Analysis of MCU microcontroller in the core technology of electric scooters
[Copy link]
If the components of an electric scooter are disassembled and priced one by one, the cost of the motor and control system is the highest. At the same time, they are also the "brain" of the electric scooter. The start, operation, advance and retreat, speed, and stop of the electric scooter all rely on the motor control system in the scooter.
Electric scooters can run quickly and safely, and have high performance requirements for the motor control system and also have high requirements for the efficiency of the motor. At the same time, as a practical means of transportation, the motor control system is required to withstand vibration, tolerate harsh environments, and have high reliability. The
conventional scooter control system hardware design is shown in the figure below, which mainly includes drive MCU , gate drive circuit, MOS drive circuit, motor, Hall sensor, current sensor, speed sensor and other modules.
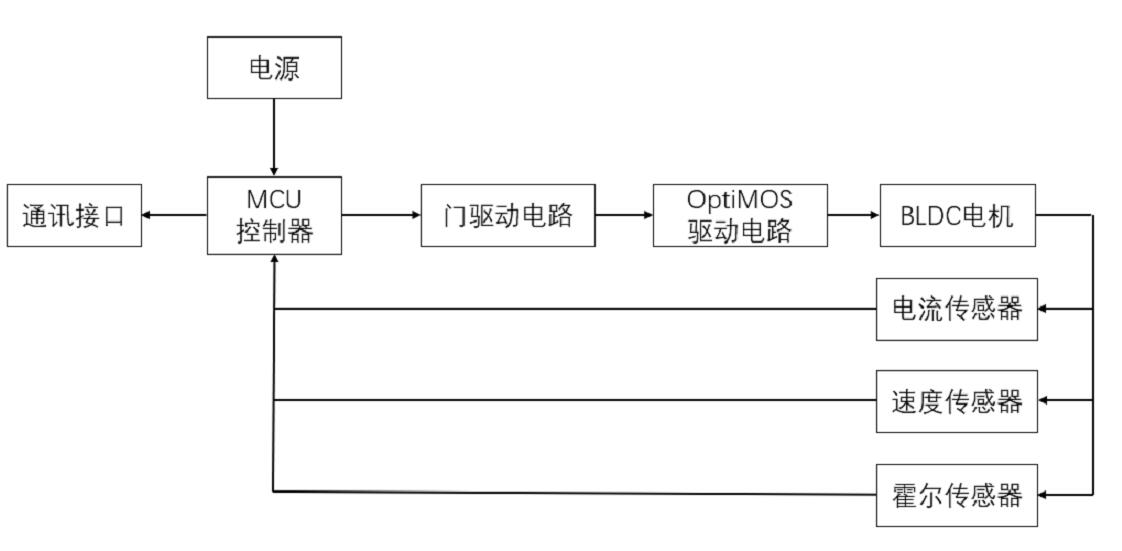
The MCU works by powering on the power supply, and communicates with the power supply and power module using the communication interface and charging module. The gate drive module is electrically connected to the main control MCU and drives the BLDC motor through the OptiMOSTM drive circuit. The Hall position sensor can sense the current position of the motor, and the current sensor and speed sensor can form a dual closed-loop control system to control the motor.
After the motor starts running, the Hall sensor senses the current position of the motor, converts the position signal of the rotor magnetic pole into an electrical signal, provides the correct commutation information for the electronic commutation circuit to control the switching state of the power switch tube in the electronic commutation circuit, and feeds the data back to the MCU microcontroller .
The current sensor and the speed sensor form a dual closed-loop system. The speed difference is input, and the speed controller will output the corresponding current size. Then the difference between the current and the actual current size is used as the input of the current controller, and then the corresponding PWM is output to drive the permanent magnet rotor to rotate continuously for commutation control and speed control. The use of a dual closed-loop system can enhance the anti-interference ability of the system. The dual closed-loop system increases the feedback control of the current, which can reduce the overshoot and oversaturation of the current, and obtain a better control effect. It is the key to the smooth movement of the electric scooter.
Some scooters are also equipped with an electronic anti-lock braking system. This system detects the wheel speed through the wheel speed sensor. If it detects that the wheel is in a locked state, it automatically controls the braking force of the locked wheel to make it roll and slide (the side slip rate is about 20%), ensuring the safety of the electric scooter owner.
|