Reliability refers to the ability of a product to complete its specified functions within a specified time and under specified conditions . It is an important indicator of product quality. If a product loses its specified functions within a specified time and under specified conditions, it is called product failure or malfunction. The scientificity and rationality of reliability test items, the standardization and rigor of sampling and testing are crucial to the evaluation of the environmental life and quality level of products, the improvement and upgrading of R&D, product iteration, and customer introduction and application evaluation.
Main test items, conditions, sampling and acceptance standards for environmental and life reliability of basic semiconductor silicon carbide devices
The basic semiconductor device environment and life reliability test items are formulated according to different product types, material characteristics and potential customer application environments, and refer to authoritative domestic and foreign standards (AEC-Q101, AQG324, etc.) to develop test items and conditions that meet the company's and customer needs. At present, the company's main device environment and life reliability test items include HTRB, HTGB (MOSFET and IGBT), HV-H3TRB, TC, AC, IOL , etc. Electrical stress testing and physical appearance confirmation are required before and after the test. In accordance with the requirements of the automotive-grade standard AEC-Q101, each reliability item requires 3 different batches. If 77pcs of devices in each batch pass the test with zero failure, it means that the test has passed.
01 HTRB
HTRB (High Temperature Reverse Bias) is mainly used to verify the leakage current of the chip under long-term stability. The test object is the weakness or degradation effect of the edge structure and passivation layer.
HTRB is the most important test item for the reliability of discrete devices. Its purpose is to expose defects related to time and stress. These defects are usually mobile ions in the passivation layer or temperature-driven impurities. Semiconductor devices are highly sensitive to impurities. Impurities will accelerate their movement or diffusion under the action of strong electric fields, and eventually diffuse into the interior of the semiconductor and cause failure. Similarly, after the passivation layer on the surface of the wafer is damaged, impurities may migrate into the interior of the wafer and cause failure. The HTRB test can accelerate these failures and detect abnormal devices.
Taking silicon carbide MOSFET as an example, the test schematic is as follows:
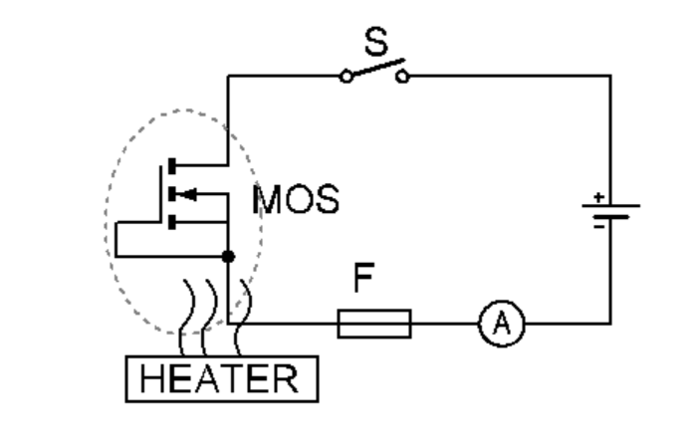
During the test, the leakage current of the source-drain of the SiC MOSFET needs to be continuously monitored. Electrical stress testing is performed before and after the test. If the static parameter test results of the device exceed the specified range, it is judged as a failure.
HTGB (High Temperature Gate Bias) is the most important reliability test for SiC MOSFET , which is mainly used to verify the stability of gate leakage current. The test object is the gate oxide layer of SiC MOSFET. Long-term application of voltage to the gate in a high temperature environment will accelerate the aging of the gate performance. If the gate of SiC MOSFET is subjected to positive or negative voltage for a long time, its gate threshold voltage V GSth will drift.
The test schematic is as follows:
During the test, the gate-drain leakage current of the SiC MOSFET needs to be continuously monitored. If the leakage current exceeds the upper limit set by the power supply, it can be judged as a failure. Electrical stress testing must be performed before and after the test. If the static parameter test results of the device exceed the specified range, it is judged as a failure.
HV-H3TRB (High Voltage, High Humidity, High Temp. Reverse Bias) is mainly used to test the impact of temperature and humidity on the long-term characteristics of power devices. High humidity environment is a great test for the packaging resin material of discrete devices and the passivation layer on the surface of the chip. The resin material cannot block water vapor and can only rely on the passivation layer. The application of three types of stress makes it easier to expose early defects.
There is only one category, H3TRB, in AEC-Q101, and its disadvantage is that the reverse voltage is too low, only 100 V. Basic Semiconductor has raised the standard and set the reverse bias voltage to 80%~100% of BV, which is called HVH3TRB.
Taking silicon carbide MOSFET as an example, the test schematic is as follows:
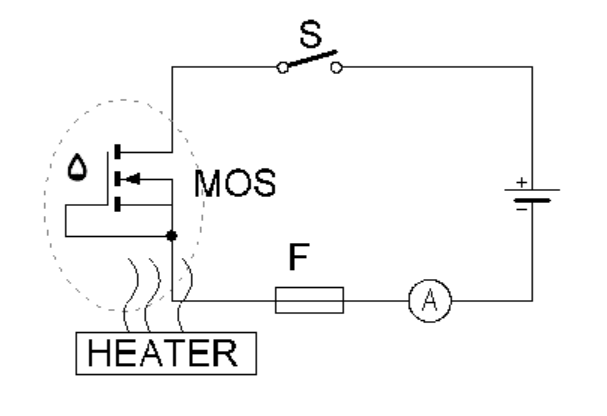
During the test, the leakage current of the MOSFET source-drain needs to be continuously monitored. Electrical stress testing is required before and after the test. If the static parameter test results of the device exceed the specified range, it is judged as a failure.
TC (Temperature Cycling) testing is mainly used to verify the integrity of device packaging structure and materials.
The bonding wires, welding materials and resin materials are all at risk of aging and failure when subjected to thermal stress. The temperature cycle test places the object under test in a temperature chamber and cycles the temperature between -55°C and 150°C (H level). This process applies thermal stress to the packaging material and evaluates the interface integrity of various materials inside the device under the action of thermal expansion and contraction; this project standard is very demanding for silicon carbide power modules.
Taking silicon carbide MOSFET as an example, the test schematic is as follows:
Electrical stress testing must be carried out before and after the test. If the test results of the static parameters of the device exceed the specified range, it is judged as a failure, and the package appearance must be checked for abnormalities.
The AC (Autoclave) test is mainly used to verify the sealing integrity of the device packaging structure. This test puts the object under test into a high temperature, high humidity, and high pressure environment to test the quality of the chip passivation layer and the performance of the resin material. The object under test is in a condensation and high humidity atmosphere, and the air pressure in the environment is high. Moisture can enter the interior of the package, which may cause defects such as delamination and metallization corrosion.
Taking silicon carbide MOSFET as an example, the test schematic is as follows:
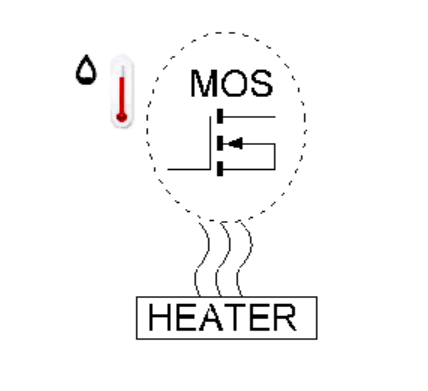
Electrical stress testing must be carried out before and after the test. If the test results of the static parameters of the device exceed the specified range, it is judged as a failure, and the package appearance must be checked for abnormalities.
The IOL (Intermittent Operational Life) test is a power cycle test that places the object under test in a room temperature environment T C = 25°C, passes a current to raise its junction temperature, and makes T J ≧ 100°C, waits for it to cool naturally to the ambient temperature, and then passes a current to raise its junction temperature, and repeats the cycle. This test can cause stress to be generated on the interface between different materials of the object under test, and can find defects such as fracture of the welding surface between the bonding wire and the aluminum layer, delamination of the interface between the chip surface and the resin material, and delamination of the interface between the bonding wire and the resin material.
Taking silicon carbide MOSFET as an example, the test schematic is as follows:
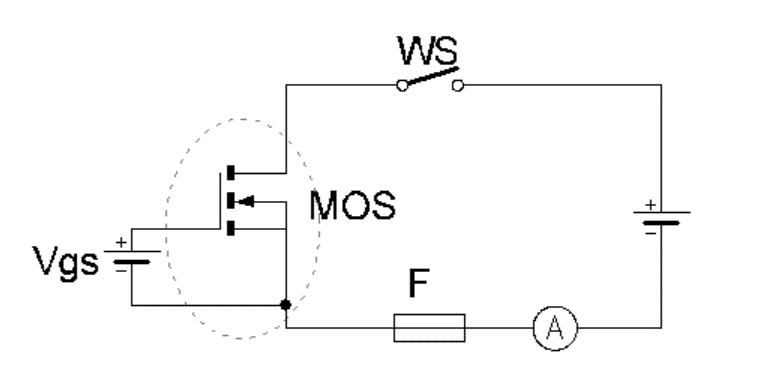
Electrical stress testing is also required before and after the test. If the static parameter test results of the device exceed the specified range, it is judged as a failure and the package appearance must be checked for abnormalities.
Basic Semiconductor 's silicon carbide power device products need to pass the prescribed reliability test before they are put on the market in batches to ensure the long-term stability and reliability of the performance of each device. Basic Semiconductor is equipped with a 1500m2 silicon carbide power device engineering laboratory , focusing on R&D design verification, new materials and experimental technology application, product function test and reliability test. It is a comprehensive laboratory for R&D and testing in the field of power semiconductors.
Basic Semiconductor will continue to aim for zero defects, constantly improve scientific and strict quality control methods, refine technology and product quality, and continue to provide higher performance and more reliable products and services to customers in industries such as photovoltaic energy storage, electric vehicles, rail transit, industrial control, and smart grids.
|