In-depth analysis: Automotive Ethernet DOIP protocol
[Copy link]
Meaning of DoIP
DoIP is not an independent application layer protocol, but is standardized by ISO in the ISO 13400 series of documents. The protocol is regarded as an interface between TCP/IP and higher-level protocols such as ISO 14229 (UDS). In other words, DoIP is a container for diagnostic requests and responses transmitted over a TCP/IP network. There are currently 4 officially released documents, and the relationship between each document and the OSI reference model is shown in the following table. The
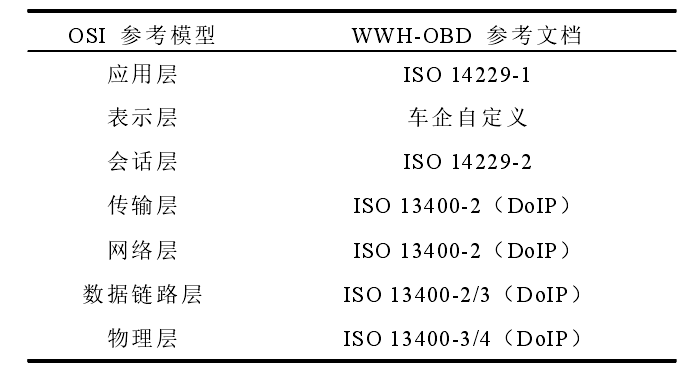
main function of the DoIP protocol is to separate the in-vehicle network technology from the external test equipment and help automobile companies use efficient communication technology that is compatible with the legislative diagnostic protocol. The DoIP protocol is also applicable to the physical layer and data link layer, as shown in the table above. If a node that supports DoIP has an Internet connection, the node supports online remote diagnosis using an IEEE 802 interface connection.
Corresponding to the OSI reference model layering, each document has a different scope of use as follows. ISO13400-1 contains general information, defines the application scenarios of DoIP, etc. ISO 13400-2 describes the transport layer and network services, contains different communication stages of the protocol, and is the main part of the protocol. ISO 13400-3 is a document specifically describing Ethernet wired transmission based on IEEE802.3. ISO 13400-4 is a document used to describe high-speed data link connectors based on Ethernet, and also contains vehicle OBD interface definitions.
DoIP application scenarios
In ISO13400-1, use cases guiding protocol design are outlined, and many typical communication scenarios are described, among which the following four application scenarios are mainly described.
1. Physical medium connection between a single test device and a single vehicle 2. Network connection between a single test device and a single vehicle 3. Network connection between a single device and multiple vehicles 4. Network connection between multiple test devices and a single vehicle The
application scenarios described in this document are mainly designed to meet the basic diagnostic functions of traditional cars, and the focus of the diagnostic scenarios is on the communication between the vehicle network and external devices close to the vehicle (mobile devices connected via LAN or WLAN technology). Cars in the Internet of Vehicles environment need to expand the scenarios mentioned in the document, and even need to propose more complex car network connection methods, that is, interconnected through real Internet networks (routing, etc.), and use such as the Internet to perform vehicle diagnosis away from the vehicle, so as to realize the rich functional requirements of intelligent connected cars.
At present, the functions derived from the Internet of Vehicles architecture based on the TSP platform of automobile enterprises may include: TSP system management, vehicle information management, report management, terminal management, vehicle information statistics, vehicle control, location monitoring, status monitoring, operator management, external system docking, terminal national standard protocol management, car owner terminal mobile phone APP function, AI diagnostic service platform, terminal application mall, dealer terminal hidden sales Heting system, special customer product planning, etc.
Comprehensive intelligent networked car rich practical scenarios and the needs of automobile design and development, 5 main use case groups are identified:
1. Predefined information request (such as vehicle health status monitoring or road adaptability assessment, etc.) 2. Vehicle inspection and maintenance (such as vehicle fault diagnosis and maintenance detection reminder, etc.) 3. Vehicle controller software reprogramming (such as software upgrades during vehicle maintenance and OTA during use, etc.) 4. Vehicle controller production line inspection and preparation (such as the writing of controller software and hardware version numbers and vehicle configuration information during vehicle production, as well as key learning, etc.) 5. Multi-purpose data transmission between vehicles, involving data exchange between vehicles and external devices (through diagnostic functions), external devices may include mobile terminals such as mobile phones and cloud platforms.
DoIP network logic diagram
Generally speaking, the network node under the control of engineers or after-sales personnel is called external test equipment. The external test equipment sends a diagnostic request to the vehicle and then waits for the response of the diagnosed vehicle. However, in the rich use scenarios of intelligent connected vehicles, the diagnostic test equipment may be arranged inside the vehicle to diagnose the vehicle, such as OTA technology and remote diagnosis. In these use scenarios, the diagnostic test equipment will be used as a vehicle node or integrated with other nodes.
DoIP diagnostic test equipment can be any terminal with DoIP function and sufficient storage and processing capabilities, such as a personal computer, laptop or mobile phone. In the Internet of Vehicles scenario, the role of the test equipment may be assumed by the TSP platform or a controller in the car. The node under test can be another node with DoIP function in the network. ISO 13400 classifies nodes with different functions in the DoIP system:
DoIP Entity: DoIP entity is a network node that implements the DoIP protocol (such as a DoIP node or DoIP gateway).
DoIP Gateway: A DoIP Gateway is a network node that implements the DoIP protocol to provide access to the ECUs of its own and its connected vehicle subnets.
DoIP Node: A DoIP node is a network node that implements the DoIP protocol to provide access to itself but does not route DoIP protocol data to the vehicle subnet.
DoIP Edge Node: A DoIP edge node is a node that connects to the Ethernet activation line defined in ISO 13400-3.
External Test Equipment: A vehicle external host that supports the DoIP protocol and is able to access the vehicle subnet and the DoIP entities in the vehicle through the DoIP protocol.
In-Vehicle Test Equipment: A vehicle internal diagnostic test equipment with the same functions as the external test equipment.
The following figure shows the logical diagram of the internal and external networks of the DoIP system.
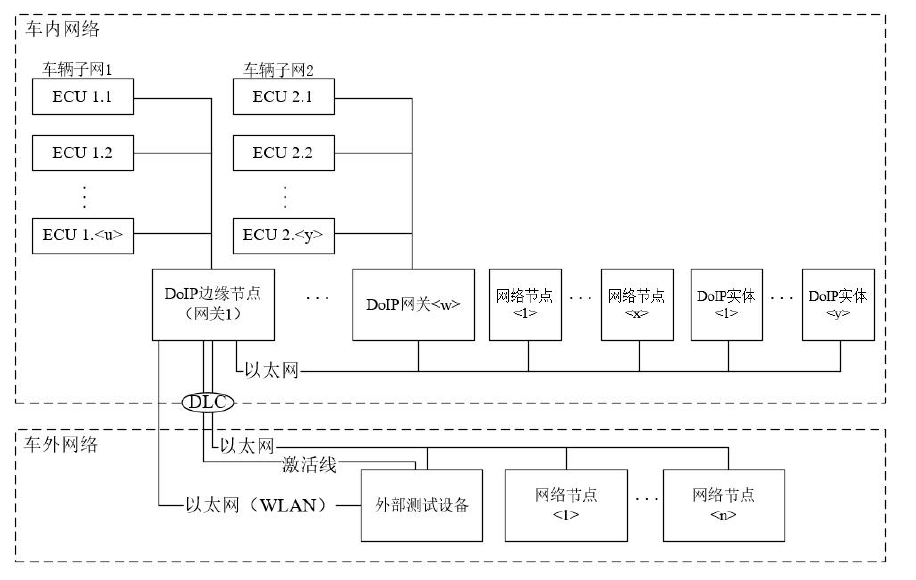
DoIP system physical layer and data link layer
The physical media connection of the in-vehicle Ethernet can use a combination of a connection that complies with IEEE 802.3 100BASE-TX and an activation line. In the use scenario definition of ISO 13400-1, the network configuration has one or more Ethernet links, and may also include wireless links and wireless links.
Ethernet cable is essentially a dedicated medium. If the medium is not well shielded, there is a risk of eavesdropping on communication data by reading the transmission medium radiation. And due to the complex working conditions and high EMC requirements of the vehicle electronic system, radiation may also affect the normal operation of other electronic systems in the car.
On the other hand, the power consumption of the Ethernet controller is large, and keeping it working for a long time increases the consumption of the automotive electronic system. In summary, the DoIP edge node is controlled by the activation line between the in-vehicle DoIP edge node and the test equipment, so as to realize the startup of the Ethernet controller in the node, which can solve the above problems to a certain extent. The following figure is a simplified diagram of the connection between the vehicle interior and the test equipment, showing the connection method of the Ethernet cable and the activation line. The
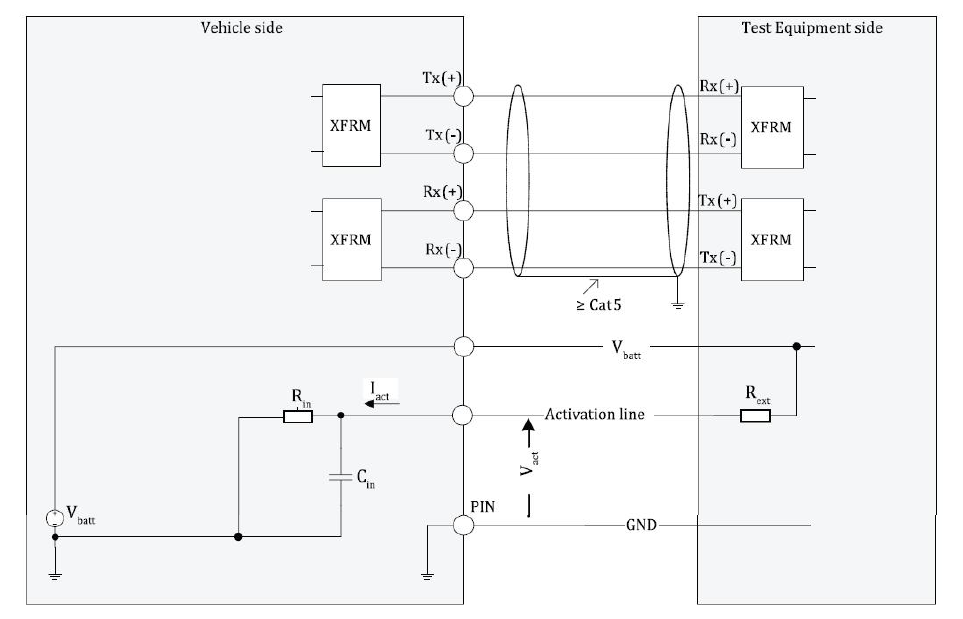
Ethernet diagnostic interface can use an RJ45 connector, and its cable specification is required to be above Category 5. As an in-vehicle node that is directly connected to external test equipment, the DoIP edge node needs to support the detection of physical connection on and off and notify the communication layer of relevant time information. It must support the 100BASE-TX standard specified in IEEE 802.3 while also supporting the 10BASE-T standard 10Mbit/s connection. It is intended as an alternative solution in an environment where a 100Mbit/s connection cannot be established between two Ethernet interfaces. In this case, the connection can still be established at a lower speed.
Ethernet controller activation timing
The control of the Ethernet controller by the activation line is achieved through the change of the activation line voltage. The following figure shows the threshold and timing diagram of the activation line activation voltage. The test equipment activates and deactivates the Ethernet controller in the DoIP edge node by controlling the change of the activation line voltage.
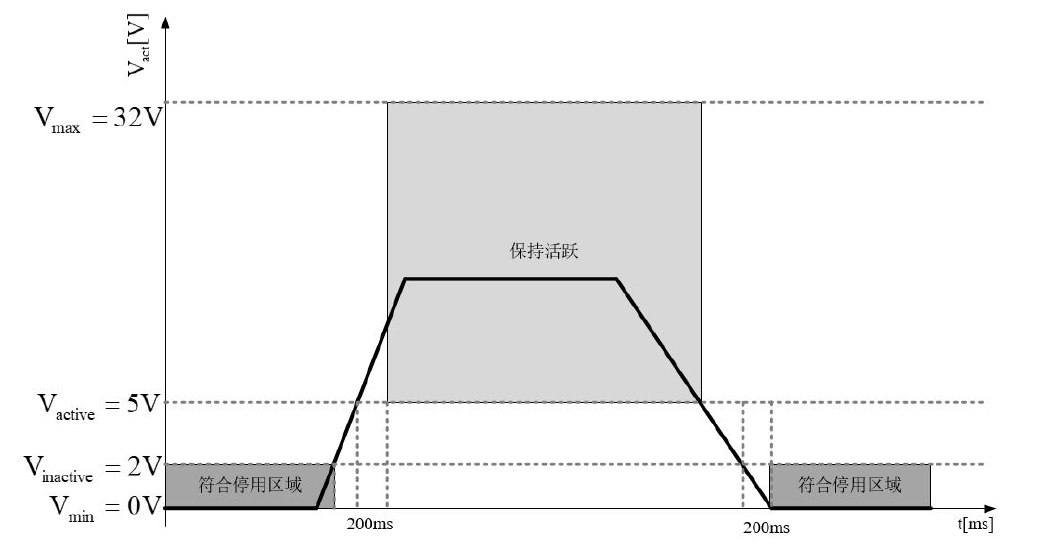
The entire activation timing is divided into three parts: deactivation, activation, and deactivation:
The deactivation voltage threshold is 2V, which means that a voltage below 2V activates the Ethernet controller of the DoIP edge node. The purpose of selecting 2V is to avoid random activation caused by ground offset and electromagnetic interference.
Keep the Ethernet active voltage threshold at 5V. The Ethernet controller should be activated and maintained when the activation voltage reaches between 5V and 32V and maintains for 200ms.
When the activation line voltage drops to the deactivation voltage threshold and maintains for 200ms, it is considered that the Ethernet controller can be deactivated.
The content of this article comes from Yanzhi Automobile and the copyright belongs to the original author.
|