, especially in short circuit and low impedance short circuit to ground conditions, the power module can be better protected. As shown in Figure 1, in the short circuit II situation, the high dvCE/dt causes the gate-emitter voltage to rise, which in turn generates a dynamic short circuit overcurrent. The amplitude of the short circuit current can be reduced by clamping the gate-emitter voltage. In addition to limiting the dynamic short circuit overcurrent, the steady-state short circuit current can also be reduced by reducing the gate-emitter voltage. This method will reduce the power module losses during the short circuit, and at the same time, the overvoltage will be reduced due to the lower short circuit current to be turned off. The principle is shown in Figure 9. This protection technology can limit the steady-state short-circuit current of the impact-resistant power module to about 3 times the rated current. 4 Conclusion With the development of power electronics technology, the application of power modules such as IGBT and MOS-FET is becoming more and more popular. In order to ensure safe and efficient operation, overcurrent protection measures must be considered for power modules. First, overcurrent faults should be detected in the shortest time, and then appropriate measures should be taken to protect the power module. Sometimes, it is not the best way to shut down the power module immediately when overcurrent occurs. A very simple dynamic gate control protection method is to reduce the gate-emitter voltage in the case of overcurrent or short circuit of IGBT and MOSFET to slow down the shutdown process. This is the "soft" shutdown process of the power module.
|